How to Stop Metal From Warping While Welding
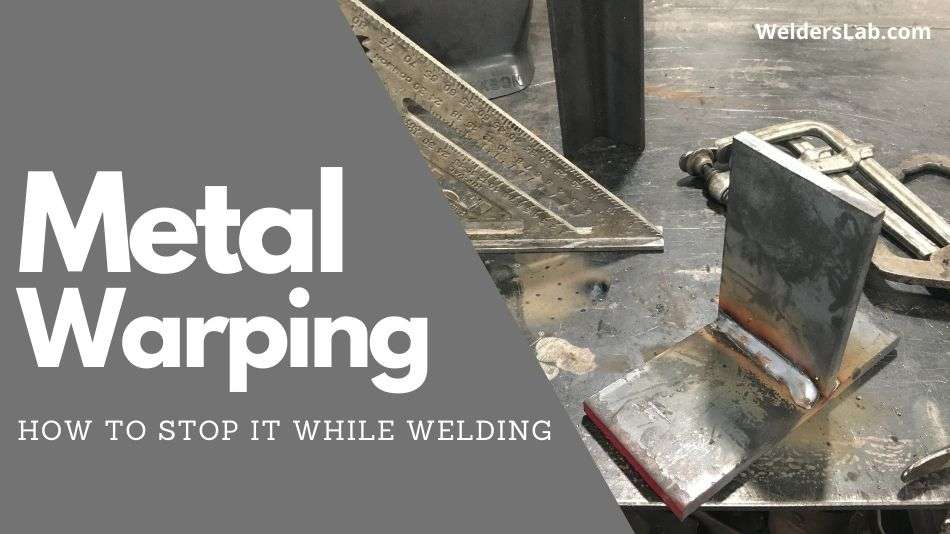
When metal warps while welding it is called weld distortion. Expert welders and beginners alike have to deal with this problem. How to stop metal from warping while welding is an important part of the craft. There are multiple causes of weld distortion. Lucky for us there are also several solutions.
How do you stop metal from warping while you are welding? Start by clamping down the metal. Weld light tacks and add bracing to keep the metal in place. As you weld the metal, keep a proportionate weld by welding opposing sides evenly. Finally, don’t overheat the metal and let it cool to prevent further warping.
In this article, we will get into some of the details about each of those. We will also look at what causes the metal to warp and some of the tools I use to prevent metal warping while welding. There is a lot to cover on the topic. Let’s get to it.
How to stop metal from warping while welding
There are basically five ways to prevent metal from warping when you are welding. They are clamping, bracing, laying a proper bead, proper tacking, and cooling.
Each one of these could be required at a moment’s notice. Staying knowledgeable about the various techniques and when to apply them will be helpful.
#1 Clamping
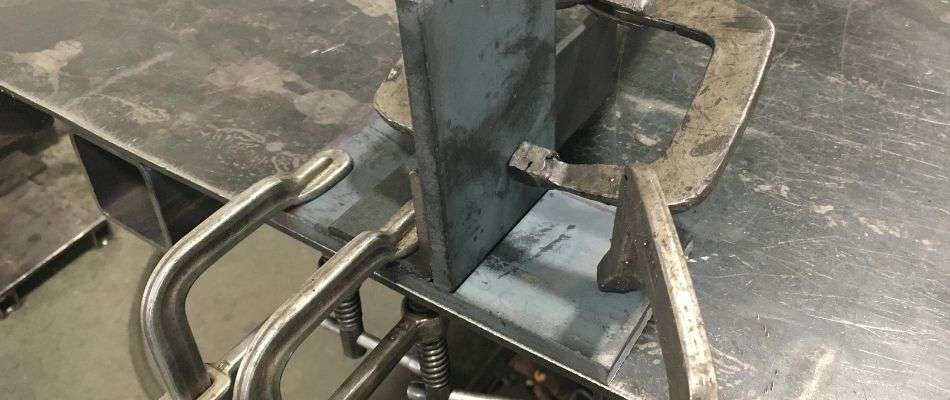
Proper clamping of the metal will help prevent weld distortion. You want to make certain you are using the best clamps available.
