What is the Best Way to Weld Thin Metal?
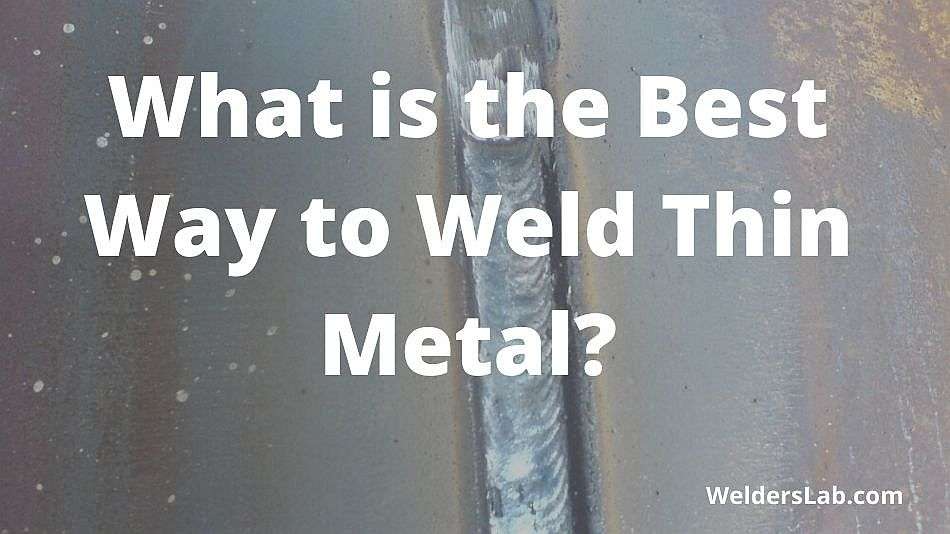
I’ve always found thin metal to be challenging to work with. It seems as though it’s the hardest to get to cooperate, to an extent. Of course, thin metal can be weak although it’s not usually brittle. The thinness and the contents of the metal often are the challenge and I have to prepare myself to work with them appropriately.
What is the best way to weld thin metal? MIG welding is a great solution for welding thin metal. However, TIG welding is probably the best solution but it can be the hardest to learn use. With the proper setting, a MIG welder can work great for welding thin metal together.
In this guide, we will be discussing the best way to work with thin metal. We will talk about the types of welding and some pro tips to help you through the process so that you can weld your metal successfully. You’re not going to want to miss out on the information I have to share here!
Stick with me to learn the best way to weld thin metal and more.
What is the Best Way to Weld Thin Metal? A Complete Guide to the Process
Some people might take a look at aluminum or some mild steel and wonder “can you weld thin metal?”. I assure you, it’s absolutely possible and it doesn’t have to be too difficult.
Yes, thin metal is perhaps one of the more challenging metals to work with, but if you take the time to learn the processes and work through them, you will find it’s not so bad.
What we truly want to portray here is that welding thin metal is nothing to be afraid of. Hone your skills, learn the techniques, and give it your best shot!
The Process for Welding Thin Metal Together
As with any welding job, you must first remember that there is a total process to follow.
No matter what type of metal you are working with, following your processes is incredibly important from start to finish.
Don’t skip steps, do not pass go – just do the process, and do it correctly. This is how you get a successful weld.
