How Do You Fix Welding Porosity – A Complete Guide
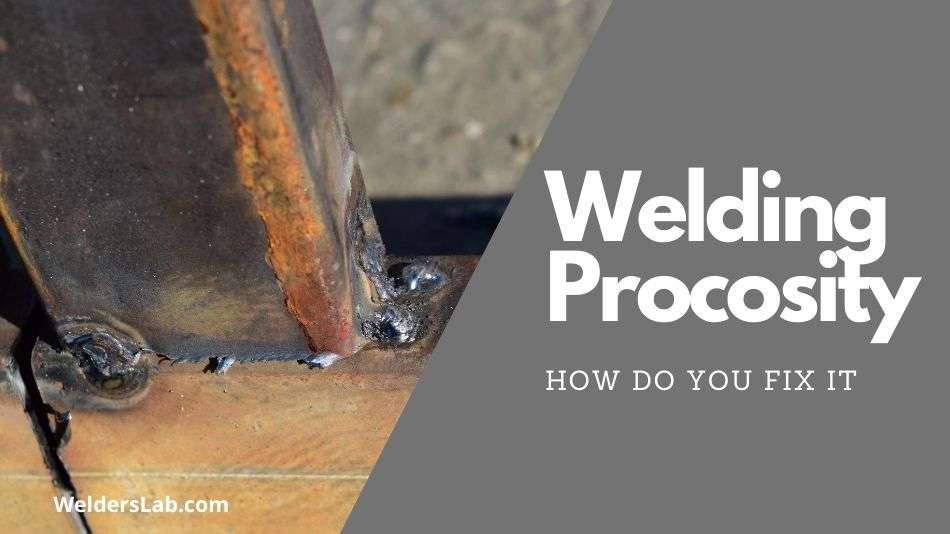
No welder is ever perfect. One thing I’ve learned over the years is that building your skills takes time and effort. We all still make mistakes and even I still get bad welds sometimes. One of the worst problems to have is porosity in your weld.
No matter how skilled you are, some metals are harder to weld than others. Of course, there are certain things you can do to try to prevent issues like porosity in your weld but you should know how to fix porosity when it happens.
As a welder, we must be able to educate ourselves on what leads to porosity and what we can do to both prevent and correct porosity. After all, porosity is a sign of a weld that might not take, which means your job isn’t done as well as it should be.
How do you fix welding porosity? Welding porosity is caused when there is either a shortage of shielding gas due to an empty tank or because the wind blowing the gas away from the weld. If you are getting porosity with flux core or a stick welder you may have an old welding rod and wire or they will likely have been damaged.
In this guide, we will cover everything you need to know about fixing porosity. We will talk about the two main types of porosity, how you can fix porosity, and why it needs to be fixed before you move on.
Stick with me to learn about fixing porosity in a weld.
How Do You Fix Porosity? The Ultimate Guide
Before you can fix the porosity in your weld, you need to understand just what porosity is and what causes porosity. We have a lot of ground to cover so let’s get started.
What is Porosity in a Weld? – Identifying The Cause and What to Look For
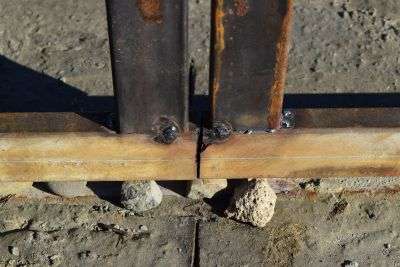
Ultimately, weld porosity is due to trapped gas. It is a contamination in your metal. This can happen from welding with the wrong shielding gas or trying to weld two metals together that aren’t compatible. It can also happen from not having a clean enough surface.
These issues cause tiny little holes (or pores) in the weld that cause it not to hold up or hold together properly.
A few other common causes to look for is your gas levels, a hole in your gas line, rusty or contaminated wires and surfaces, spatter in your MIG gun, oils, or contamination on your surface.
There are two primary types of weld porosity.
- Surface porosity
- Inner porosity
You can typically see the pores simply by looking at your weld. If your weld looks porous and clearly isn’t a good weld, you should address the issue. The two types of porosity are pretty self-explanatory. One if on the surface of the weld while inner porosity is found inside, or in the center, of the weld.
When it comes to porosity, the holes are not always tiny like pores but can rather be large or even elongated holes in the weld. Inner porosity is far more challenging to identify because those holes or gaps are underneath the surface. You may not be able to identify them without some sort of testing or an x-ray of the weld.
