What Kind of Wire Do You Use for a MIG Welder?
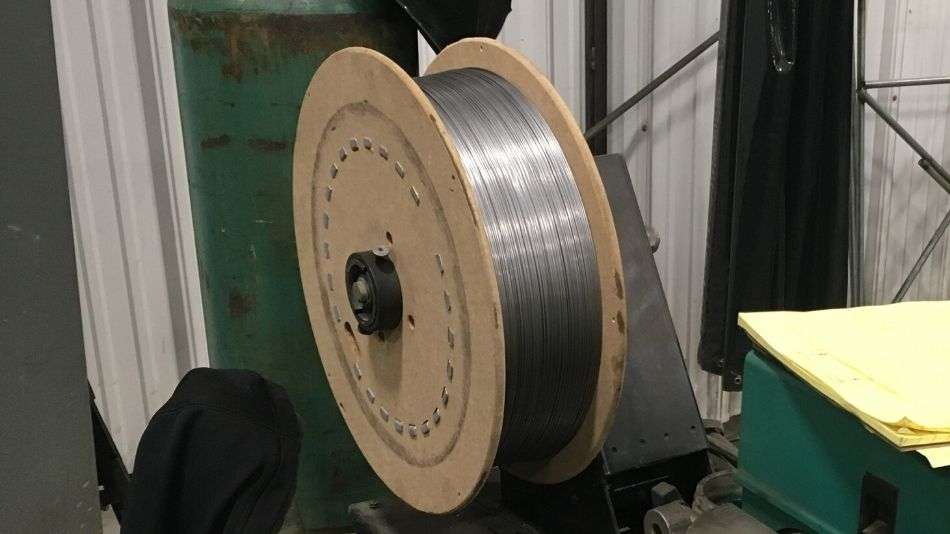
When you’re new to welding, it can feel completely overwhelming. Everyone seems to be talking in code. You’ve hard to learn all about the multiple types of welding you can perform. MIG welding seems to be the easiest for beginners, the most convenient, and the most closely aligned with the reasons you’re learning to weld.
You’ve looked over a lot of different tutorials and guides about how to weld and taken a few classes. You’re feeling a bit more confident and have started learning to crack the complicated code that comes with welding vocabulary. Unfortunately, there’s still one mystery remaining!
Everyone talks about MIG wire as though it is a given that you understand what it is and how it functions.
You’ve seen terms like wire spool and drive rolls tossed around, and all these barely distinguishable numbers keep cropping up, but no one ever slows down enough to explain the difference between .030 and .035 wire or what you should be using for your welds!
That’s why we wrote this complete guide. We will cover all of those lingering questions you might have regarding MIG wire. We go over the different sizes and types of wires, their advantages, and disadvantages, and when to use which type of wire on your project.
We also answer a few remaining questions that are frequently asked and left unanswered. By the time you finish our guide, you will know everything you need to know to get started with your welding project and confidently buy and feed the right wire into your welder!
What Kind of Wire Do You Use for a MIG Welder?
It is crucial that you select a high-quality MIG wire when making your selection.
These wires are far more forgiving of errors in technique that beginners may have, and they will produce a very sound weld under less than perfect conditions.
For example, if a beginner hasn’t fully cleaned their plate and surface contaminants are remaining, the right MIG wire can take care of that issue.
The right MIG wire will also provide better accuracy when wires are being placed and more consistency overall, so you don’t have to go back over your work multiple times.
MIG Welding Wire Sizes
There are several different wire sizes with MIG welding. Most MIG welders will come with a roll of flux cored wire so you will need to buy specialized MIG wire for this type of welding. As a good rule of thumb, thicker wire is better for thicker metal and vice versa.
For higher quality welds, you will probably find that cranking the machine up on the thin wire and then bringing it down to a very low setting for thicker wire will result in the best possible welds.
Here are some guidelines for choosing wire thickness, but just make sure that you’ve checked the door inside your MIG welder (or your users manual) to make sure you’re following their specific recommendations.
Wire Sizing:
- 0.23’’ wire – This wire is for very small welding machines. It is typically used for welding thin sheet metal from 24 gauge to around 16 gauge.
- 0.3’’ wire – This wire is usually what is included in your MIG welder. It’s a great option for welding sheet metals up to 1/8’’ thick.
- .35’’ wire – This wire will properly weld metals that go up to ¼’’ in thickness, so it’s probably the best choice for beginners.
- .045” wire – This wire is best for thick metals that are ¼” thick or more. It’s what you would use for industrial welding.
Types of MIG Welding Wire
There are 2 main types of wire. Flux-cored wire and solid electrode wire. They each have their own advantages and disadvantages.
#1 Flux-Cored Wire
Flux-cored wire electrodes are built for gas-shielded and self-shielded welding projects. The gas-shielded wire needs an external shielding gas, and self-shielded doesn’t. Usually, MIG welding for beginners uses self-shielded wires.
