Can You Mig Weld Aluminum Without a Spool Gun
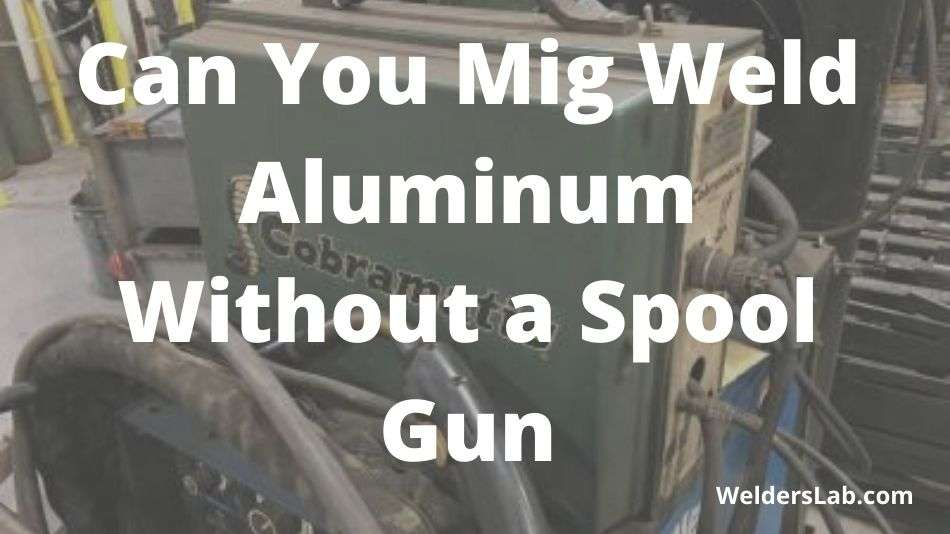
In my early days of being a welder, I was always curious about different ways I could weld things together. Aluminum was no exception to that rule and after a little bit of tinkering around, I was able to use a MIG welder to weld aluminum together.
Can you MIG weld aluminum without a spool gun? Yes, you can weld aluminum with a MIG welder. To do this you will need to loosen spring tension to avoid the wire from snapping as it pulls through the feed rollers. You’ll also want to keep the weld lead and liner as straight as possible to avoid the wire from kinking as it is very fragile.
One of the things a lot of beginners want to know is can you weld aluminum with a MIG welder without the expensive spool gun accessory. This article will answer that question, then provide you with some great tips for handling MIG welding aluminum.
Can you weld aluminum with a MIG welder without a spool gun?
It is possible to weld without a spool gun, but it will take a lot of skill and practice. If you want to succeed, you will need to know how to create and maintain a very stable arc.
Because the spool gun has such a small feed distance, it can offer rapid and steady feeding for your aluminum wire. The smooth wire feed it creates is what makes such a beautiful, stable arc.
You will, therefore, need to be able to create that smooth arc on your own, and this can be hard to do with a MIG welder since it has a much longer lead.
What kind of welder do you need?
If you have a MIG welder, you can adapt your settings to handle aluminum wire instead.
It will take a lot of adjustments but if you can find the right settings and have the patience to experiment, you will find that you can weld aluminum without the spool gun.
What extra equipment will you need to weld aluminum?
Because we are talking about aluminum, there is still quite a bit of equipment you will need.
Safety Gear. First and foremost, you will need your safety gear. It will prevent you from getting arc eye, from catching fire, from a stray spark bursting through your eardrum and causing deafness, and other hazards. This is especially important with high heats.
Drive Rolls. You’re also going to need special drive rolls for the task. You need rolls that can produce a steady feed and grip the soft metal without pulverizing it or picking up steel dust.
Wire. Along with this, you’ll need the right type of wire. Aluminum MIG wire 4043 and 5356 are good options.
Tips. Using 030 wire and an 035 tip can also help since aluminum tends to expand when it reaches its flashpoint.
Gas. You will also need 100% argon shielding gas rather than the mixture.
Drive Rolls
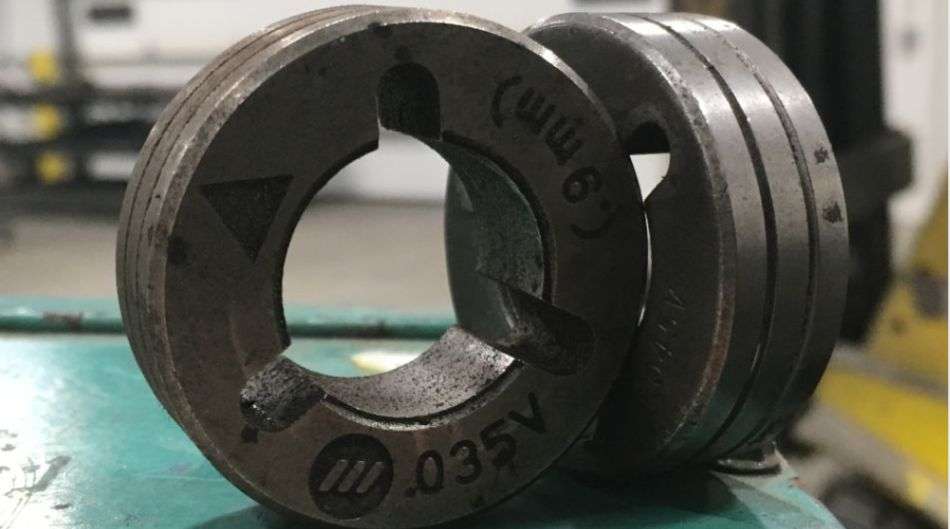
When it comes to aluminum wire, the rule of thumb is more drive in the rollers is better. The more drive your rollers have, the better it can handle the aluminum wire.
