What Are the 4 Types of Welding Processes – A Definitive Guide
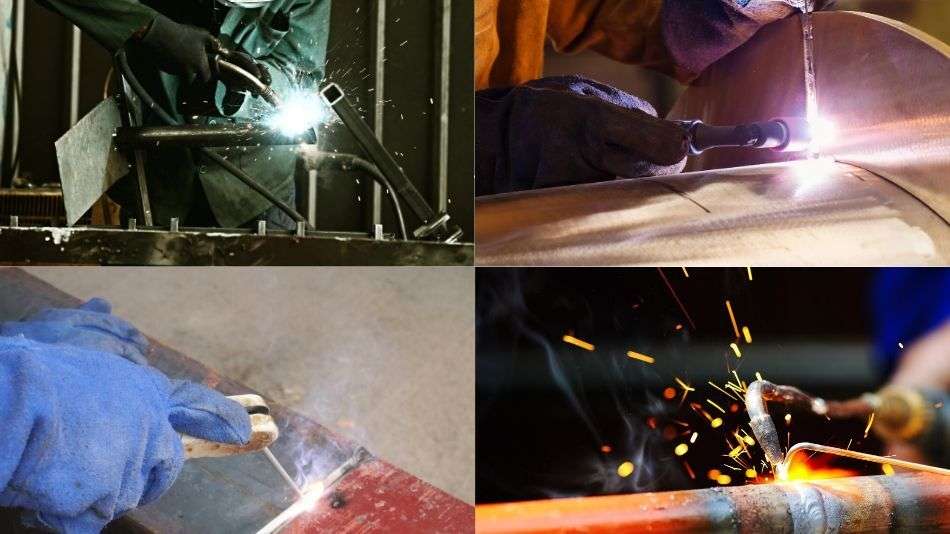
There are various types of welding processes available to use. It can often be difficult to determine which of the different types of welding processes are worth learning and using from project to project. Each of them come with their own advantages and disadvantages.
What are the 4 types of welding processes used by industry professionals? There are MIG, TIG, stick, and flux core welding. Each of these comes with its own set of advantages and disadvantages, and different welding projects call for different techniques to get the job done to the best possible standards.
If you’re wondering which type of welding to use for your project, then read this article. By the end, you will know a lot about each type of welding.
You’ll be able to determine which process is best for your project base on the materials you’re using, the penetration you need, and whether or not it needs to look as solid as it functions.
Let’s take a look at the different types f welding now.
MIG Welding (GMAW)
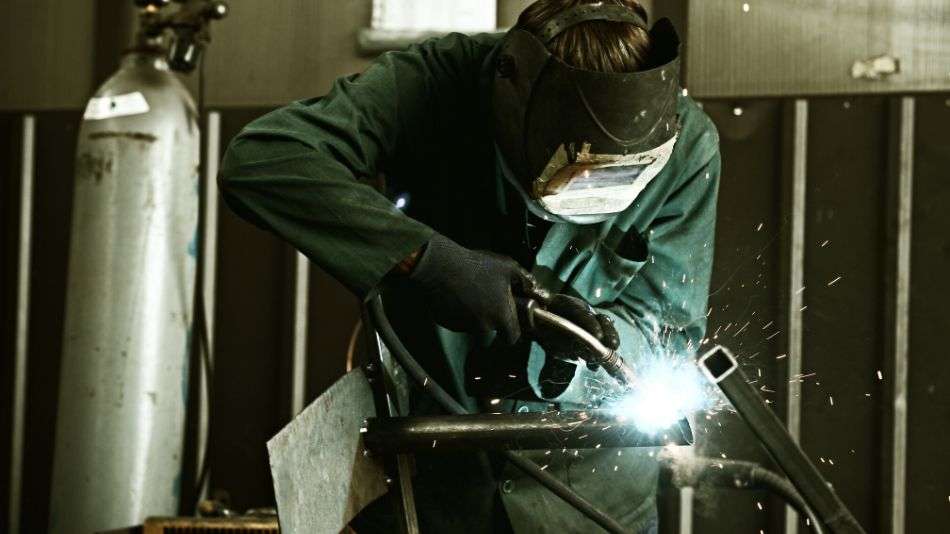
K\MIG welding is the first type of welding process. It’s the most popular and commonly used type of welding because of its versatility and ease of use. It is also known as Gas Metal Arc Welding (GMAW).