The flu coating will solidify more rapidly on gas-shielded wires than molten weld material. This creates a shelf that will hold the weld pool when you’re using vertical or overhead welding positions.
These instances are great for gas-shielded flux wires, as they tend to use thicker metals. This wire makes it easy to remove slag.
Self-shielding wires don’t need an external shielding gas. This electrode protects the weld pool as gas gets generated from burning the flux wire.
This type of wire produces its own protective shield, so it doesn’t need an external gas tank. This makes it very portable and much easier to handle.
Flux-cored wire electrodes have some real advantages. They allow a higher rate of deposition. They work well in windy conditions and outdoor settings. They can make FCAW possible in any position using the right filler materials. They also create a very clean and reliably strong weld.
There are a few concerns with this weld, though. These are not immune to the possibility of creating an incomplete fusion that exists with any welding. These are also vulnerable to cracks in the weld or slag incursion. On occasion, these may melt your contact tip.
If an electrode spends too much time in contact with the base metal, it will fuse the tip to the base. This can also encounter high levels of porosity if the gas can’t escape the weld are before the metal hardens.
#2 Solid Wire Electrodes
MIG welds typically use solid wire electrodes. These require a shielding gas, that comes from a pressurized gas bottle. Most of the time, argon or a 75%/25% Argon to Helium mixture is used for the gas. This shielding gas will protect the molten weld pool from any contaminants found in the atmosphere while you weld.
These electrodes are typically made from mild steel that gets plated with copper. The copper plating prevents oxidation and helps electrical conductivity. It also helps the lifespan of your welding contact tips.
Solid wires are a great choice when working with thinner materials like sheet metals. They reliably create clean, strong welds. These wires don’t work well in the wind, though.
Quick Tip: Exposing the shielding gas to the wind could compromise your weld’s integrity and strength.
What Kind of Welding Wire Do I Need?
The sizing guidelines above gave you a bit of a reference for the type of wire you will need to use for various projects. It is important to select your wire carefully and avoid some common mistakes.
When MIG welding mild steel, the ER70S-3 and the ER70S-6 from Lincoln are the most common options. These wires are designed carefully to handle 70,000 psi of tensile strength.
ER70S-3 is usually what you select when you’re working with a clean material that is free of any oil or rust. It’s a great choice for avoiding the silicon islands that often form on top of welds and give them a glassy look.
These islands need to be avoided at all costs because paint layers will flake off of them and welding that requires multiple passes, they will show up on x-ray scans as slag incursion and require you to rework your weld because they are defects.
If you’re working a plate that has mill scale or surface contaminates, use the ER70S-6 wire instead. This wire actually incorporates deoxidizer into the wiring to prevent those issues. The deoxidizer absorbs new oxygen, allowing it to vaporize into the arc instead of forming scale oxides.
This wire is also better at transitioning work and creates a smooth transition from the base metal to the weld. These wash-ins (or tie-ins) may be required in any welding project that is subject to fatigue.
Make sure the wire you select has a consistent chemical composition. This will offer more consistent performance. This also provides a more stable arm with greater quality control.
This allows new welders to set then forget their procedures instead of constantly re-adjusting to account for differences in chemical composition.
When comparing wires, the best choice is usually determined by the type of welding job you are performing and the location where you’re doing the work. Both types of wires can make sound welds that have beautiful beading when proper technique is applied.
Thicker metals and outdoor jobs tend to do better with flux-core welds, while thinner metals and outdoor jobs will do well with solid wire electrodes.
The solid wire electrodes that MIG welding uses are less portable than flux-cored wires, but they are also more forgiving of poor techniques. Both are easy to use once you get the hang of it, but MIG welding is much more affordable.
Switching Wire Sizes – Use Caution
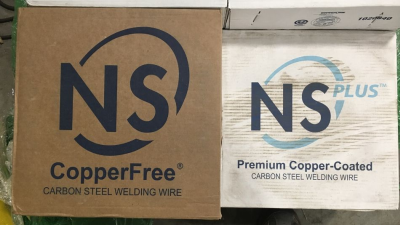
Consistent wire diameter is vital to a proper current passage from the contact tip to the wire. If your wire is undersized, it can cause arcing between the inside diameter of the tip and the wire. This will erode the inside diameter of the top and eventually cause it to fuse to your wire. Oversized wires, on the other hand, will cause excessive feeding force, block your tip, and end up causing downtime and wire slippage.
A quality wire will be manufactured smoothly, without diameter or cast changes when the wire ends join together in butt welds. These locations within your spool or reel are the most often cause of variation in the wire diameter or cast when it comes to ower quality MIG welds.
Over time, this affects the deposition by up to 8%, so make sure your manufacturer has inspected 100% of the wire with a laser micrometer.
If you’re using a stick electrode, cored wire, spot resistance, or submerged arc welding then you may need to switch back and forth to MIG wire for added benefit.
