How to Set Wire Speed on a MIG Welder – A Helpful Guide
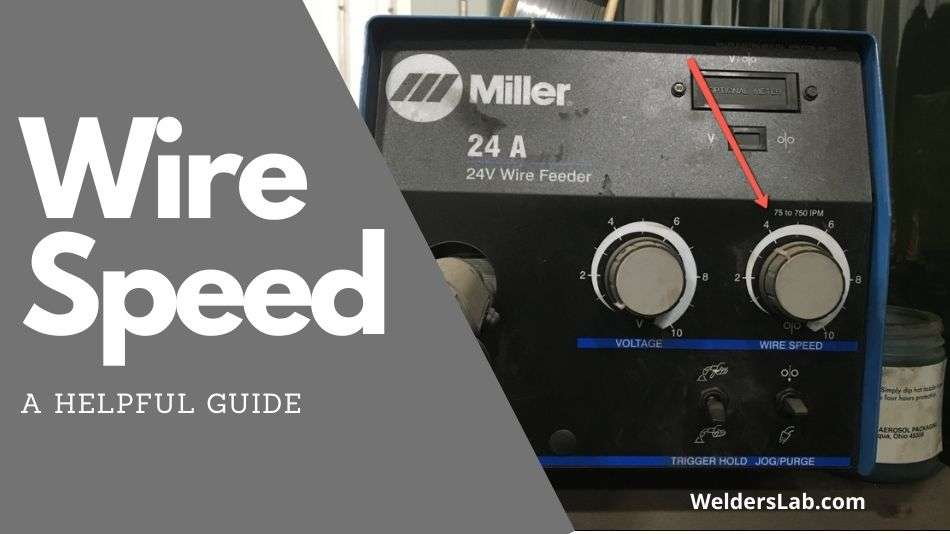
When it comes to welding I’ve found that the small things matter a lot to laying down a good bead. The right gas, the right amperage, the right voltage setting, and even the correct wire speed all factor into a quality weld. However, in this article, I’m going to go more in-depth as to what is the correct wire speed.
Wire-speed is measured in inches per minute (IPM). Welding a thinner metal with a smaller welding wire (.030) requires a lower wire speed (90 to 260 IPM). Welding thicker metals with a heavier welding wire (.045) will result in a higher wire speed ( 260 to 390 IPM). Factors such as the type of metal, metal thickness, wire size, and the type of weld determine your wire speed.
If you read this article on how to set wire speed on a MIG welder you will find a helpful guide to all the details you need. As will any welding project you will learn how much depends on voltage and wire thickness. You will also learn how different materials affect the process. It will talk about what happens when the wire speed is too slow and what happens when the wire speed is too fast.
But first, let us get into the details of how to set wire speed on a MIG welder.
How to set wire speed on a MIG welder
Wire speed for a MIG welder is measured in inches per minute (IPM) and are based on several factors.
- Metal thickness
- Type of Metal
- Wire Size
- Amperage
- Voltage
- And the Type of Welding you are doing.
Related Article: I won’t cover amperage and voltage in this article. You learn more about those settings in this related article.
Steel Wire Speed Settings
Below is a chart I put together for some recommended wire speed settings to consider if your welding mild steel.
Steel – Thickness | Wire Size | Short-Arc Transfer IPM | Spray Arc Transfer IPM |
22 gauge | .030 | 90 to 100 ipm | Not Recommended |
20 gauge | .030 .035 | 120 to 135 ipm 105 to 115 ipm | Not Recommended |
18 gauge | .030 .035 .045 | 150 to 175 ipm 140 to 160 ipm 70 ipm | Not Recommended |
16 gauge | .030 .035 .045 | 220 to 250 ipm 180 to 220 ipm 90 to 110 ipm | Not Recommended |
14 gauge | .030 .035 .045 | 250 to 340 ipm 240 – 260 ipm 120 to 130 ipm | Not Recommended |
1/8″ | .035 .045 | 280 to 300 ipm 140 to 150 ipm | 320 to 340 ipm 160 to 175 ipm |
3/16″ | .035 .045 | 320 to 340 ipm 160 to 175 ipm | 360 to 380 ipm 185 to 195 ipm |
1/4″ | .035 .045 | 360 to 380 ipm 185 to 195 ipm | 400 to 420 ipm 210 to 220 ipm |
5/16″ | .035 .045 | 400 to 420 ipm 210 to 220 ipm | 420 to 520 ipm 220 to 270 ipm |
3/8″ | .035 .045 | 420 to 520 ipm 220 to 270 ipm | Not Recommended 375 ipm |
1/2″ and up | .045 | Not Recommended | 390 ipm |
A few things I want to note here are that the thinner wire size like .030 will run at higher wire speed. However, when you weld thicker metals such as 3/8″ and 1/2″ the wire speed will increase.