What is MIG welding?
MIG welding uses a metal inert gas (hence, MIG) as a shield along the wire electrode during the welding process. This will heat the 2 metals that need to be joined and fused together.
This method of welding requires a constant voltage and uses a direct current (DC) source for its power. There are 4 methods of transferring the metal: globular, short circuit, spray, and pulsed spray.
MIG welding is one of the oldest welding practices around, having originated in the 1940s. Because it is so versatile and easy to learn, it has become the favored process for nearly all indoor and industrial welding available. Pretty much anyone can learn how to MIG weld.
How does it work?
This process works by using consumable wire. The wire gets fed from a spool through h the gun and ends up inside the joint in the metal that you’re trying to weld together.
The process uses the welding gun that is fueled by an inert gas. This produces high enough heat in your arc to melt the wire you’re feeding through it into a bead on your joint.
There are a couple of different wires you can use. The common wire types for MIG welding steel are ER70S-3, which is used for pretty much anything, and ER70S-6, which is great for aluminum or for projects that need more deoxidizers, like dirty and rusty base materials.
Usually, a good wire diameter size is .030 inches. It’s great for all-purpose welding on a wide variety of metal types and thicknesses.
On thinner material, use .023 inches instead, because this will reduce the heat input and prevent you from burning through or distorting your base. For thick material, you will need more heat and a .035-inch wire.
Related Article: What kind of wire should you use for a MIG welding? Read my complete guide here.
Next, you need to decide what your shielding ga will be. You can choose from 100% carbon dioxide or a blend of 75% argon to 25% carbon dioxide.
The blended gas works best for all-purpose projects. This blend will produce less spatter, make for prettier bead aesthetic, and won’t burn through thinner metals as easily.
Carbon dioxide by itself will provide much deeper penetration for stronger welds that need to bear more stress, but it will also increase you’re spattered significantly, so you will need to spend a lot of time cleaning afterward.
It will also produce rougher beads than the blended gas, so your weld will be stronger but won’t look as nice.
Related Article: Not sure what gas mixture to use with your welding? Check out my complete guide here.
After determining these things, you are ready to set your machine. Determining your voltage and amperage will be important for your machine to work properly.
Most MIG welding machines these days will let you input your wire diameter and the thickness of your metal and automatically adjust the machine to the proper voltage and amperage settings and wire feed speed. This allows you to relax and make minor adjustments as needed.
After this, you need to pick the right welding position. The position you use will depend on where the metal you’re welding is located.
The flat positions are nice and easy. You can simply hold your gun at a 90-degree angle to your workpiece and put the filler metal directly into the joint.
T-joints, are the most common weld joint around, which is also called a fillet weld. This simply changes your gun to a 45-degree angle instead and uses multiple passes.
Horizontal welds are used when your workpiece is horizontal in front of you. You need to adjust your gun angle by no more than 15 degrees to avoid your filler metal rolling over the bottom of your weld joint.
Vertical MIG welding is pretty difficult because you have to fight against gravity while welding. Reducing your voltage and amperage a little bit can help. Welding thin metals in this position should be done from the top down to avoid melting through your metal. Thick metals will require you to start at the bottom ad move upwards so you can control the size of your weld puddle.
The overhead position is the hardest welding position to work from because both gravity and your gun speed are working against you. You will need to lower your voltage and amperage and decrease the diameter of your consumable wire to keep your weld puddle small enough to control. Always drag (or push) your gun quickly, so the weld metal doesn’t have time to fall out of the joint.
Advantages of MIG Welding
There are a lot of advantages to MIG welding, which is why it is one of the most popular types of welding techniques and is used in such a widespread way. It’s the best all-purpose welding you can do.
MIG welding is pretty easy to learn. Of all the techniques, only 2 of them are relatively difficult and require more precise technique and skill. Compared to all the other forms of welding, this is the easiest to learn and most people will pick it up very quickly.
