How to Make Strong MIG Welds – A Beginners Guide
A lot of people turn to MIG welding when they are learning how to weld. MIG welding is one of the easiest techniques to do. It is also one of the friendliest and most forgiving for new people who have not mastered the perfect technique yet.
MIG welding is where I first learned how to weld. Sure I made a lot of mistakes as a beginner but over time I learned a lot about what makes a strong weld and what does not.
It is also much more affordable than other methods – both in terms of welding machines and the tools and components required – and more portable and versatile.
How do you make strong MIG welds? There are 5 components to making a strong MIG weld. You need a good ground, the right welding gas, the proper settings on your welder, the correct wire, and decent skills to lay a good bead.
Unfortunately, it has also gotten a reputation for being weaker than other methods of welding. Many welders feel that MIG welds are more prone to porosity, more likely to end up contaminated, and more likely to need reworks than other welding techniques. They feel that the welds don’t get as much penetration and don’t hold as strong.
This is actually not true. Despite these common misconceptions, MIG welding is a great option. It’s very flexible, compatible with most material types and thicknesses, can work on aluminum as well as steel, and offers plenty of strength for those who know how to properly handle MIG welding.
This guide will teach you everything you need to know about how to get a strong MIG weld from your project. You will learn what makes strong welds, how to spot good from bad welds, and how MIG welding stacks up against TIG and stick welding in terms of strength.
If your MIG welds need some work, and you’re wondering what others do to achieve perfect and strong MIG welds, then read through our guide. We will offer some great techniques and positions for MIG welding and by the end, you’ll be able to confidently weld and test your project for strength.
How to Make Strong MIG Welds
We rarely think of welds when we are out in nature, but the truth is that every aspect of our daily lives uses welding. It’s the only way to join together multiple pieces of metal to create a single piece. This means that skyscrapers and cars and even boats and planes are full of welds.
These items are economical and efficient to create thanks to the art of welding, but they also must be reliable. A marine craft that isn’t airtight will take on water and sink. If a weld doesn’t hold strong for airplanes, the entire thing will fall from the sky. This means it is important to create strong welds.
MIG welding (which is also known as GMAW, or gas metal arc welding), is the most common type of welding used today. It is also the easiest to master for both industrial and home use.
In MIG welding, an electric arc forms between workpiece metals and a wire electrode (which gets consumed). The heat that results causes these metals to melt and then fuse together permanently.
What Makes a Good Weld
The best way to make good MIG welds is by using a good ground, the right settings on your welder, a short stick out, and proper technique.
Ground Clamp
Getting a better ground clamp can really improve your weld.
The wrong ground clamp will make a terrible noise when you start your welder up and can destroy your machine and your weld.
Side Note: I prefer a copper ground clamps like this one because they conduct electricity the best and are built to last.
Avoid bad grounds. Clamps used to be made entirely from copper, but more recently they’ve moved towards plated steel with copper jaws. This isn’t as good at the job.
Stick Out Length
You also need to make sure your stick out length is short enough. This refers to the distance from the arc to the contact tip on your MIG welder, not the distance from the arc to the nozzle.
If you stick out is too long, it will make your weld pile up because your arc will be too soft. While this will work okay and might be good for super thin sheet metal, it’s not great for welds that don’t need a high amperage spray transfer.
You can attain a strong and stable arc on thicker metal and short circuit MIG work by making sure your stick out os less than ½ an inch. A recessed tip will result in too much stick out. A tip that pokes out a little offers a shorter stick out, which results in better penetration and a smoother weld.
Weld Up Hill
You should also learn how to weld uphill. If your metal is thicker than ¼ inch, you will need to learn to weld uphill to avoid a lack of fusion. Otherwise, you won’t get a deep enough penetration.
Likewise, welding downhill may look more aesthetically pleasing but it is not as strong as a weld.
Good Weld vs. Bad Weld
Some warning signs of a bad weld include a lack of uniformity along the weld, welds that are too thin, cracking down the middle of the bead, and discoloration of the base metal.
Metal sheets are usually thinner with MIG welding, so you will occasionally notice cracks running through the center of your bead. This indicates poor fusion on a bad weld. The parent metal, usually steel or aluminum, may also discolor.
Most of the time in MIG welding, bad welds are a result of
- An improper bead profile
- Lack of fusion
- Faulty wire delivery
- Excessive porosity
To prevent porosity in your welds, use a deoxidizer in your wire. You also want to grind your surface clean from oil, rust, and paint.
Improper bead profiles are usually caused by cold welds. If you don’t have enough heat input, you won’t get proper penetration.
Check your amperage against the thickness of your base metal and adjust as necessary. You can also change the angle because in MIG welding 5 to 10-degree push angles will help with penetration.
If your weld isn’t fusing properly, it might be because of your arc. Short arc transfer methods require sufficient energy to work, or you will fuse the weld pool to the base plate without joining the metals together.
Make sure your amperage and voltage are set properly and change your technique if the problem continues.
How to Make a Strong Weld – What Welding Patterns Make a Strong Weld
There are several things you can do to make a strong weld.