1. Clean the Surface
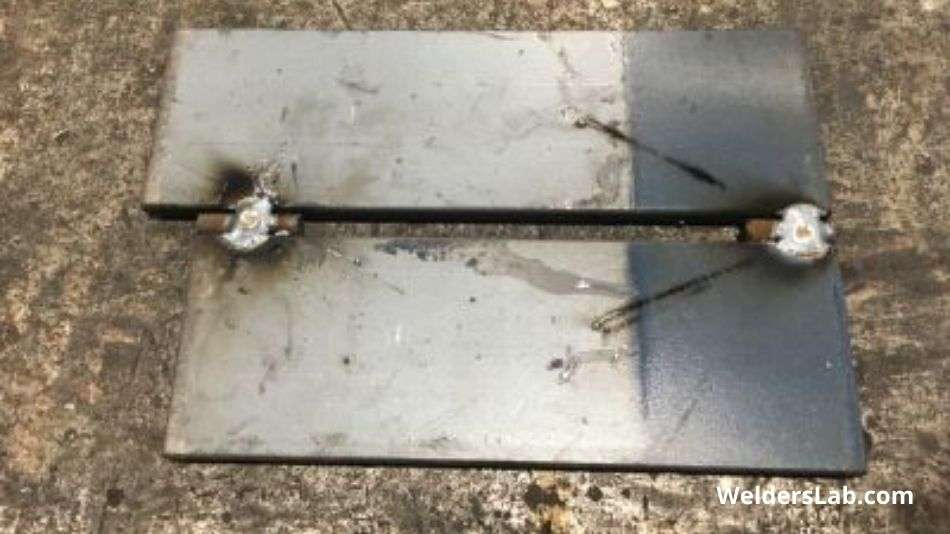
I know you know this step quite well. It’s always the first thing you do. If you skip this step, you could potentially ruin your weld.
There are visible properties that need to be cleaned from the welding surface, like paint, oil, rust, etc. However, then there are also invisible properties that could impact your weld.
Do yourself a favor and take the cleaning step seriously. Get out your cleaner, your wire brush, and your grinder (if necessary), and set to work cleaning the surface.
Start by stripping and removing paint as well as sanding away any rust or other residue. You need these out of your way before you even start. This is particularly true of thin metal since it presents its own welding challenges even with a clean surface.
Once you’ve taken off any coatings or residues, use your cleaner and wipe down the surface to get rid of oils, grease, and so forth. This is how you prepare your thin metal surface for success.
2. Adjust Welder Settings
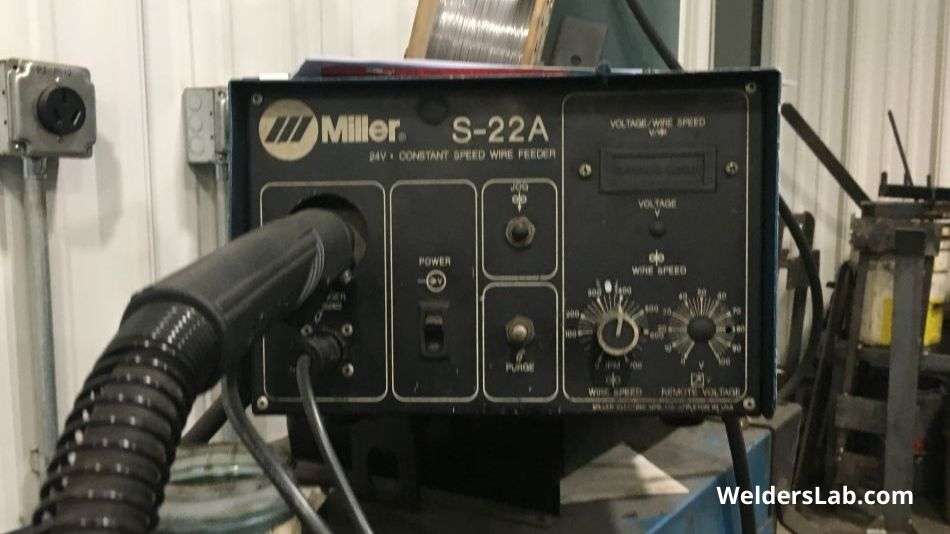
We’ve already mentioned that when working with thin metals, MIG or TIG welding is your best approach. Choosing the right settings within these welding types can also make a significant difference as to whether or not you have a successful welding experience.
The last thing you want to do is worry about having a blow through or something else like that occurs. These things can be reduced or prevented by using the proper amperage and the proper wire speed as well.
I recommend using a reduced amp level, staying well below 35. It’s best if you can stay below 30 to be on the safe side. Of course, having the right amp only goes so far, you need the appropriate wire as well. Try using .8mm or .6 mm with this amp pairing and see how that does for you.