MIG welding is also extremely flexible. The versatility makes it really popular. MIG welding can be used for pretty much any metal thickness and type. You can even weld mild and stainless steel, nickel, and aluminum with MIG welding by adjusting a few settings on your machine!
MIG welding can also produce some very strong, high-quality welds. These welds are usually reserved for people who have impeccable technique, but with MIG welding, there is a lot of forgiveness for sloppier technique, so even beginners can produce welds that withstand stress tests.
This welding doesn’t rely on flux, so you don’t have to worry about trapping any slag in your metal weld or contaminating it enough to prevent strong finished products.
This is also the safest welding process to use. The gas shield will protect the arc from pretty much anything from contamination to the elements and it produces virtually no spatter for you to clean later.
Disadvantages of MIG Welding
MIG welding has a couple of disadvantages, too.
It’s got a very high heat input. This means it’s less ideal for using vertical and overhead welding techniques because it could very easily burn through or melt your base metal.
It also has a pretty complex setup. There are a ton of different pieces involved with MIG welding. You have a gun, a gas supply, a constant power supply, a system for wire feeding, and cooling water to consider.
What situations would you use MIG welding for?
MIG welding is great for use on thicker metals. It also works when you need to complete your work quickly. Beginners will also find MIG welding easier to use.
This makes MIG welding great for heavy-duty welding, too. It’s much easier to handle large pieces of metal.
TIG Welding (GTAW)
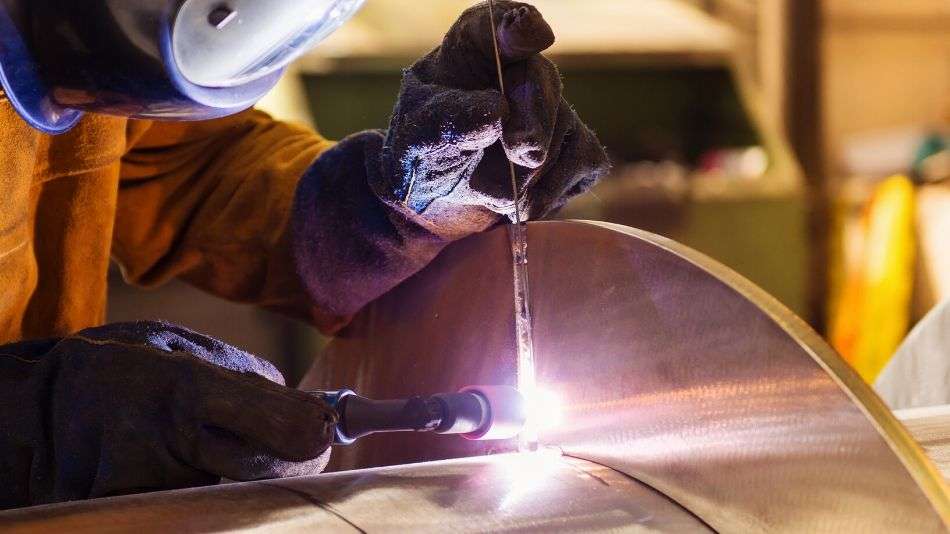
TIG welding is a much more advanced process. It is less forgiving f sloppy technique, but it is used regularly because of its ability to penetrate deeply and handle difficult metals with ease.
This process is also known as Gas Tungsten Arc Welding (GTAW). It is commonly used to handle thick metals and non-ferrous metal like aluminum.
It’s another process that uses an arc, but this one relies upon a tungsten electrode to produce the weld. The process takes the most amount of time because of its complexity.
What is TIG welding?
TIG welding was invented in the 40s by the Northrop Aircraft Corporation. It was created to help with welding aluminum and magnesium, so you can join alloys in aircraft manufacturing.
How does it work?
TIG welding works by using an electric torch with a tungsten electrode. This delivers current to the welding arc. The consumable filler rod gets fed into the weld puddle with one hand while the other holds the torch.
An inert gas cools and protects the work. The heat is controlled using either a pedal or a fingertip.
First, you need to clean and prepare your metal. It’s important in TIG welding that your metal be perfectly clean and free of any oil, rust, oxides, paint, or other issues.
Even metal shavings need to be removed.
Next, pick the TIG electrode for the job. There are 6 different types. Pure tungsten electrodes are affordable and provide a stable arc.
