Can You MIG Weld in the Wind?
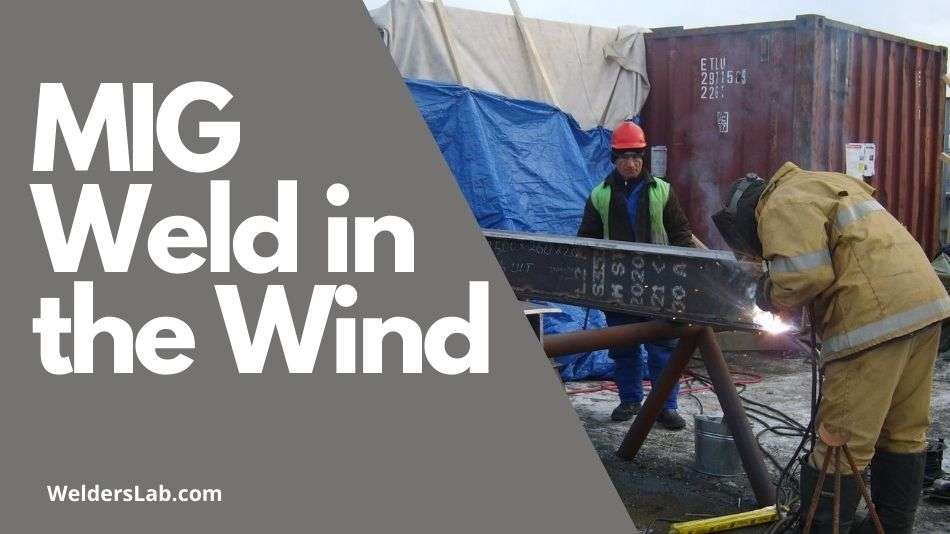
Welding can take place in any number of locations and environments. You may be welding in a workspace booth, in a small or tight space, in an open area, or even outdoors. As a welder, you must be prepared to deal with the circumstances at hand no matter what they may be.
When it comes to lessons learned as a welder, I learned early in the game that you have to be able to adapt to your surroundings. If I’m working in a tight space, what will I need to make it work? What kind of protection should I have?
In a perfect world, when I weld outdoors, the weather is always nice and beautiful and there is never any wind. But let’s be real, chances are the perfect weather is just not something I will see the majority of the time. Whether I’m facing wind or rain or some other adverse effect, I have to know how I can work with these issues?
Can you MIG weld in the wind? Yes, you can weld in windy conditions but you will need to block the wind around the weld to protect the shielding gas. If too much of the shielding gas is pushed away from the weld it will cause porosity to form creating a weak weld.
In this guide, we will discuss everything you need to know about can you MIG weld in the wind and what happens when you MIG weld in the wind. We will cover some basic tips and steps that you can take as well as what to expect when you have the wind working against your welding job.
Let’s get to it?
Can You MIG Weld in the Wind? The Ultimate Guide
It’s challenging to do many different things in the wind and MIG welding, particularly, happens to be one of those things. Just consider you have gas and flame, hot metal, and possibly sparks. So, ask yourself a common-sense question and consider how all of these elements could possibly combine with wind?
Consider rather the risks or possible defects of welding (of any kind) in the wind and then take it from there. What can you do to make the scenario go as smoothly as possible and what issues can you expect to run into?
I know that’s a lot of questions to ask yourself but that’s why we’re here. To cover these questions and ensure you’re fully prepared for anything you might have to face in a windy situation.
According to the American Welding Society, you are not to weld in excessive winds when the wind velocity is more than 5 miles per hour.
This rule also calls into a place that you can weld if the weld is covered by a shelter. The shelter must be of material and shape to reduce the wind velocity within the allowable range.
What Happens When You Weld in Windy Conditions?
The primary problem with welding in the wind is a matter of safety when it comes to the restrictions placed by the American Welding Society.
But what exactly happens when you weld in the wind? For starters, you’re much more likely to have porosity in your weld, in fact, you can almost guarantee you will have this issue. The wind will affect your penetration and the quality of your weld.