Once you get to 1/8″ metal you start to introduce spray arc which runs at a higher IPM (Inches Per Minute) .
Aluminum Wire Speed Settings
Aluminum – Thickness | Wire Size | Short Arc IPM | Spray Arc IPM |
1/8″ | .035 3/64″ | Not Recommended | 350 – 400 IPM 240 – 270 IPM |
3/16″ | .035 3/64″ | Not Recommended | 425 – 450 IPM 300 – 325 IPM |
1/4″ | 3/64″ 1/16″ | Not Recommended | 350 – 375 IPM 170 – 185 IPM |
5/16″ | 3/64″ 1/16″ | Not Recommended | 400 – 425 IPM 200 – 210 IPM |
3/8″ | 3/64″ 1/16″ | Not Recommended | 450 – 480 IPM 220 – 230 IPM |
7/16″ | 1/16″ | Not Recommended | 240 – 270 IPM |
1/2′ | 1/16″ | Not Recommended | 290 – 300 IPM |
With a MIG welder spray is the way to go. Just like mild steel if you have a smaller metal thickness and a smaller wire size your wire speed will be higher.
If you use a thicker wire like 1/16″ you wire speed will decrease but as aluminum metal gets thicker the wire speed will increase.
Stainless Steel Wire Speed Settings
Stainless Steel – Thickness | Wire Size | Short Arc IPM | Spray Arc IPM |
18 gauge | .035 | 120 – 150 IPM | Not Recommended |
16 gauge | .035 | 180 – 205 IPM | Not Recommended |
14 gauge | .035 | 230 – 275 IPM | Not Recommended |
12 gauge | .035 | 300 – 325 IPM | Not Recommended |
3/16″ | .035 | 350 – 375 IPM | 400 – 425 IPM |
1/4″ | .035 | 400 – 425 IPM | 450 – 475 IPM |
5/16″ | .035 .045 | 450 – 475 IPM Not Recommended | Not Recommended 250 – 300 IPM |
3/8″ | 1/16″ | Not Recommended | 140 – 170 IPM |
7/16″ | 1/16″ | Not Recommended | 170 – 200 IPM |
1/2″ | 1/16″ | Not Recommended | 200 – 230 IPM |
If you’re using a 304 grade stainless steel these are the typical wire speed settings you can use to dial in your welder.
One final note here, if you are using a slightly thinner wire such as .045 wire instead of 1/16″ that might be recommended then you’ll have to run a slightly higher wire speed and vise versa.
What happens if the wire speed is too slow
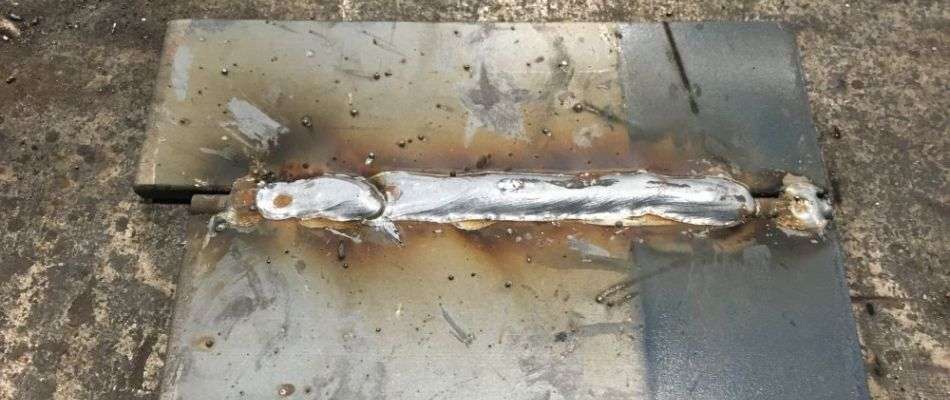
A slower wire speed will produce a narrow weld. This could affect the uniformity and create cracks or discoloration in the weld. It may also influence the control you have over the welding process resulting in weakness or fragility of the final weld. That is why knowing how to set wire speed on a MIG welder is so important.
May also produce a weld that is too tall. Even if the penetration is okay, a tall weld could leave cracks down the center of the bead, discoloration, and lack of uniformity. You may have to increase the voltage or adjust the speed a little to reduce the height of the weld.
Slowing down your wire speed will increase penetration of the weld. Be able to adjust the wire speed to accommodate the welding project you are working on is an important part of welding. Make sure you are within the correct parameters with relation to the voltage and thickness of the materials you are using.
A reduction in travel speed could also affect the integrity of the weld. Faster travel speed will reduce penetration because it causes the heat to drop. Of course, that is if you are staying within an acceptable range. Slowing down too much will reduce your control because the pool will get out ahead of you. Too fast and you may experience burn through.
