What Happens if the Feed Roller Tension Is to Tight, Loose, or the Wrong Size – Complete Guide
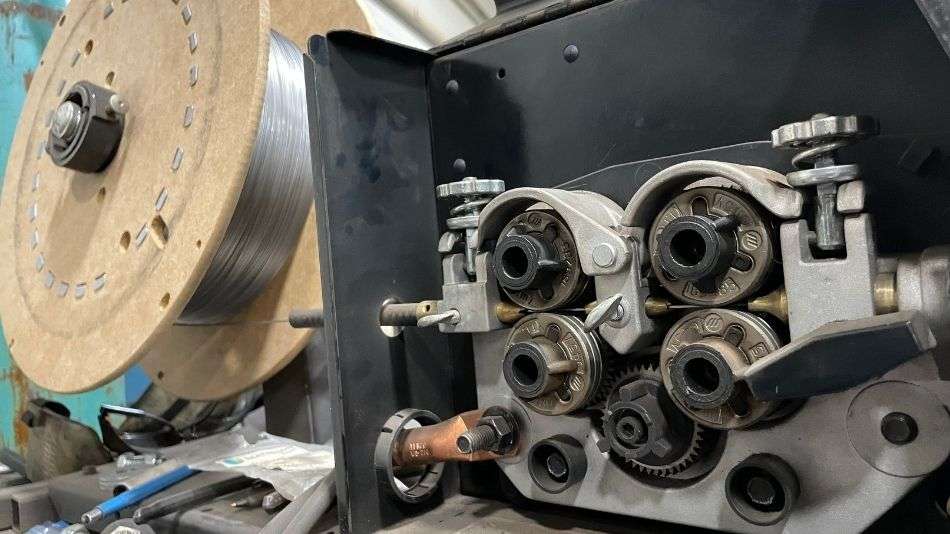
If you have a MIG welder you know that it has a set of feed rollers on it the pull the wire from the wheel to the lead, to the weld gun where it ultimately welds a bead. However, what you may not know is how important these feed rollers are.
I learned this the hard way one of the very first times I was putting a new roll of wire on my welder. I replaced the wire and noticed that when I was welding the wire wouldn’t feed through the welder correctly. It would start and stop causing breaks in my welds.
What I had come to find out was that I was smashing the wire. This caused the wire to widen and small parts of it to break off. As a result, it made it hard to push through my liner.
This all happened because I tightened down my feed rollers too tight. In the rest of this article, I’m going to cover exactly what happens if you tighten your feed rollers too tight, or not tight enough plus more so you can avoid these mistakes.
What Happens if the Feeder Roller Tension Is to Tight
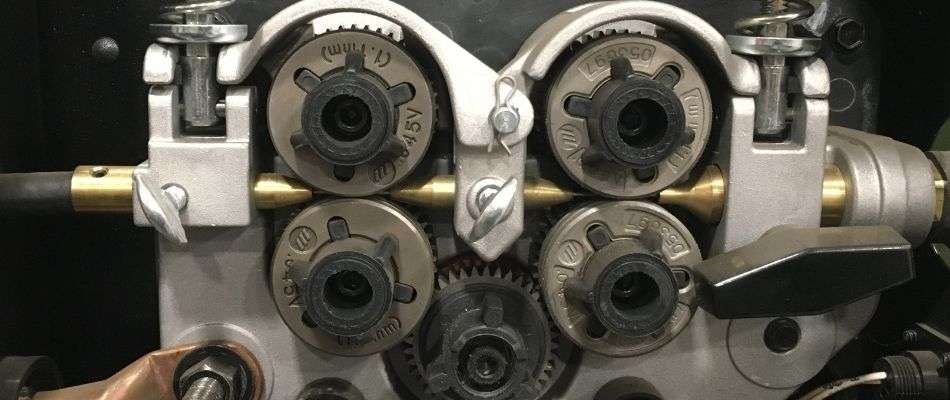
If the tension on a MIG welder is set too tight it will cause the wire to flatten, making it harder to pass through the liner. This will cause small shavings of the wire to break off and plug up the liner. This could also cause the wire to brake and bunch up.
As I mentioned at the beginning of this article this happened to me once where it actually flattened the wire. This can cause a few big issues with your welder if this does happen.
Deformed Wire
The first problem is that can deform the wire. Welding wire is meant to be the size that it is. Everything from the tip to the liner depend on it staying the size that it is.
If it gets flattened because the tension is set too tight it will make it hard to pass through the liner and especially hard to pass through the welding tip. In some cases, it won’t even pass through the tip based on the tip size.
Shavings
The second problem this will cause since the wire is being deformed is that it will cause tiny parts of the wire to break off as the wire passes through the rollers. These shavings can play havoc on your liner.
Over time they will bunch up and begin to plug up the liner. If you don’t catch this soon enough you have to replace the liner altogether.
What Happens if the Feeder Roller Tension Is to Loose
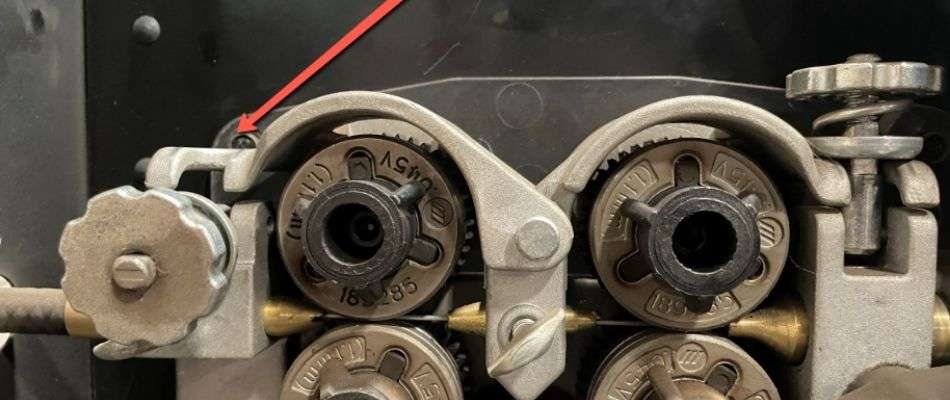
If the tension is not tight enough on your MIG welder then the wire will slip on the rollers and not feed through the liner. This could cause the wire to start and stop creating infrequent welds.