Thoriated electrodes are the most common types. These mix thorium into the tungsten for a stronger electrode tip. These tips will last longer.
Ceriated electrodes are used in DC welds because of the low amperage. Lanthanated electrodes are the most versatile.
Zirconated electrodes are used in AC projects that need an electrode that resists contamination. Rare-earth electrodes offer a stable arc and last longer.
You also need shielding gas. Pure argon is pretty common because you can use it on any metal type. It’s good for narrow arcs.
Argon and helium gas mixture will increase amperage for hot welds. It works well on everything but mild steel.
Argon and hydrogen will increase the heat when welding for deeper penetration.
Advantages of TIG Welding
TIG welding has a lot of fans for a variety of reasons.
It gives a very precise and controlled weld. This is the process that gives you the most control over your weld project.
It also produces the smoothest finish. A lot of people prefer TIG welding for art projects because of how aesthetically pleasing the finished product is. You can also use TIG welding for a wide variety of metals.
TIG welding works on everything, including non-ferrous metals like aluminum, magnesium, and copper.
Disadvantages of TIG Welding
Unfortunately, it hasn’t overtaken MIG welding as the most popular method because it also has some major disadvantages.
This method of welding is the most difficult welding process to learn. It is extremely complex and requires a ton of control.
It offers absolutely no forgiveness for poor technique, so you must have high levels of accuracy and skill to make sure the arc is kept at the right distance from the metal workpiece, the penetration runs deeply enough, and the weld stays strong.
TIG is a slow process. Because of the required precision and fluctuating heat control that you control yourself, and because this method requires the use of both hands, it is also an extremely slow process.
Can’t be automated. Unlike other methods of welding, TIG welding can’t be automated for use in manufacturing and robotics. It requires a person to take a fair amount of time to handle the work.
It takes more time to do. While this produces the best detail work, it also takes significantly longer to accomplish simple tasks so it’s less popular for welds that don’ need to look perfect.
TIG welding is also less safe than other methods. It uses electrodes that are not consumable and also not flux coated. This means they won’t screen your arc light well, making it extra dangerous to use. This is only compounded by using arcs and gases that maintain very high levels of heat.
What situations would you use TIG welding for?
TIG welding is the preferred welding method when you are working with very thin material. Because you can precisely control the heat, you can join thin pieces of metal together without melting, burning, or distorting your base metal.
TIG welding is the best option when you’re joining wires together for steel baskets. It’s also great for jobs that have smaller budgets. It joins the pieces of metal together directly rather than using filler metals, which makes it cheaper and also makes it less likely to fail.
Stick Welding (SMAW)
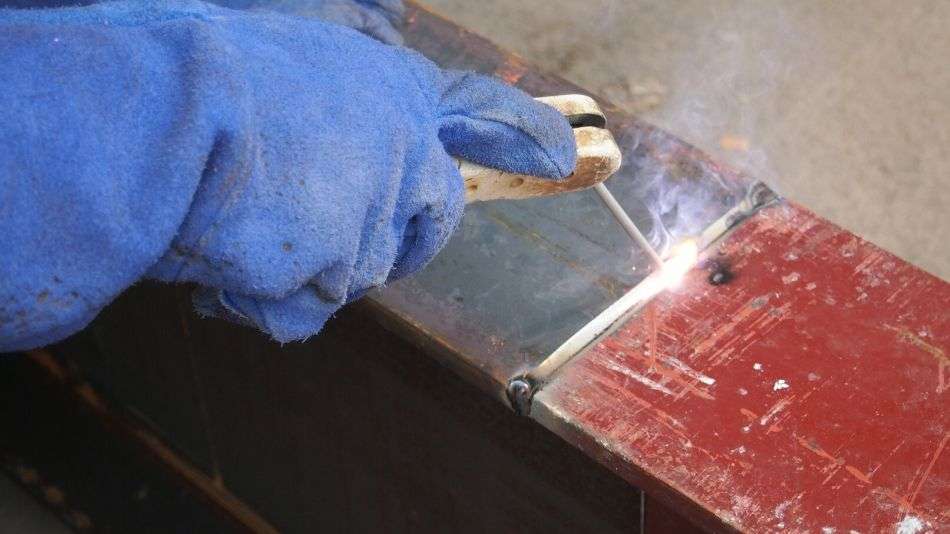
Stick welding is also called Shielded Metal Arc Welding (or SMAW). This welding requires a manual welding process with a stick.
