How Thick of Metal Can You MIG Weld?
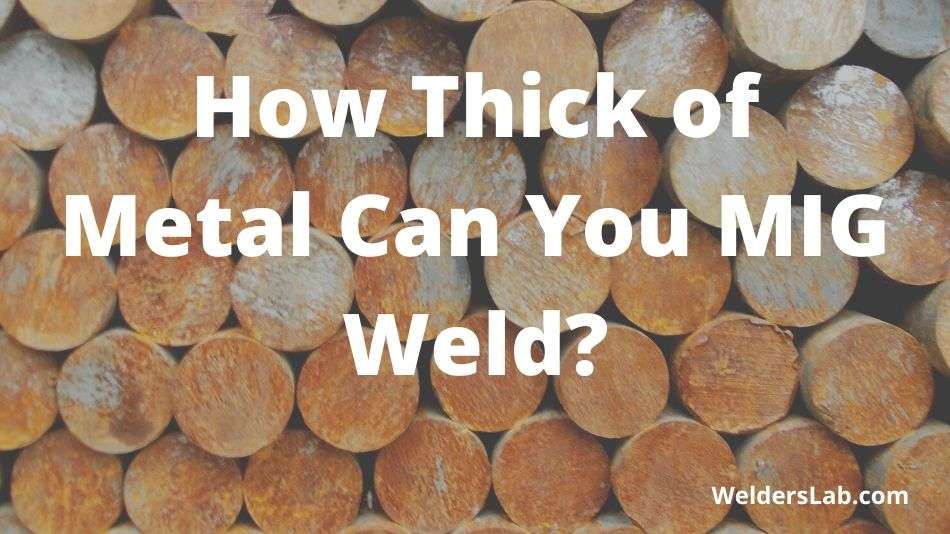
One thing I’ve learned quite well throughout my welding years is that every type of welding has its limitation. MIG welding is one that I use quite often but of course, it’s best for certain types of metals, particularly certain thicknesses.
It’s important to keep in mind the functionality and capabilities of your tools so that your welding job is accurate and flawless. After all, this is most likely your livelihood.
So how thick of metal can you MIG weld? You can weld relatively thick materials, including structural materials. In general, you can expect your MIG welder to be able to weld .001 thickness for every amp. So, the answer is fairly open-ended depending on your amperage capabilities. Another translation to this might be that you can weld a 1/4-inch for every 250 amps.
In this guide, we will cover the options and capabilities that a MIG welder can provide, including discovering just how thick of metal you can MIG weld.
No one type of welding encompasses every type or thickness of metal but we want you to be informed as to just what you can accomplish with your MIG welder and how you should go about accomplishing your tasks.
Keep reading to learn how thick of metal you can MIG weld and so much more.
How Thick of Metal Can You MIG Weld – The Ultimate Guide
Thick metal is not off-limits when it comes to MIG welding, you simply need to know the technique to use and what to expect.
There are of course certain limitations. If you try to weld something that is too thick for your MIG welder capabilities, then you will probably not get a very good weld and possibly not even a connection.
The purpose of this guide is to simply keep you informed as to how you weld thick metal and what you can expect to help you through the process.
Understanding that there are certain limitations will help you because you don’t want to think you can achieve a weld that you really might not be able to achieve with your MIG tools.
What is the Thickest Metal You Can Weld?
There is one thing you should know before we get started. The type of metal might also have an impact on the thickness of metal that your welder can weld.
For instance, when welding aluminum, the heat dissipates much more quickly than if you were welding something like mild steel.
When it comes to aluminum, the thickness your machine can handle will probably be about 20% less. Of course, aluminum is fairly thin anyway but this is something to be aware of.
There are 4 different primary types of MIG welding and each of these also has different capabilities. To truly understand how thick of metal you can weld.
To understand what YOUR MIG welder is capable of, I recommend that you first refer to the voltage chart on your machine.
Every welding machine has one. The chart tells you what amperage to use for what thickness and even tells you what maximum thickness your welder can accommodate based on the amps.
Metal Thickness | Amperage |
1/8″ Mild Steel | 125 Amps |
1/4″ Mild Steel | 250 Amps |
3/8″ Mild Steel | 375 Amps |
1/2″ Mild Steel | 500 Amps |
For example, the chart might say that 230 volts (roughly 210 amps) can weld 3/8” thickness. Now, don’t let that get you down. That doesn’t mean you can’t weld any higher.
What it means is that is the maximum thickness you can weld in a single pass – there is a difference, and understanding that could allow you to weld substantially thicker materials.
You should take on the challenges of thicker materials by understanding that you will need to use multiple passes at maximum power.
Don’t assume that because your chart says you can’t weld a 1/2-inch thickness you truly can’t.
The chart is a guideline for welding in a single pass. So, no you can’t weld that thickness in a single pass but you can weld that thickness with other methods.
How to Weld Thick Metal – The Complete Process
The question of the day is can you weld thick metal? And yes, you absolutely can. We’ve indicated that every machine has limitations but what you truly need to understand is taking those limitations and using them to get the job done.
You saw in the previous section that you can find the maximum single-pass welding capabilities on the chart on your machine. But how can you weld thick metal beyond those measurements?
First, you should know that there are four types of MIG transfer that are used. The most common is known as the short-circuit method. Here are the four types.
- Short-circuit (least amount of heat)
- Spray transfer
- Globular transfer
- Pulse MIG
Next, you should understand how to use these transfer methods and when to use them. I can tell you that the short-circuit method is probably what you will use the most. It is the most common method and I use it often.
Here are the steps to welding thick metal, in a complete guide.