I’ve had this problem happen to me a few times over the years and it can be a bit annoying. Here are a few reasons this might be happening to you if you’re experiencing this issue.
Loose Tension
The first problem is that you probably don’t have the tension on the feed rollers tight enough. In order for the feed rollers to pull the metal wire through the welder, it needs to be tight enough to grab the wire.
To tighten this to the correct setting just follow me step below on how to set the tension correctly on your MIG welder.
Tension Not Hooked Up
The other reason this could be happening is that the tension isn’t hooked up. This usually happens to me when I’m putting a new spool of wire on the welder. I run the wire on and forget to set the tension altogether.
This is a quick fix since you just have to pop the tensioner back on and you’re good to go.
What Happens if I Use the Wrong Size Rollers
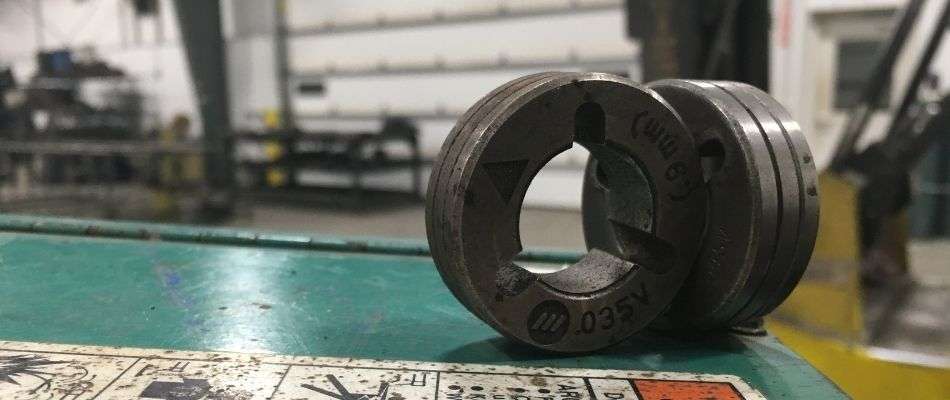
If you are using the wrong rollers on your MIG welder they may be either too tight or loose on the welding wire. A smaller roller size may cause the wire to become deformed and break off small shaving and to bigger roller size will cause the wire to slip and not pull through the lead.
If this is the case here are a few things you can do to fix this.
First, check the size of your wire. Make sure it’s the correct wire size that you intended to use.
Second, check the roller size you are using. The wire size should be stamped on the side of the roller you are using.
Third, change the roller. If the wire size and the roller size are not the same numbers then you need to pull the rollers off and put the correct size on. A lot of times a set of rollers will have two different sizes on them. For example, on one side you might have .035, and on the other .045.
If this is the case all you may have to do is take the rollers off and just flip them around.
How to Set the Tension on the Feeder Rollers
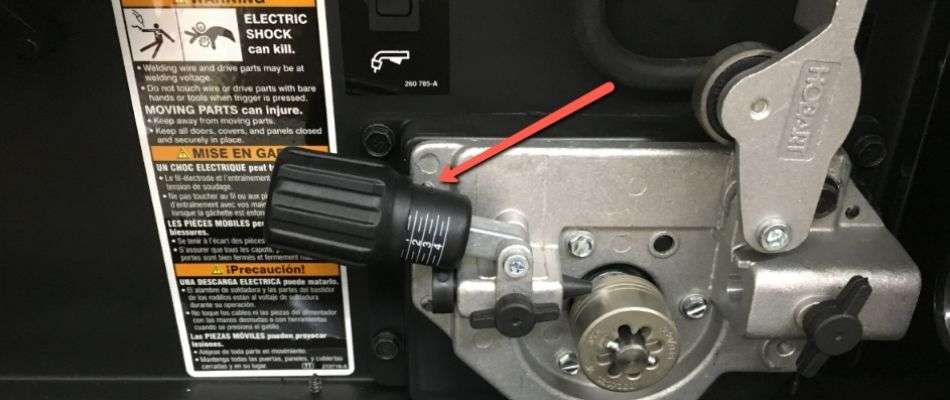
Now that you understand what happens when the wire feed rollers are too tight, loose, or even the wrong ones you need to know how to set the welder to the proper tension so you don’t run into this issue again.
1. Loosen the Tension
To set the feed roller tension on a MIG welder start by loosening the tension on the rollers. If the wire is slipping then it is too loose. Tighten the wire till it starts feeding though.
2. Remove the Ground Clamp
Then remove the ground clamp from your table. In order to set the tension, you’ll need to use your welding table and you don’t want the wire to arc while this is happening.
3. Squeeze the Tigger
Finally, keeping the weld tip face straight down at the table and squeeze the trigger. As the wire comes out it should start to curl around like a spring. If the wire doesn’t do this then tight the tension till you start to see the wire curling up.
As a side note, some welders have built-in tension settings for all the different wire types, such as stainless steel, and aluminum. If this is the case then you can set your tension to those settings but for good measure, you can do the test I mentioned above to double-check yourself.