There are weld quality tests that can be completed. These tests can be both physical and visual. This is the best way to know you have a quality weld and determine if you potentially have any inner porosity. Surface porosity is far more common and thankfully, far easier to diagnose.
If you’re asking yourself why is there porosity in my weld? Consider the factors we discussed above and whether or not those are your leading cause. None of us like to see porosity in our welds, which is why we take such great care to prep our surfaces.
Unfortunately, prepping your surface isn’t always enough to ensure that you won’t have a porous weld since there are so many other causes that can affect the weld as well.
How to Fix Weld Porosity
In order to fix weld porosity, you must first determine why your weld has porosity.
Follow thesetrouble shooting questions.
- Is my surface sufficiently cleaned?
- Is my hose clogged with spatter?
- Is my gas high enough?
- Are my metals compatible for welding?
- Is my wire rusty or contaminated?
There could be other leading issues causing your porosity but these are the most common things. If you can identify what caused your weld porosity, then you can fix the issue and move on. The majority of porosity can be avoided by cleaning your surface appropriately before you start.
The most common causes are unclean surfaces and improper gas levels.
Once you’ve done the weld, if you have weld porosity, you really should grind off the weld and start over. This time, try to clean your surface and get your levels right. Sometimes, it just takes practice and learning the proper technique and levels to get you there.
As a beginner, you may find yourself grinding off welds with porosity quite a bit. Remember it takes practice to build your skills and get the technique down. Try to learn from your mistakes as you go and you will get more familiar and more meticulous with what works and what doesn’t.
Case in point here, ALWAYS clean your welding surface properly before starting.
You should never weld over the surface of weld porosity in an effort to correct it. This does not correct the issue but rather just covers it up. If you’re working on an artistic piece that is mostly for looks and won’t be load-bearing or required for structure, you might be able to get away with it.
However, best practice is to simply get out the grinder, grind away that bad weld, and start fresh again. This is always your best bet for fixing weld porosity.
You can look things up to know what gas flows you should use
The Dangers of Porosity
You might look at a weld with obvious porosity and choose to ignore it but a good welder will never ignore telltale signs that their weld isn’t good.
Unfortunately, a weld with porosity is not a solid weld. Surface porosity is an obvious indication of a weld that isn’t solid and you should work to correct that issue. Why is it dangerous? Ultimately, porosity in the weld is an indication that it is lacking the structural integrity that a weld is relied upon for.
Inner porosity is much harder to pinpoint since it is hidden below the surface. If you’re working with any sort of structural piece or something that will be load-bearing, you should be proactive and complete some sort of weld quality testing to ensure your weld is safe and secure and there are no hidden porosity issues.
Ultimately, porosity is unreliable. It’s a bad weld and you should never just leave it if you are aware of it. It will not hold up over time and can be quite dangerous, particularly if you can identify porosity that needs to be corrected.
Can You Weld Over Porosity?
We’ve already somewhat touched on this subject but we want to dive a little deeper. The best bet if you identify porosity in your weld, regardless of whether its surface or inner porosity, is to grind off the weld, clean your surface, and start over again.
Every welder has had to grind off a weld and do it over again. You’re not alone and don’t ever think that you can just ignore a bad weld and move on. That’s a blatant sign of shoddy workmanship and it’s simply unacceptable. If you notice porosity, just do the right thing and start over.
There are certain exceptions. For instance, if you’re just welding an artistic piece or something that is just for fun or for show you could ignore the porosity. The same rule applies though that this weld will weaken over time. Welding over it won’t fix the issue.
If you are welding anything structural, load-bearing, anything that may receive any semblance of pressure should be fixed. This means grinding away the weld with porosity, cleaning up the surface, and doing the weld again.
According to the American Welding Society, the rule is that if your visible porosity exceeds 3/8 of an inch, or 9.5 mm, in any linear inch of weld, it is unacceptable and should be corrected. So, in terms of how much porosity is acceptable in a weld, you can follow these guidelines.
However, I recommend that if you notice surface porosity, you simply just be proactive and start over to ensure the integrity of your weld.
Conclusion
Welding porosity is a nuisance at best. It’s not always something you can control right away and many times you won’t notice it until you’re either well into your weld or even finished with your weld.
It’s never fun to have to correct the issue but it’s simply part of the job.
Take heed of the tips and tricks we’ve shared here, as well as the general information that can help you deal with weld porosity and you will be well on your way to better welds in no time.