What is the Best Way to Weld Upside Down – Tips, Techniques, and Concerns
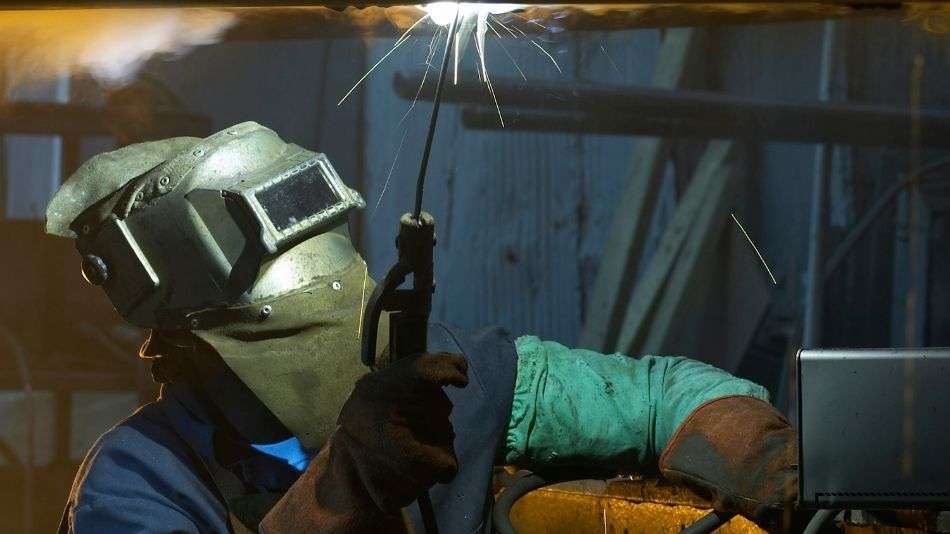
Welders have many unique methods to get a job done. One method is welding upside down, also known as overhead welding. This method is sometimes necessary to get a good result.
When you’re welding upside down or overhead you’ll want to keep the weld in front of you and slightly above eye height. This will allow you to see the weld without actually having it directly over you and having sparks and slag hit you on your head. When welding keep the puddle moving to avoid dripping.
The processes of MIG welding and stick welding are slightly different, and some methods prove to be very effective. Knowing how to control speed is a must. Effectively controlling the welder with the proper procedures are sure to get the job done right the first time.
The Best Way to Weld Upside Down
Also known as an overhead weld, welding upside down can be a great challenge. This is especially true for a welder that has not used this technique before. The reason for the name of upside down, or overhead weld, is because the welder is actually above the head of the person welding.
It is very important to line up the body of the welder with the welding machine precisely. Without the proper angle, the task can be very daunting. The weld should always be focused in front of the forehead.
Whenever possible, the welder should find a point to brace their hand. Steadiness is the key to performing a good, clean, and accurate weld. Sometimes, depending on position, it is necessary to use one hand on the welder and keep the body braced with the hand.
If it is possible, wether MIG welding or stick welding, it is best to have both hands on the welder. Similar to steering a motor vehicle, a person will undoubtedly have more control if both hands are able to be used.
It is important to keep a clear focus on the weld pool at all times, as well as the progress being made. Sometimes, overhead welding can be a dangerous proposition. Things may need to be changed or altered rapidly in some cases.