Do your Research
The first is to do research. You want to learn the best practices for your specific base metal and wire. This will let you know the recommended parameters so you can configure your welder properly.
As previously mentioned, keep your stick out short so you don’t end up with a cold weld that drops amperage and reduces penetration.
Make Sure Your Connections are Tight
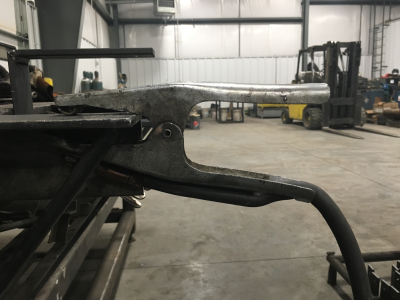
You also need to check your connections. You need all of them to be tight and make sure that no spatter has built up anywhere on your consumables.
Your ground cable should be as close to your workspace as you can get it. If possible, hook it to the weldment itself. The closer your ground cable is to your arc, the better your weld will be.
If your ground isn’t tight or close, you will end up with overheating in your gun. This lowers the quality of your weld and decreases the lifespan of your welding contact tip.
Check Your Drive Roll Tension
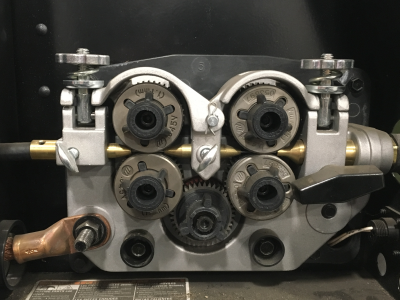
You also need to make sure you’ve got the right drive roll and tension settings. Without the right settings, your wire won’t feed properly. You need to keep the size and type of your wire in mind then match it to the right drive roll.
A flux-cored wire is softer, so it needs a knurled drive roll. The teeth can grab your wire and feed it through properly. With solid wire, you need to use a V-groove or U-groove roll instead. The teeth will shave solid wire and lead to hams and breakage that will clog your liner and resist the feed.
You can set the tension properly by releasing the rolls, then increasing the tension gradually while feeding the wire into your gloved hand until the tension is a half-turn past wire slippage.
You also want to make sure your gun stays as straight as possible, so you don’t kink your cable and cause bad wire feeding.
Check Your Weld Tips
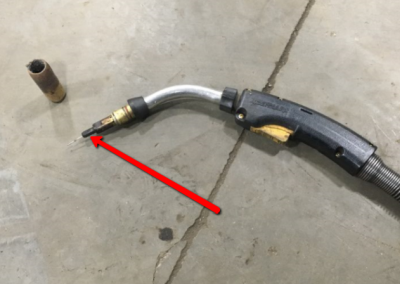
You should also use the right contact tip recess. These contact tips have a massive impact on the strength of your MIG weld and your welder’s performance. This consumable is what transfers your welding current to your wire and creates your arc.
The position of your contact tip within the nozzle (also known as the contact tip recess) is also important. The right position will reduce splatter, eliminate porosity, and offer better penetration without burning through or warping thin base materials.
Check your welding machine and wire specifications for the right setting and position. A general rule of thumb for guidance is that the recess will increase as current increases.
Check Your Shielding Gas
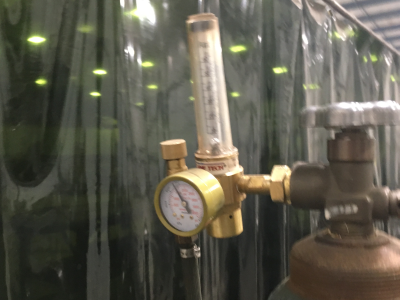
You also need to match the shielding gas to your wire choice.
Different wires require different gas mixtures. CO2 is cheaper than argon and great for penetrating steel welds, but it’s also cooler so it may not be ideal for all welds. A 75 percent argon to 25 percent CO2 gas mixture will offer great penetration and clean welds while generating less spatter.
For solid carbon steel wire, you should use 75 percent CO2 to 25 percent argon. This type should be used inside with no wind.
Aluminum wire needs 100% argon gas but is ideal for strong welds. Stainless steel wire works well with helium, argon, and CO2.
Keep a Good Welding Position
You also want to keep your wire directed at the leading edge of your weld pool. To control your weld bead properly, directing the wire at the leading edge of the pool helps.
If you’re welding out of position (vertically, horizontally, or overhead) then your weld pool should remain small so you can maintain control.
Beads that are too skinny or tall are a result of welding too fast when you travel or not having enough heat in the weld joint. If your bead is too flat or wide, then your settings are too hot or you’re traveling too slowly.
Pushing will preheat the metal, so it ‘s better than dragging (or pulling) when working with thinner metals. Pulling solid wire will flatten your weld and drop extra heat into your metal.
Always store your filler metals with care. You want to put them somewhere dry and clean, so moisture won’t damage the wire.
You also want to use gloves any time you touch the wires so moisture and dirt won’t get on the surface of your wire.
How to Test How Strong Your Weld Is
Sometimes, a bad looking weld is just a matter of aesthetics. You may be a strong enough welder to create a solid joint but lack the precision and finesse necessary to create a strong joint that also looks beautiful.