This stick uses an electric current to create an arc between the metals that need to be fused together.
It’s used regularly in steel structures and industrial fabrication because it can penetrate deeply.
What is Stick welding?
Stick welding is the most regularly used of all the arc welding methods. It uses an electrode with an electric current to fuse together a variety of metals.
The electrode is made of a solid metal stick (or rod) that is surrounded by a coating of metal powders and compounds that includes a binding agent to help bind the surface.
Then, electric current helps to form an electric arc between the metals being fused together and the electrode. The electrode will provide filler metal for the joint by conducting an electric current.
This form of welding is also pretty old, having originated in the 1800s. Over time, the process has been updated using different binders, electrodes, and coating.
How does it work?
Stick welding uses an electrode that has been flux coated to form the weld in a joint. It facilitates the passing through of electric current from the electrode (or welding stick) and the point of contact with the base metal, using an arc.
The electrode will start melting, ad the flux coating that was placed on it will create the shielding gas that prevents the molten metal from oxidizing. (This is why the process is also known as shielded metal arc welding.)
The last part of this process involves a good deal of cleaning because the gas cloud that settles on the metal while it cools turns into slag.
When you have completed your weld, you will need to chip off the slag. It’s a simple process that doesn’t require tons of equipment.
Advantages of Stick Welding
A lot of people like stick welding because it’s very easy.
Stick is the easiest method of welding to learn and master when it comes to technique. On top of that, the equipment itself is easy to use. This process is also very inexpensive, with both the equipment and the rods (or sticks) costing much less money than other methods.
No shielding gas required. On top of this, you save even more money because this method doesn’t require you to find an external shielding gas. This also makes it more portable, because you won’t have to carry around the gas canisters.
It’s also the only welding method that can be used in bad weather. Because it doesn’t have an external shielding gas that can be blown away, this method of welding can be performed in windy and even rainy conditions!
This is also pretty versatile. Your electrode can be changed pretty easily based on the different metals you’re working with and fusing. This means that there is a wide variety of alloys and metals that can easily be welded together using this technique.
It’s also a good option for people who aren’t meticulous enough to constantly clean and prepare their workpiece, or for people who can’t get all the paint or rust off of their weld. This method will even fuse together metal with painted and rusty surfaces.
Disadvantages of Stick Welding
It requires a good technique. Unfortunately, this is a method of welding that requires precise technique, skill, and experience. While it’s easy to learn, it will not produce strong joints without good technique. It’s also a difficult process to use on thinner materials and may lead to distortion and burn-through of your workpiece.
It’s a dirty method of welding, too. The flux coating that burns into the shielding gas will leave all kinds of slag that needs to be chipped away when the weld itself is completed. This is one of the factors that makes stick welding a slow process compared to other welding methods.
This also takes a big toll on your electrodes. Stick welding will require you to replace your electrodes far more frequently than other types of welding, which eventually begins to undo the savings you make through the equipment bein cheaper.
This also doesn’t work as well on larger projects. It only allows short lengths of welding before you need to insert a new electrode, which can lead to a less smooth weld if you’re working for longer lengths. You also can’t use it o any reactive metals. This means that you can’t use this method to weld titanium, tantalum, columbium, or zirconium.
What situations would you use Stick welding for?
Stick welding is popular when welding iron and steel. T is also used more often than any other type of welding when it comes to maintenance, repair, and the construction of steel structures.
