How Does Arc Length Affect a Weld?
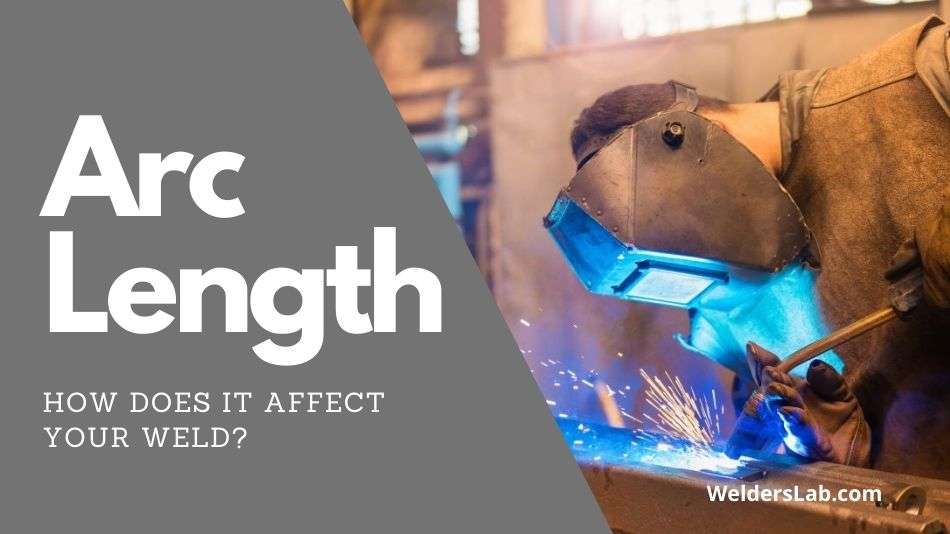
If you learn nothing else from reading what I have to say, I hope that you learn how important it is to perfect your technique and continuously build your skills. Preparation and understanding of what can make or break a quality weld are the two things that will help you survive in this business.
One of the important factors to consider during your welding processes is the length of your arc. The length of the arc does make a difference and there are certain variables to consider in order to determine the best arc length.
How DOES the arc length affect a weld? Arc length is the distance between the welding nozzle and the metal you’re welding. A shorter arc length will keep an adequate amount of shield gas around your weld but will result in more spatter on the nozzle. A longer arc length will result in less shielding gas, a weaker weld, and cause the welder to spit and sputter the wire.
As a welder, it’s your own reputation and potentially a company’s reputation on the line if you mess something up. Now don’t get me wrong, we all make mistakes and sometimes we learn through trial and error what works best.
My point is that you need to make an effort to always do your best, but if you want to avoid this issue keep on reading.
How Does Arc Length Affect a Weld? The Ultimate Guide to Understanding Arc Length
Arc length may just seem like a random factor of your weld but ultimately, that arc length could affect the integrity of your weld, which is the last thing you want. If you want a high-quality and reliable weld, you need to understand your arc length and know how to calculate the appropriate arc length.
For most welding jobs, there are calculations that can be completed and typically a specific range that you can utilize. If you’re a centimeter off, it probably won’t make a huge difference but if you’re 2 inches off on the arc length, your weld could be shot.
As we progress through this guide, I will share with you the things you should know about your arc length in relation to your weld.
Appropriate Arc Length & Understanding Your Range
The definition of arc length is the measurement between the material you’re welding and your electrode tip. This length can vary by the stability of the arc, the current from the voltage, and the part materials.
Ultimately, you want to keep the electrode a specific distance away from the surface you are welding. This distance can vary by material and voltage as well as the speed at which you’re welding. What you mostly need to understand is that the farther away your tip is from the welding material, the weaker the arc is.
Some welders recommend that you keep your tip within 1/4 to 3/8 for an appropriate range. However, some would argue this is getting too far away. If you get too far away, your arc gets too weak and your weld will not only look awful but it also won’t likely penetrate like it is supposed to.
Most practiced TIG welders would tell you to try to keep your arc length within 1/32 to 1/8 of an inch if you can. But remember not to get too close. If you can achieve a steady .10 of an inch arc length, you will achieve perfection.