Of course, the speed of your wire and the amp you use could potentially vary based on the job you’re doing but this gives you a good point of reference. Your power might just give you a minimum option, and that’s a good place to start.
3. Weld Small Stitch Welds
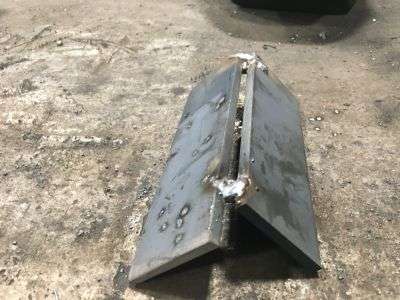
You’ve prepared your surface and you’ve got your welding settings just right, now how do you go about actually welding thin metal?
In this case, slow and steady wins the race. Don’t try to fool yourself into believing that you can just breeze right through this welding job. You need to take your time and work slowly to do it right.
You should use small stitch welds to weld thin metal together. Do this by welding in short pulses, allowing less than a second of time to elapse between each pulse for the steel to cool slightly.
You typically only need about half a second to a second in between pulses. You don’t want the joints to get cold as this could lead to pinholes in the welds.
What Kind of Tools Are Used for Welding Thin Metal?
We’ve already covered your wire in the previous section. The thinner the wire the better, although we know that this could vary depending on your job site and your materials.
There are specifically two types of tools that are optimal for welding thin metal, and then of course accessories and gears to go with these tools.
Yes, it’s truly that simple. If you equip yourself with the proper welding equipment, then you can expect to have a much easier time throughout your welding process.
These welders are great for welding thin metals because you can use a reduced heat, allowing you to heat the metal less. The ability to use smaller wires and lower amperage gives you more control of your weld overall.
With MIG or TIG welders, you are more likely to weld thin metal successfully but you are also less likely to make mistakes, particularly if you follow the steps and guidelines I provided in the previous section.
The right tools go a long way to getting that welding job done right and not having an overly challenging time.
My 7 Best Tips to Welding Thin Metal
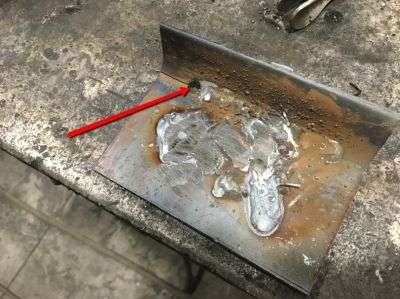
We’ve covered a lot of information here to help you achieve welding thin metal. Understand that thin metal will present its challenges but if you follow the tips and procedures we’ve shared here, you can absolutely do it.
Give yourself some grace, it does take practice and skill-building to get to the point where you can weld perfectly and comfortably every time.
Even after years in the industry, there are times I still make mistakes and am uncertain about how to approach certain welding jobs.
It’s ok to face challenges and it’s even better to be willing to face those challenges head-on and continue to build on your skills and experience to better yourself.
Here are some of my top tips for welding thin metal.
- Use a MIG or TIG welder
- Use minimum power (below 30-35, if possible)
- Use thin wire, .6mm and .8mm are great but this could vary
- As a rule, don’t use filler metal that is thicker than your base metal
- Use smaller electrodes
- Don’t whip or weave your torch, rather work in short pulses making small stitch welds
- For most metals, use higher argon shielding gas levels for reduced heat
While these tips are certainly not a fail-safe means to perfect welding for thin metal, they will go a long way to help you through the process.
I think you will find that if you follow these simple tips and tricks, you will have a far better experience trying to weld thin metals.
No matter what type of metal you are working with, if it’s a thin metal you can typically take these tips to heart and find your welding job going much smoother than if you just wing it.
Conclusion
Don’t let welding thin metal scare you. It’s simply another part of the job that you need to learn to master and build your skills. Not one of us starts out welding every type of metal perfectly every single time.
Welding takes practice, skill, and focus to do properly and there are just some materials that are much harder to weld than others.
Remember to take your time and use these tips I’ve provided. Mistakes happen but these tips will help you be more successful if you give the job at hand your full attention.