Flux Core Welding (FCAW)
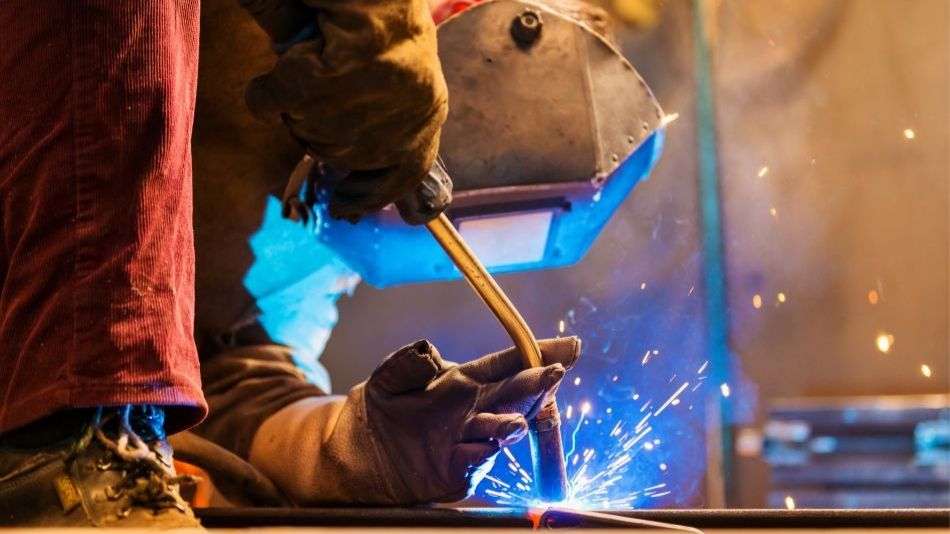
Flux Core Arc Welding (or FCAW) is an alternative method to stick welding. It’s a more automated version that can create a semi-automatic arc weld.
It’s popular in construction because it’s portable and very fast.
What is flux core welding?
Flux core welding is kind of like a mixture of the best features of MIG welding and stick welding.
It uses a continuously fed electrode and nozzle to create an arc and provide filler metal, which makes it similar to MIG welding. The difference is that, like stick welding, the electrode creates its ow shielding gas when it burns.
This method of welding is a hybrid of these processes, which makes it work similarly to them.
It’s not quite as easy as MIG welding, but it’s far easier than stick. This hybrid was invented in the 50s.
How does it work?
Flux core welding works through the use of 3 components: shielding, filler metal, and electricity. You feed an electrode through to the joint by squeezing the gun’s trigger to start the wire feed process.
This feeder then fills the joint. At the same time, the electrode begins to charge. When the electrode touches the joint, it heats the electrode and melts it.
The electrode then causes the filler metal to melt, creating a weld puddle. This puddle will melt the flux core, creating the gas shield from the air and protecting the weld from contamination.
Advantages of Flux Core Welding
Flux core welding is nice because it doesn’t always require a shielding gas. This means it can be used outdoors, even in windy environments. This is also a much faster method to weld, so a lot of high-speed situations prefer this method.
Flux core welding can also handle dirtier metals. While it’s always important to clean and prepare your base metal, flux core welding can de-oxidize rust and mill scale, trapping them in the weld pool’s slag instead of allowing them to contaminate your piece.
This also decreases production time because it can deposit weld metal at much higher rates of speed than the other methods. Despite requiring good technique, it is also easier than TIG and stick welding, so a lot of intermediate users enjoy this process once they’ve mastered MIG welding.
Disadvantages of Flux Core Welding
Unfortunately, there are some downsides to this method as well.
The filler wire for flux core welding is far more expensive than the wire that MIG welding uses, or the sticks and electrodes used in TIG and stick welding. This wire needs to act as both a filler and a shield, which comes with a price.
This is also a far less portable method than other welding methods. The machine can’t move around as much and isn’t as mobile. It is usually also much heavier. It produces more toxic fumes, too, making it less safe than other methods.
Another disadvantage is that when you change your filler wire, you need to change your entire spool. This is much more difficult and time-consuming than just changing filler wire on its own. In this regard, MIG welding is much easier to use.
What situations would you use flux core welding for?
Flux core welding is great to use when you have dirty or impure metals. It is able to de-oxidize them metal during the welding process, just leaving you with some slag to scrape off at the end.
This can be used for a variety of metals and alloys, including nickel and some surfacing alloys. It’s also great at fast production, so it is very convenient to use in automotive assembly fabrication and repair.
Because it doesn’t need a shielding gas, it’s also great for outdoor use. This makes it a popular choice for agricultural welding, out of position welding, and thick materials.