You can tell whether your weld is strong or not by employing a variety of tests.
You can do a variety of tests to find voids, lack of fusion, and other weaknesses in your welded project that would require a rework of the joint.
Welds usually get tested for their intended function. The tests use the same conditions (or sometimes more severe ones) that the welded joint will encounter in the field. Some of these testing techniques include…
- a gas weld test
- backbend tests
- physical weld tests
- ink break tests
- fluorescent penetrant tests
- hardness tests
- magnaflux tests
- guided bend tests, acid etch tests
- hydrostatic tests
- tensile strength tests
- electromagnetic tests
- acoustic emission tests
- free bend tests
- magnetic particle tests
- x-ray tests
- ferrite tests
- and gamma-ray tests
You may have no idea what any of these tests mean or do and you might be thinking how can I do any of these tests when I’m just a hobbyist or beginner that doesn’t have access to equipment to perform these tests.
However, there is one test you can do and that is to simply cut you weld. To this set up a basic weld you normally do such as a T-joint weld.
Quick Tip: You’ll want a longer weld that will allow you to cut the weld.
Once you make the long bead take a 6″ angle grinder and cut it in half. Once it’s cut look at the weld from the end. The picture below shows what a good weld looks like.
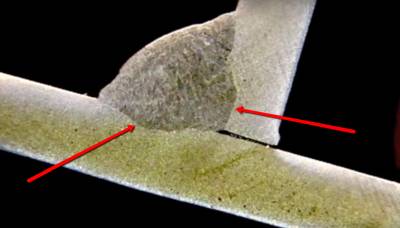
As you can see the weld penetrated deep into the base metal and will hold. If you do not see this then you may need to make adjustments to your welder to get a better bead.
Frequently Asked Questions
When it comes to MIG weld strengths, the most commonly asked question is how it compares to the weld strength of other welding methods.
Here are the answers to how MIG welding stacks up against TIG and stick welding, the 2 most popular methods after MIG.
Is MIG welding as strong as stick welding?
There are a lot of little variants that go into welding, especially with the wire. Flux core with fas or no gas, for example, is one variation.
For the sake of the question, we will look at the bare wire when determining the strength of MIG welding versus stick welding.
A lot of people use E70S-6 bare wire and others use 7018 stick rods. The 70 in each of these product names means that they are the same strength.
Both the bare wire for MIG and the rod for stick have a 70, which represents the 70,000 psi tensile strength. These will be at least as strong as most of the steel you would be welding, occasionally stronger.
Penetration is another variant with regards to weld strength. If you’re welding downhill on 3/16 or thicker, then a 6011 stick rod will penetrate far deeper than bare wire.
If you’re doing vertical uphill welding, then MIG will penetrate jut as well as the stick as long as it’s hot enough when it sets and you keep the wire stick out short.
With stick welding, there is a safety net that gets built-in. You have to set your machine hot enough to keep your rod hot. With MIG welding of wire, there’s no limit so it’s possible to keep your machine set colder and achieve a more aesthetically pleasing weld that won’t get through the mill scale on hot rolled steel.
In the end, it is possible to achieve a MIG weld that is as strong and deeply penetrated as stick welding. It will just require certain techniques and positions to be used.
For this reason, you will need to have more of a mastery over technique than if you used stick method welding in order to achieve the strength.
Is MIG welding as strong as TIG welding?
MIG welding is often more popular than TIG welding because it’s faster, more affordable, and easier to master. It’s extremely common in automotive welding and at home.
TIG welding, on the other hand, is very popular in aerospace manufacturing. It’s more expensive and time-consuming, but it produces some very high-quality welds.
MIG welding can weld thicker materials together than TIG welds, and at a much faster pace. If you’re using thinner metal, TIG also works. MIG welding tends to be much faster, while TIG welding is more concerned with aesthetic detail. MIG welding is easier for beginners, and TIG welding requires both hands and much more experience with balancing and timing.
MIG welding is faster, cheaper, and more accurate than TIG welding. It also leaves a much cleaner weld with less maintenance required. Unfortunately, it’s also less reliable, less safe, and not as strong as TIG welding. It can cause rush deposits and produce toxic fumes.
TIG welding is more precise, doesn’t require filler material, lower maintenance, and offers greater control than MIG welding. Unfortunately, it’s also more expensive, more difficult, takes longer, and requires a thoroughly cleaned surface.
Which one is stronger, though? In the end, TIG welding will usually produce much cleaner and more precise finished welds than MIG welding can do. A lot of people assume this means that TIG welds are also the strongest ones out there.
This isn’t always the case, because there are a lot of different types of welding jobs, and each one may require a different method of welding. TIG is usually stronger, but many jobs specifically require MIG welds instead, as they are more versatile and often just as strong.
Conclusion
As you can see, there are a lot of factors that go into making a strong MIG weld. With the right technique and training, it is a solid choice and you can make very reliable welds from this method.
Employing the MIG welding technique in a variety of ways will result in deep penetration and strong welds. We have covered a lot of great tips.
What are others in the welding community doing to make stronger MIG welds? Begin with our methods and then continue researching to get even better results!