One of the issues with welding in the wind is that the wind will blow your shielding gas. If the shielding gas is being blown away, you’ll end up with a lackluster weld, if you can even get a weld at all.
Ultimately, the wind will make your welding process a disaster! But wait, that does not mean you simply can’t do the weld. It means you need to learn how to approach doing the weld to protect it from the wind.
4 Tips for MIG Welding in the Wind
There are a few things you can do that will help you be able to weld in the wind. The primary concern here is that the wind will blow away your shielding gas and your weld will be ineffective or contain a lot of porosity.
What can you do about it? Remember that in the guidelines earlier, the American Welding Society provided that if you can shield your weld to reduce the wind velocity at the point of your weld, then you can do the weld.
So, here are some tips that may be helpful for you if you find yourself in an outdoor situation and you have to work in the wind.
1. Welding Blanket
If you are able to, you should consider setting up a welding blanket. Most welding blankets can be hung so you can hang up a welding blanket that will block the wind where you’re working.
This works almost like a thin wall and will reduce the wind so you can do your weld.
Most welders carry welding blankets with them to various job sites or keep one in their tool bags. The challenge here will be whether or not you have somewhere to set up or hang the blanket that will effectively block the wind.
Be creative if the space allows. You can always move around if necessary. Obviously, moving around may not be an option with all outside welding jobs but be as flexible as you can. A welding blanket is a simple solution.
2. Place a Shield
Set up a shield or even a blind to block the wind from your weld location and protect the shielding gas.
You can purchase welding shields but you could also make your own. Some welders use something as simple as a slash of cardboard to block the wind.
The idea is, you’re shielding your weld from the wind appropriately. Use whatever barrier you can make work to protect your shielding gas from the wind and proceed with your weld.
Get creative. You don’t necessarily have to have anything huge. Consider the tools and items you carry with you from job to job that you might be able to use for protecting the shielding gas.
Some welders carry dustpans for cleaning up. You can prop, set, or hang a dustpan to protect your weld. It’s small but you can move it as you move with the weld if you need to. It will serve as a wind block.
3. Switch to Flux Core
If you go fully prepared to every job site, then it should be easy for you to switch to using flux core wire for your weld.
With flux core, you don’t have to use any gas so it takes away the shielding gas issue that the wind can cause for welding jobs.
This is a simple switch and it works if you’re in a pinch. Keep a small spool with you in your tool bag so you’re prepared if you need to make the switch.
If you notice the wind is blowing with any considerable strength, just make the switch. You will be happy you did when you get a successful weld.
4. Turn Up the Gas
Be cautious with this tip. This tip is meant for minor repairs and small welds and not for anything that is meant to be structural or load-bearing.
If you’re in a pinch and you just have a small repair to make on something simple or decorative, this can be a suitable solution for you. Turning up your gas flow can give you the extra push you need to get that weld done quickly and move on.
Remember, this is not a top recommendation and should only be considered when you’re in a bind for a suitable situation.
FAQ Section
Can You Stick Weld in the Wind?
Stick welding does not require shielding gas and therefore is much more reliable in some windy situations than MIG welding.
You can stick weld in windy situations that are up to 35 MPH.
Anything higher than that becomes a bit of a safety issue but this gives you far more leeway than MIG welding restrictions.
Can You TIG Weld in the Wind?
TIG welding is going to be very similar to MIG welding when it comes to windy situations.
TIG welding also requires shielding gases, which means you should take the same factors and tips into consideration if you are TIG welding in a windy situation.
Conclusion
MIG welding in the wind is not a desirable condition. It can cause a lot of problems for you and effectively make your welding efforts worthless or frustrating.
However, we know that Mother Nature has a mind of her own so we just need to be prepared.
If you find yourself facing the wind and needing to make a weld, just be sure to take into practice and consideration some of the tips and information I’ve shared in this guide.
This will help you get the weld done and be on to your next duty in no time.