Stick Welding
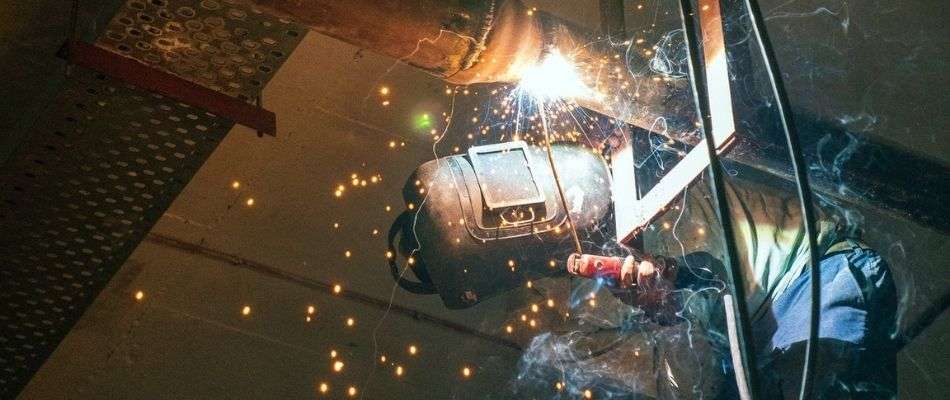
When working with a stick welder, it is important to keep the welder straight up and down. Ideally, as close to a 90 degree angle as possible is the best angle of approach.
It is best to keep the welding slow, and move the welder from down to up (uphill). The reason for this is because this method gives the best possible penetration. By having the weld solid, it is unlikely to have to go back and fix mistakes later.
It is also important to note that for stick welding upside down, amperage settings should be kept low. By keeping these settings low, there is less of a danger of falling debris.
A welder should always remember that when they are welding upside down, gravity is working severely against them.
MIG welding
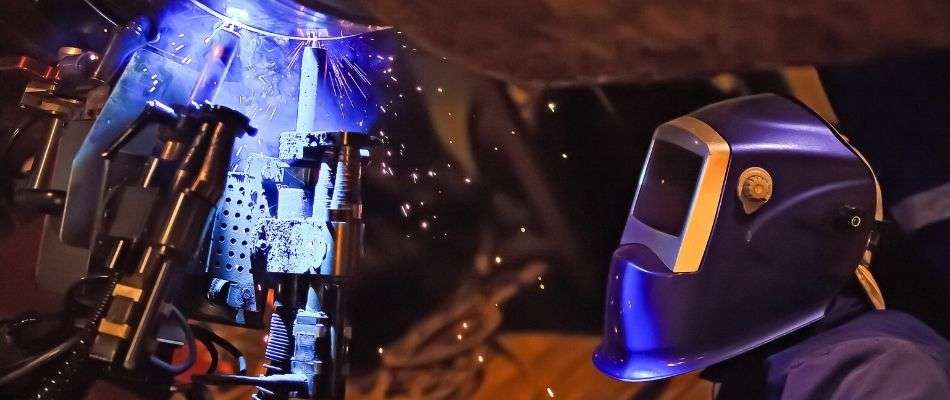
Mig welding is similar to stick welding in the angle, but rather than holding the welder straight up and down, it should also be tilted. The best approach is straight up and and down, and slightly tilted back towards the person welding.
According to many welders, MIG welding overhead is easier than stick welding overhead. There is more control over the weld pool, and the user can easily stop and start as needed to view the weld.
Finally, keep the weld up and in front of you never directly over you. This could result falling sparks and slag to land on you.
3 Techniques for Both MIG and Stick Welding
Positions are important to remember since they differ. However, some aspects are very similar. It is important to go back and forth to focus on the weld.
Sparks can fly down, or a part may not be covered as much as it should be. By focusing on the weld itself, and pausing as needed, a welder is more likely to catch an error that could take place.
1. The speed of the welding machine
It is important to keep the welding machine speed set as perfect as possible. This is in common with every welding position and technique. It is entirely possible to overspeed a welder, or not go fast enough.
The rate should be carefully calculated and dialed in to prevent the weld pool from dripping. The molten metal material can pose a very dangerous risk as gravity will force it to fall.
Also, the weld will not be eye appealing or effective if the rate of speed on the welder is improperly adjusted. It may take a few practice attempts, but once calculated, the proper speed should be locked in.
2. Keep Your Welds Short
If you’re new to all of this consider keeping your welds short. Don’t try to weld the entire bead in one shot. This will allow you weld in short burst and minimize the dripping.
I’ve had slag land on my arms, welding sparks get in my ears, and it can be painful. The best way I’ve found to do this is weld in short burst.