The drive rollers will offer a better grip than undriven rollers while also maintaining less pressure on the soft aluminum.
This is a great option because the problem with rollers that only guide is that they will add a lot of resistance to your feed system.
You also want to make sure that your wire drive is clean. You should always clean your drive and rollers before you try to put the aluminum wire into your welder.
If your aluminum wire picks up any of the dust from steel welds, it will add too much resistance. The wire will also pick it up and carry it into your weld, which will contaminate it.
When you’re picking a roller, make sure it is smooth and clean. Some manufacturers sell specific rollers that were made only for aluminum, so you may be able to purchase one for your welder.
If you’re looking for this type of drive roller, it is going to have a deep U-groove with a lot of polish. This will avoid any distortion your wire may have without the extra grip. If you can find rubber rollers, these would be awesome choices!
If you need a lot of tension and the smooth rollers start to deform and ruin your wire, consider knurled rollers instead.
A lot of MIG machines actually include these in their box because they’re perfect for flux-cored wire. These offer better grip when it comes to holding and feeding your wire, so you can release the pressure on your rollers and avoid damaging your wires.
Liner
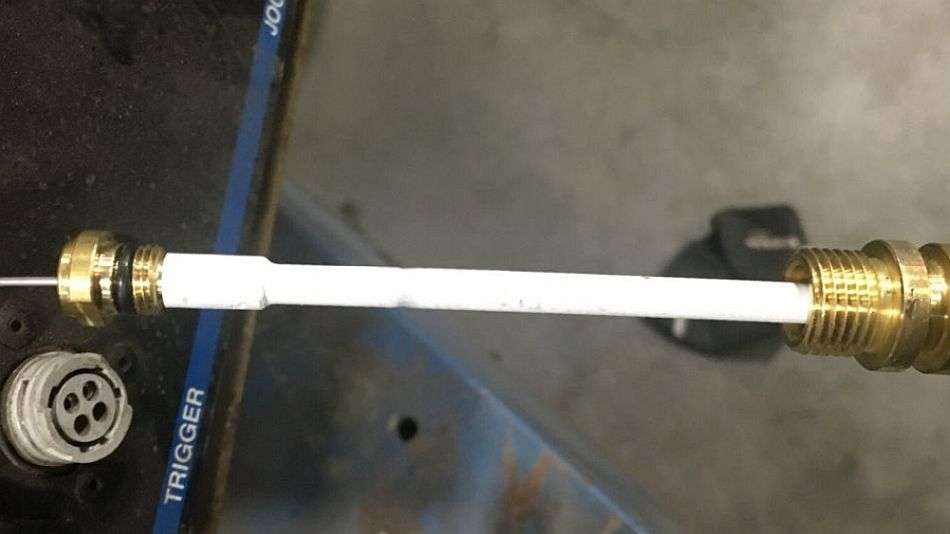
You should also try to avoid putting too much tension on your rollers. You want enough pressure to allow the drive to roll smoothly and feed your wire through at a steady pace without it slipping around, but too much tension will end up pulverizing your wire. This will create a lot of unnecessary drag on your liner.
The tension setting is going to take a lot of practice and experiment to find this balance, so test it out before you try using it on your important welds. You need to strike the balance that allows the liner to guide the wire through, without too much pressure or too little. Both of those will lead to contamination and uneven feeding. These issues compound with unstable arcs and cause porosity in your weld.