You also want to ensure you are using the right clamps for the job and materials. If you are using the wrong equipment or apply the clamps in a less-than-secure fashion you might still experience warping.
Be certain you have everything secure and correct from the beginning.
#2 Tacking
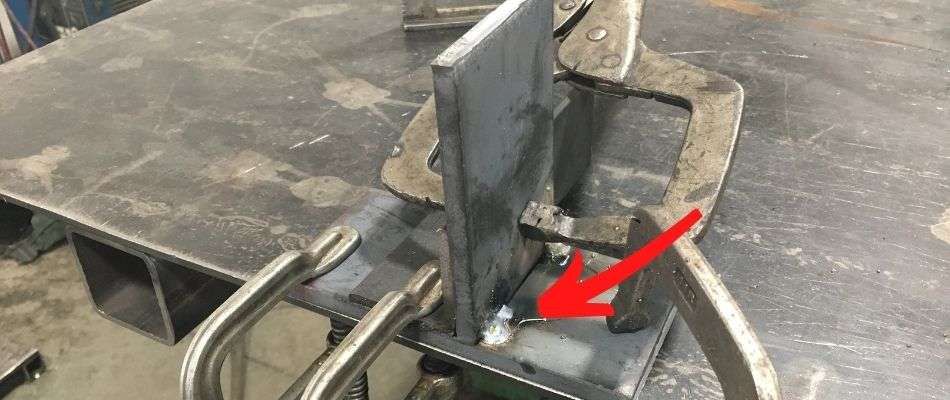
Properly tacking the metal in the right place will go a long way to prevent warping. If you tack things in place first, you will help secure the material before you lay down a solid weld.
It is important you tack on the front and opposite sides before you start welding. This will help stop the weld from pulling.
#3 Weld Proportionately
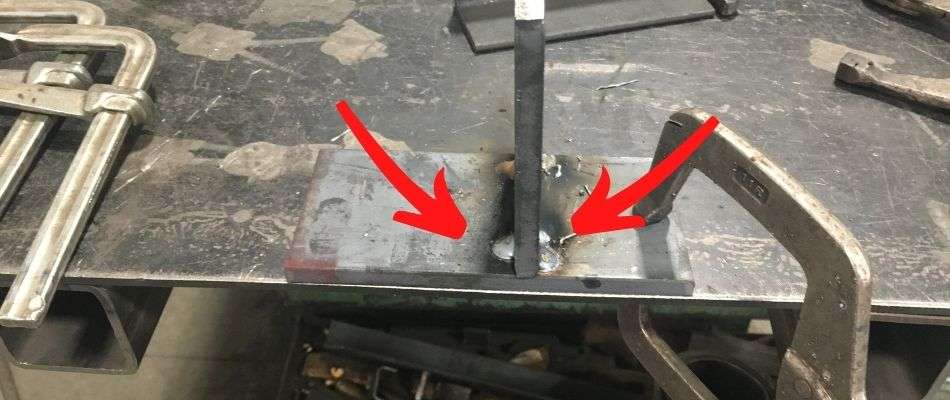
Laying a proper bead in the right place and at the right time also prevents weld distortion. If you have a particularly long bead to lay, consider breaking it up into short segments.
Doing so will decrease the chances of warping the metal. That is because it gives the metal time to cool down between welds.
Make sure you are timing the bead properly based on the materials you are using.