The advantages of wire switches include welding with less to clean up because there’s no slag regardless of how many passes you need to make. They also don’t require as much skill from the operator, so beginners find it useful.
Using a Tandem MIG process of 2 MIG wires will allow for lower heat input than submerged arc and lower the distortion. It is more versatile and can be used on a variety of different materials, regardless of the strength of the metal or the alloys contained.
MIG wire can even let you do all-position welding, which means you’ll have less fixturing to handle and lower costs. It uses lower heat input so you don’t have as much distortion or burn through in your finished welds. It also has a high electrode efficiency rating of 97 to 97 percent!
Solid MIG wire usually also has better placement than cored wire. This affects the ability of your wire to exit the contact tip of your welder in the same location every single time for accurate placement.
This is important when it comes to welding automated materials. When you compare wires in the joint, look for a consistent cast.
Changing MIG wires could be good for your weld project. They can improve your productivity, reduce fumes during welding, save money, and fix quality issues. That being said, it’s important to do it the right way.
Different wire types may run on different polarities. This will impact your entire welding process. Wires that operate using electrode positive (EP) polarity will usually have more of the welding arc heat on the base material.
This provides deeper penetration. Conversely, electrode negative (EN) polarity uses the arc heat for the wire itself. This causes your wire to burn off faster but also provides higher deposition rates.
Always use the right polarity setting for your wire. Consider the mode your wire operates best in, because you may need to change your equipment or your stings. Wire feed speed and voltage are all affected. You also want to consider your space. Larger spools and drums will require a larger weld cell footprint and storage area.
You should also determine whether you need to change your consumables and equipment when you change your wire. Welding wand, drive rolls, liners, and contact tips are all dependent on your wire.
If you need a different polarity or process, you may also need to draw more power. This current can be found in higher-amperage welding guns, which work to eliminate the extra heat and won’t get damaged from overheating.
Consider the size and type of your wire when selecting the drive roll, too. Flux-core and metal-core wires tend to be softer, so they need a knurled drive roll.
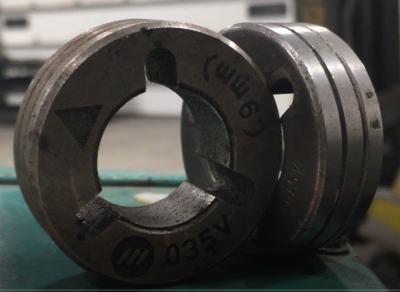
This drive roll can grab the wire ad push it through with teeth, so you get a consistent feed. These knurled rolls should never be used with solid wire because the teeth will shave the wire and clog your liner. For solid wire, use a smooth V-groove drive roll instead.
To increase performance, it might also be necessary to change your contact tips with new wire. The size of your contact tip should match with the wire size so you don’t incur issues with arc stability. Mismatched wire and tips can also result in bur-back and wire stubbing. Switching wires may increase the diameter of your wire, which would then require a larger contact tip size.
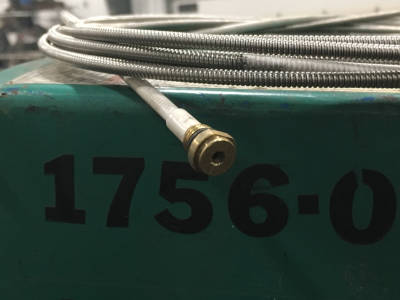
Cable liners also depend on your wire. The liner size should match the wire diameter. If your liner is too big, it will cause your welding wire to move around and slip. This leads to birdnesting and erratic wire feeding, which in turn causes an unstable arc. If the liner isn’t big enough, the wire can’t feed through, which also creates wire feeding issues.
You may also need to change your shielding gas. The wrong gas for the wire can cause defects and poor weld quality that will require you to rework the weld. For example, if you’re moving from MIG welding that uses solid wire to a pulsed MIG process that takes a metal-cored wire, you will need to increase the percentage of argon in your shielding gas mixture to at least 90%.
Frequently Asked Questions
Here are a few of the remaining questions people have asked that end p mostly unanswered. Hopefully, this covers the last of the information you are looking for before beginning your project.
What type of metal is MIG wire?
MIG wire is typically made of mild steel. It gets coated in a copper plating.
Why is MIG welding wire copper coated?
MIG wire is coated in a copper plate to slow down the process of oxidation (or rusting) in the wire and the base metal. This coating also decreases the wear and tear on your contact top and allows for solid electrical conductivity.
This copper coating or plating should never flake off or leave any residue. If it does, it will clog your wire feed cable or your welding gun.
The layer of copper in a coating must be kept at a low enough level to minimize copper fumes and flaking while welding.
Conclusion
Now that you’ve been through our guide, you should know exactly which type of wire to use when.
You’ve learned about the different types and sizes when to use them when to switch between them, and the advantages and disadvantages of each type.
Now, you are ready to grab a welder and get started with your MIG welding project!