1. Clean Surfaces
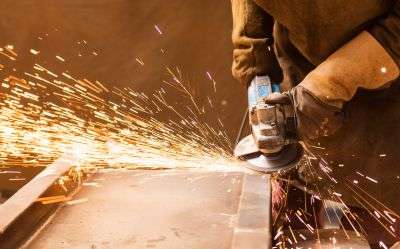
If you’ve read any of my material before now, you know that cleaning your surface is always the first step. Welding thick metal is exceptionally challenging because it’s pushing your skills and your machine to the limits and it will take some time and significant effort.
Set yourself up for success and take the time to clean your surface accordingly. This means to start by stripping, grinding, sanding, or whatever you need to do to get rid of paint, grime, rust, and any other form of debris on your surface.
Then follow that up with your cleaner and wipe down the surface to remove any residue as well as any oil or grease that could impact the weld of the surface area.
2. Preheat Your Surface

Since you are working with thicker metal than usual, it will help to preheat your surface. Preheating your material will make it more pliable and more susceptible to your welding demands.
For preheating purposes, I recommend preheating to somewhere between 150 and 300 degrees Fahrenheit.
This is simply a preparation step. It gets your metal heated and makes your metal much more likely to receive a weld when you get to that part of the process.
Your end goal is to make penetration of the metal much easier. Pre-heating your metal and getting it ready to receive a weld in this way will make the penetration process work far better.
3. Use Proper Shielding Gas
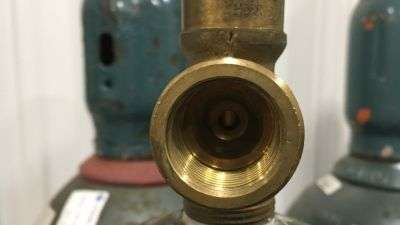
Your shielding gas mixes and ratios can have an impact on the value of your weld. Your best bet is to have a reduced argon level in the mix.
You can go with something that is like 75% argon and 25% CO2. This is one of the most common shielding gas mixes for MIG and it tends to have a high success rate.
Don’t rely on this to be your only shielding gas mixture, however. In this case, working with thick metal, you need something that burns hotter, which may mean reducing the argon to get more heat.
4. Practice and Training
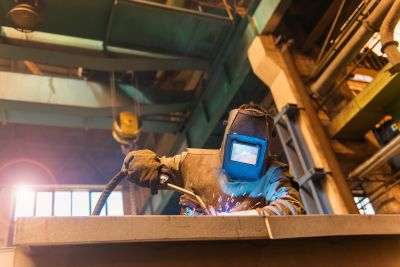
Welding thick metal is not simple. You will need to develop your skills and practice to get your welding skills as good as they can possibly be.
You may need to approach thick metal with another form of welding until you can have time to train and practice your skills.
Don’t sell yourself short but just understand that it may take practice and training for you to be able to successfully MIG weld thick metal materials.
6 Tips to Welding Thick Metal
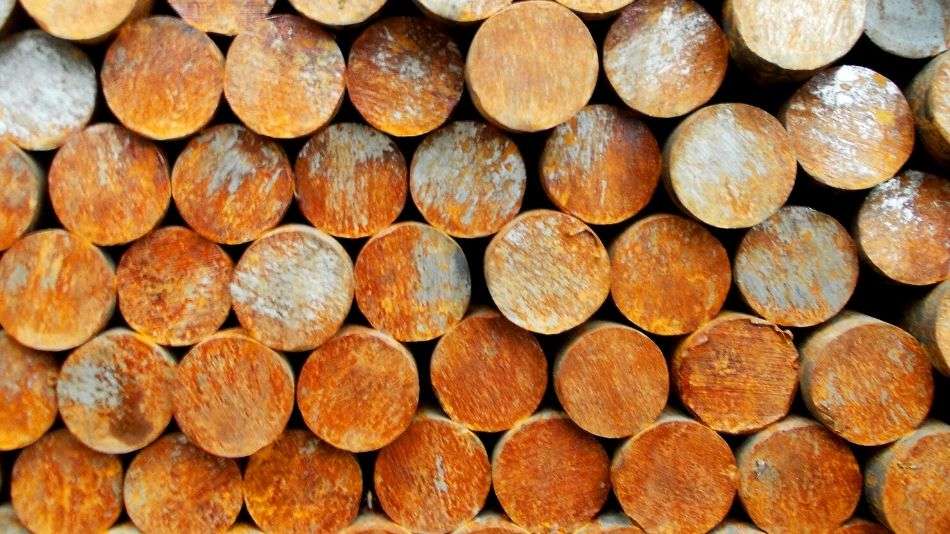
There are several tips that can help you weld thick metal that we’ve covered here. The thing to keep in mind is that if you struggle with a weld, it’s ok.
Remember that it can take years of training and skill-building to figure out technique and heating methods to truly be able to weld thick metal and to get it to stick.
Here are my tips to remember.
- Use your chart as a general guideline for the thickness capabilities of your welder. Understand that thickness beyond that requires more than a single pass.
- Preheat your thick surfaces to make them more pliable.
- Don’t skip the cleaning step.
- Understand that the ability to fuse thick pieces sometimes comes with practice and training.
- Work your skills to improve.
- Choose your shielding gas combo wisely.
Conclusion
There is no promise that you will be able to weld any thickness. Remember that your machine certainly does have limitations when it comes to MIG welding.
Practice really does make perfect and until you hone your skills, you may need to use another welding type to work with thicker materials.
There is nothing too thick to weld but the thickness can be challenging so don’t give up!