Once you get your first pass done you can start to lay longer beads down that will allow you to create a stronger penetration.
3. Turn Your Amperage Down
Finally, you’ll want to keep the amperage down and keep your weld a little colder. The hotter you weld the easier it will be for the weld to drip.
This doesn’t mean you need to turn the amperage all the way down but rather just slightly less then you normally do to keep a smoother weld.
Overhead Welding Safety Concerns
Without a doubt, welding upside down can be a very dangerous feat. If not armed with the proper safety gear and common safety knowledge, this welding technique can prove to be very dangerous. It is always better to be prepared and focus on safety measures at all times.
Gravity naturally pulls everything down. Similar to a penny falling off a table, the sparks from the weld pool will be rapidly falling. This slag and spatter can be severely dangerous.
Quick Tip: Keep all flammable materials and chemicals far away from the welding site. These obstacles can create a serious fire hazard or explosion. These sparks can also harm a person’s skin and cause burns or lacerations.
As well, if the weld pool begins dripping, it can cling to the skin and cause a serious burn. It is important to remember safety training and use common sense when welding upside down.
The position of the body is crucially important to safety. A person should be close enough to the welding area that they can easily control the welder. However, this should be done reasonably close.
The arms should be as low as possible, and not extend too far. Sometimes laying on an elevated item will help a person get closer to the welding site without overextending their arms. If the person’s arms are extended to far, it can cause fatigue.
When a welder gets fatigued, they are more prone to accidents. Whether it be dropping the welder or messing up the weld, fatigue is something to avoid. If pieces of the weld pool fall on the skin due to unsteadiness, it can be especially bad news.
A person should never be eye level with the weld. They should be able to see the weld perfectly, as lined up with the forehead, but directly in front of the eyes can be a great hazard. Dirt and weld splatter can get directly into the eyes.
Safety Gear for Overhead Welding
Here are just a few things I recommend doing.
1. Welding Helmet with Hood
A welding helmet is one of the most important pieces of safety equipment for any type of welding, especially overhead welding. Debris and sparks will be falling due to gravity, and these hazards should never come in contact with the face or eyes.
It is hard to watch the progress of an overhead weld. For this reason, both the inside and outside of the helmet lenses should be clean. If the lend is dirty or cloudy, the location of the weld pool or welder itself can be distorted.
You’ll also want to have something to cover the top of your head. This could be as simple as a welding cap with a bill on it. This will keep the sparks and slag from going down your back
2. Welding Apron
A welding apron is very important as well. These aprons have flame-resistant qualities. Slag will undoubtedly fall on the body at some point, even if it is just light sparks. The apron should always be worn snugly above the regular clothes.
While a scary situation, if the welder falls on the person using it because they lose their grip, an apron will save them from serious burns or other injuries. When possible, a leather apron should be used. This material is tried and true, and offers the most protection.
Leather aprons also consist of heavier material, so it creates a sort of “shell” on a person that a standard apron does not provide.
3. Leather Work Boots and Jeans
Heavy-duty work boots are very important to wear as well. They should preferably be flame resistant and have thick souls. The boots should be worn at all times when welding is being performed.
Though not a strict requirement, it is best to wear flame-resistant pants. This creates extra protection for the person welding.
There is a proper way as well to wear the boots and pants together. The pants should never be tucked into the boots. Falling sparks or slag can get stuck inside the boot and cause severe burns or injury.
It is important to always keep the pants leg over the top of the boots. This will prevent any sparks from getting down your boots. I’ve had this happen to me a few times and the worst part about this is that it doesn’t stop burning once it gets down inside your boot.
In Conclusion
Overhead welding, or upside down welding, can be a daunting challenge.
There are different methods of approach whether a person is MIG welding or stick welding. With patience and the proper techniques put into place, it can be a success and is often required to get the job done.
It is very important to always use caution, common sense, and the proper safety gear. By doing this, the weld should be a success.