Keep your tip nice and close to the weld but you definitely don’t want to touch the surface. This is true of nearly any kind of welding machine. You also need to try to stay a consistent length away and move smoothly and steadily so the weld is consistent throughout the entire piece.
You maintain these arc lengths and ranges to ensure that you get proper penetration without contaminating your weld. This gives your weld quality and strength, which are both important.
Don’t Get Too Close!
What happens if your arc length is too short? Well, first of all, it can contaminate your weld or contaminating your tip with the molten metal that you are making with the heat. This can completely ruin your weld or cause build-up in your machine.
You don’t want to risk ruining your machine, those things certainly aren’t cheap. If you get to close to that melted metal of your weld, you might find a nozzle full of spatter or even a melted tip. Both of these things could cause you problems with welding and have a terrible effect on your machine.
Again, remember that this can take practice. You will need a steady hand and focus in order to get your arc within the appropriate length for proper penetration and a quality weld result. The hazards of getting too close mostly relate back to having a negative effect on your machine or your tip.
Don’t Get Too Far Away!
It’s simple right? Don’t get too close and don’t get too far away. Let me remind you, this can take practice. A lot of beginners tend to be too far away because it’s almost like they’re scared of getting too close. It happens! We teach ourselves the appropriate length and technique.
Practice, practice, practice.
What happens if the arc length gets too long? Well, this is where you will see a definitive issue with your weld. You won’t get the penetration that your weld needs. You will end up frustrated because your weld won’t be strong or won’t stick.
If you do get some penetration and a weld when too far away, it probably won’t be strong enough for durability purposes and you will end up with a shoddy weld.
A weld too far away is not strong enough, if you even get traction. It also looks terrible. The weld will be humped in appearance rather than flat, which could cause other issues with whatever it is you’re welding.
When it comes to TIG welding, if you get too far away with your arc you end up with too wide of a weld because your voltage will increase. The heat of that arc spreads out and you don’t have control. You also might be melting metal that you’re not filling, which weakens the overall weld.
Calculating Arc Length
There is somewhat of an art to calculating the appropriate arc length for the best success. How do you calculate arc length? Well, you can calculate in degrees or radians. This does take some math skills and a specific formula. If you understand the formula, you can calculate any arc length.
The formula for calculating arc length in degrees is A = (0/360) x (D x r). In this formula, the individual selections are as follows.
- A – arc length
- 0 – Arc angle, in degrees
- r – circle radius
- D – circle diameter
The formula for calculating arc length in radians is A = r x 0. In this formula, the individual selections are as follows:
- A – arc length
- R – circle radius
- 0 – arc angle, in radians
A scientific calculator can help complete these calculations for you as they can be difficult to calculate. Most welders are not mathematical people, even if we understand the concepts of calculations and measurements.
To get to the point of working with these fractions, it might be required to calculate circumference, which adds another step to the calculation to consider.
These calculations aren’t awful if you understand the terminology and where the numbers should come from.
How Does Speed Factor In?
Speed is another important factor. For one, moving too quickly will mean that you don’t have the control that you need over your process. It also might mean that you’re moving too fast for the weld to penetrate, leading to a shoddy weld.
Two of the biggest mistakes for new welders are the length of the arc and the speed of the weld. Remember these, and do your part to practice and improve your processes. It’s not always about moving fast and just getting the weld done.
It’s more about the quality. If you rush through a job, you’re not saving yourself time when you have to grind off that weld and do it all over again. Or when you have an angry customer because your weld broke. You won’t do yourself any favors by speeding through the process.
The appropriate speed is based upon the flow and amperage of your machine, the material you’re welding, and the thickness of what you’re welding. You want to move quickly but you always want a high-quality weld.
Conclusion
I hope that you find this guide to understanding arc length and the effects it can have on your weld to be a valuable resource. Remember that my knowledge comes from years in the field. I’ve had time to practice and improve my skills and learn from my own mistakes along the way.
Don’t be scared away by the complexity and focus required. Welding is a tradeable skill. It takes practice to improve and sometimes you just need to know where to start or what to focus towards in order to know how you can improve your own welding capabilities.