The cosmetic appearance of your weld could be jeopardized by too slow of wire speed. The resulting spatter, loss of pool control, and penetration variables may produce a less aesthetically pleasing weld. Discoloration or cracks in the bead will need to be repaired if you are not keeping a vigilant watch over your speed.
What Happens if You Set the Wire Speed to Fast?
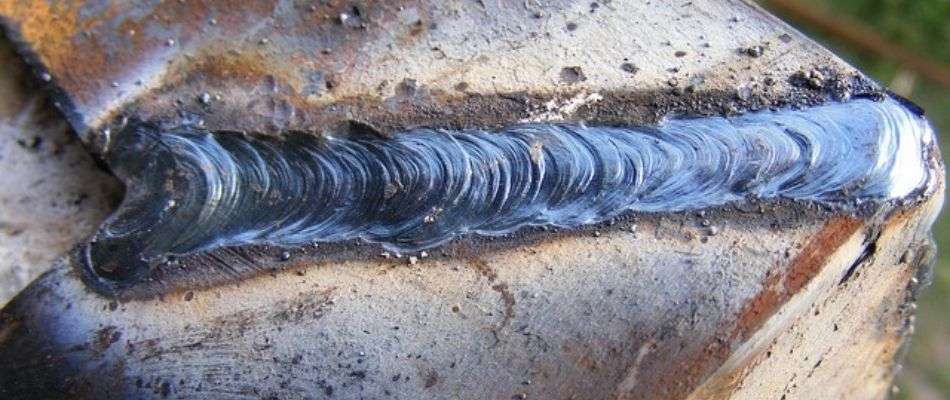
The wire speed controls the current. If the wire speed is too fast it increases the current. If the current is too high you can lose the integrity of the weld. It could result in burn through on thinner materials.
It might also create a fatter weld. This could increase spatter which is a safety hazard as well as a cosmetic risk to your final product. Loss of control and cracking the bead could also result. Managing the speed in relation to the voltage will reduce the risk.
If your wire speed is too fast it will increase the travel speed with can also create a bad weld. You want to make sure the wire’s speed is within the acceptable variable range based on the materials you are using. This range is based on your calculations at the beginning of your welding project.
If your wire speed is too fast it could become expensive. Not only will you be racing to stay in control, but you will also be wasting a lot of material.
Going too fast can eat through your wire and leave you running low at the end of your project. If the project goes incomplete because you blew through your wire, you will have to purchase more.
Once more we see how penetration is affected by wire speed. The more consistently you can maintain wire speed, the more consistent your penetration will be throughout. Penetration is more than just an aesthetic concern. It directly affects the integrity and strength of the weld.
Stay on target and maintain wire-speed within the allotted range and you will be able to maintain a consistent penetration. There may be times when less penetration is required, but the majority of welding projects need good, steady penetration.
4 Quick Tips Setting Your Welders Wire Speed
#1 The Wrong Wire Speed Makes it Hard to Weld
Wire-speed might be the most important setting on your MIG welder. Even though it is possible to weld neatly with an incorrect power setting. It may be that the penetration is a little off.
It will still be possible to get a neat weld. But if your wire speed is incorrect you will have a really difficult time welding. That’s why you want to make sure your calculations are in order and that you maintain a strong constant that stays within an approved range of wire speed.
If your wire speed is too slow it can cause a lot of trouble. If it’s too fast it may also deliver results that are not where you want them to be.
Between penetration, variable speeds, voltage, bead integrity, splatter, and other safety and cosmetic issues it is important to remember that a lot of your welding will rely on wire speed more than any one thing.
#2 Properly Set Wire Speed Will Save You Money
Keeping a healthy and vigilant watch on wire speed will save you a great deal of time and money. But remember, there is no set speed on which you can set your machine and expect it to perform well.
Welding is an art just as much as it is a science. Things change and there is a constant need for readjustment and resetting. Great welders are aware of that and compensate accordingly.
#3 What Your Welding Matters
Always remember to base your wire speed on what you are welding. The calculations used to determine accurate wire speed will help you do that.
Recall how important the thickness of the material is to your welding project. If the wrong speed is in place and your current becomes too high you could run the risk of burning through a thinner metal.
Be extra careful and make sure you are paying attention.
#4 Don’t Let the Puddle Get Ahead of You
Do not let the pool get out ahead of you and do not let it fall behind either. As was stated earlier, welding is an art.
Your canvas is steel. Your paint is molten hot. Your eyes and hands are the brushes that make or break the bead. Take extra care to calculate accurately, understand the materials you are using, and keep a steady, attentive eye.
If you do that you will have a completed project that is finished in no time.