Welding Wire
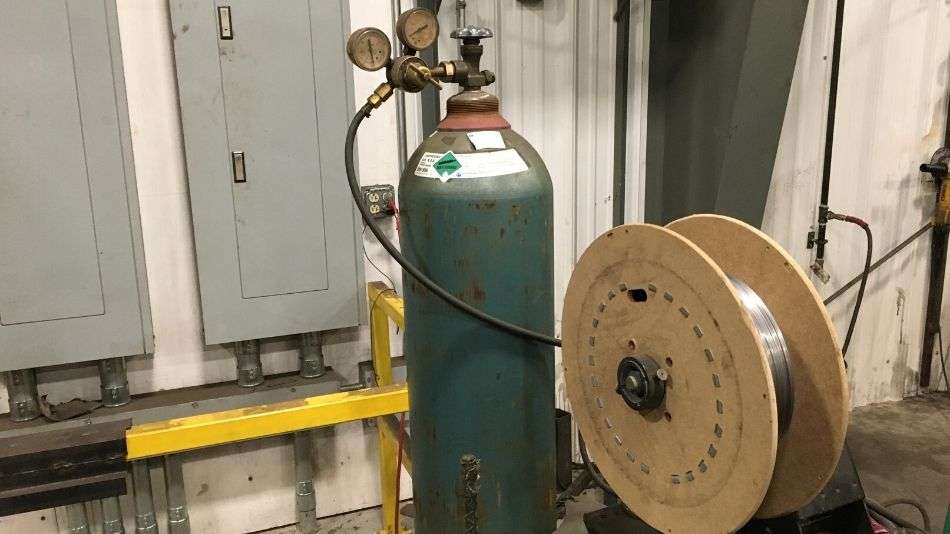
When it comes to the wire, you will likely want to use Aluminum MIG wire 4043, which is standard. Some people like 5356 instead because the extra rigidity will prevent it from bird caging when it runs through the machine.
You will also want to use an 030 wire for MIG welding aluminum. Despite this, a lot of people prefer the 035 tips with the 030 wire.
Aluminum will expend when it hits its flashpoint. If your tip is meant for the wire’s original size, it could cause your tip to jam.
The 035 tip is still small enough to work well with the 030 wire, but it allows a bit of extra space to avoid jams when the metal expands.
Gas
You need to pick the right gas for the job. Aluminum is non-ferrous. This means that it will need a 100% argon shielding gas.
It may be tempting to save money through combinations, but this won’t work with such a delicate and soft metal.
You will only end up causing problems for yourself. Stick to the 100% pure argon gas and allow it to go through at a flow rate somewhere between 20 to 30 cubic feet per hour.
2 Tips to Weld Aluminum
Can you weld aluminum with a wire welder? Yes, if you have good technique. Welding aluminum can be a bit tricky.
Even professionals have difficulty sometimes. Here are some tips to make the task easier.
#1 Weld Angle
When you’re working with aluminum, the settings and techniques need to be flawless. Your skill level, the joint type, and the positions and fit up will all impact whether or not the aluminum weld can even be attempted.
When it comes to the skills, there are a few things you can do to increase your chances.
First, practice! Next, think about the technique. For welding aluminum, you want to have your nozzle and the tip pointing in the direction that you are traveling.
Use a push travel angle of 10 to 15 degrees. Never pull or drag when welding aluminum. This will create dirty welds with high porosity because the gas won’t be able to shield the area properly.
Make sure that you’re observing the right distance between your tip and your work. The contact tip should be about 1/8 of an inch inside the nozzle whenever possible.
Because the puddle and reflective heat are extremely hot with aluminum welding, it is important that you control the tip distance if you want to avoid burning the wire through to the contact tip or burn through on your sheet metal.
You also want to avoid large beads from weaving with aluminum. If you need to weld a large fillet, then get ready to make a lot of passes.
When you use straight beads that get layered through multiple passes, your weld will look much prettier and be far less likely to see defects, burn through, or cold lapping.
Keep an eye on your travel speed, because if your material starts getting hot you may need to travel faster.
#2 Welder Lead
Keep this short since you don’t have a spool gun. The reason the spool gun works so well for aluminum welding is that it has a very short lead, which keeps the wire feed very stable and steady.
That stability and consistency in the feed are what cause such a perfect arc. A smooth arc is critical to welding aluminum without destroying it or burning through it.
Frequently Asked Questions
Here are a few more questions that get asked a lot when it comes to welding aluminum. Hopefully, they will answer any lingering thoughts in your mind.
Is it hard to weld aluminum?
Welding aluminum is much trickier than welding mild steel, which is why a lot of welders are willing to invest in the spool gun that is designed to make the task easier.
What happens if you MIG weld aluminum without gas?
No. Aluminum oxidizes very quickly. There’s a reason it is tricky to work with and needs to be perfectly prepped ahead of time.
In fact, not only is it not possible to weld aluminum without gas, but it’s also not recommended to weld without 100% argon gas because that’s the only one that can shield enough of the space to prevent problems with oxidation and porosity.
What’s the benefit of having a spool gun to MIG weld aluminum?
One of the benefits of the spool gun is that it has a very short lead. The shorter the lead, the better the feed.
It’s less likely that the feed wire is going to get stuck on its way through the rolls and it’s also easier to create a steady and smooth arc when the wire comes through so consistently.
Conclusion
Have you tried to weld aluminum with your MIG welder?
Hopefully, the next time you try to weld aluminum without a spool gun you will be a little better informed.
It takes great technique and some experimentation with the settings, but eventually, you’ll be welding like a pro!