#4 Use Bracing
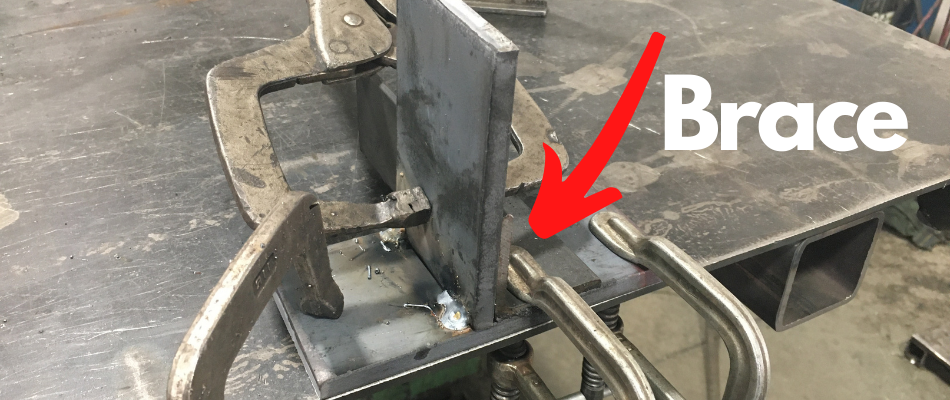
Another thing to consider is bracing. If you can add additional bracing or gussets you can help prevent warping metal. This works by increasing strength.
It also helps hold the metal in place. Keeping things locked down and held fast in this way will go a long way to decrease warping metal while welding.
Applying any of these techniques will decrease the chances of warping metal. How you apply them and at what time will depend on the individual circumstances of the job you are on.
Materials, settings, and the scope of the project will make a difference to your end results. Just keep your eyes and ears open at all times, stay aware of your options, and you should do fine.
#5 Cool Down
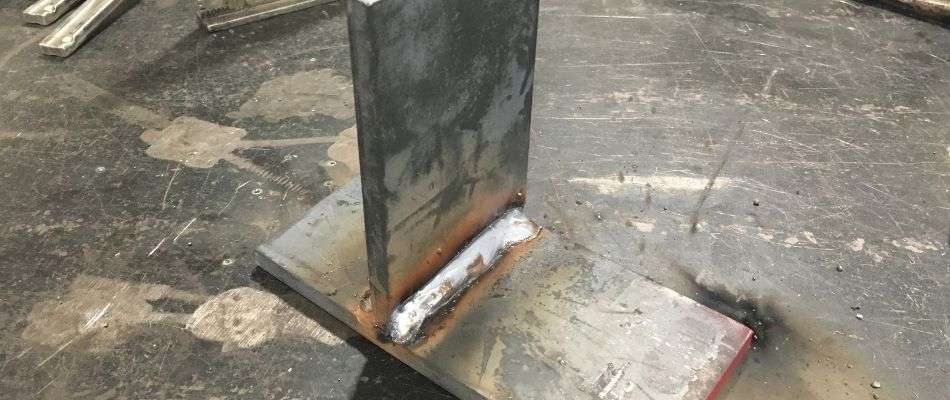
Let things cool down by taking breaks. If you are running high amperage and hot welds you can warp the metal.
By taking breaks as you work on the project you give the metal time to cool down. The hotter it gets the more likely it is to warp.
If you keep it hot for a long time the chances of weld distortion increase.
What causes the metal to warp when welding?
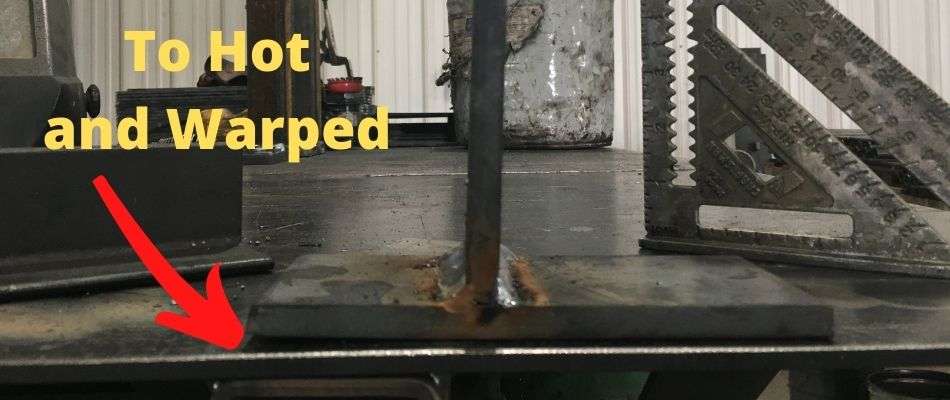
When metal gets too hot it will begin to warp. That is common knowledge. As welders, we want to avoid warping metal at all costs.
The best way to do that is to know what causes it to warp in the first place. Essentially, as the metal gets hot or cools down it will change shape by pulling in one direction or the other.
If you take a metal bar and heat it uniformly then cool it uniformly it will expand and contract according to its original dimensions.
But if you heat that metal bar while it is in a vice it will expand in a distorted manner. When it cools down it will contract according to the constraints of the vice. In other words, it will become permanently deformed.
On a welding project, the same principles are at play. Depending on how the metal is braced or clamped and what temperatures you are working with the metal can react by warping.
That’s why it is important to clamp strategically and firmly. Giving the metal time to cool down in intervals is also a safe way to prevent permanent distortion.
Certain metals will warp more easily than others. If the metal you are working with is thin, there is a greater chance of it warping.
Stainless steel will also warp pretty easily if you do not know what you are doing. Proper clamping and good welding technique go a long way here. I found this out the hard way when I tried to weld a gate out of stainless steel.
Because of the type of metal stainless is it warped severely ruining my jig. If I would have tacked things together, clamped thing properly, and welded the gate in a particular way I’m sure I could have limited the warping but that comes with experience.
Tools I use to prevent warping while welding
There are a lot of techniques good welders use to prevent warping. Light passes or limiting the number of passes, anticipating shrinkage, and moving around the project to keep a good eye on the materials are a few of those.
You also want to make sure you fix any mistakes right away and consider intermittent or backstep welding.
#1 Ball Peen Hammer
But there are also various tools you can use to prevent warping. The good old-fashioned ball-peen hammer is one. Peening is when you lightly tap the bead while it is cooling.
This creates some dents and relieves stress. It is not a major solution, but it might make a difference in a critical weld.
Do not overdo it though. Too much and you could compromise the strength of the weld.
#2 Clamps
Welding clamps, vices, and jigs help control distortion. They do so by holding the materials in place and at the correct angles for the project.
Clamps and vices will only control distortion if they are placed correctly and in the right places before you begin welding.
You must use the best clamps you can get. Any weakness in the clamp or vice will weaken the hold on the parts. If that happens and the metal gets too hot you will increase the chances of warpage.
I prefer Bessy bar clamps. They are well made and hold well. An 11r locking c-clamp is also great for this work. In addition, a good pair of vice grips help keep materials in place while welding.
Final Thoughts…
Experts and beginners alike encounter the problem of metal warping while welding. Metal warps or distorts when welding because it gets hot and changes shape.
As it cools down it wants to return to its original shape but usually cannot because of the constraints of the welding process. Warping can occur for various reasons including:
- the type of metal you are working with
- amperage and temperatures
- and timing and technique
There are ways to prevent metal from warping including clamping, adding extra bracing, and tacking metal in place. Laying the bead properly and at the right speed will also decrease the chances of distortion.
In addition, allowing the metal to cool while you are doing the job is another good way to protect from the warpage.
For the masterful welder, applying proper technique will not always ensure protection from weld distortion, but it helps. Intermittent welding, backstep welding, peening, and walking around the job are other things to consider for keeping everything straight on a welding project.
Limiting the number of passes and making lighter passes are effective techniques to stop metal from warping when welding, also.
Remember that practice makes perfect. If you are a beginning welder there is nothing more important than getting practice.
By regularly practicing you will become more and more familiar with the art and craft of welding. You will be better equipped to recognize the signs of distortion and adjust your process the more time you get under your belt.
Not only that, you will get faster. Welding with a little bit of speed on your side will decrease the chances of metal warp.
As always practice safe welding and make sure you have plenty of room. You want to make sure there is ample space for any welding restraints you will use like c-clamps, bar clamps, welding jigs, and vice grips.
You are working with hot metal that under restraint has a limited number of places it can release pressure.
Hot metal can be unpredictable and if a clamp or restraint happens to pop off or gets bumped into it can cause a whole lot more trouble than it is worth. Always keep an open welding area and plenty of ventilation too.