How to Prevent Cracks in Welding – Complete Guide
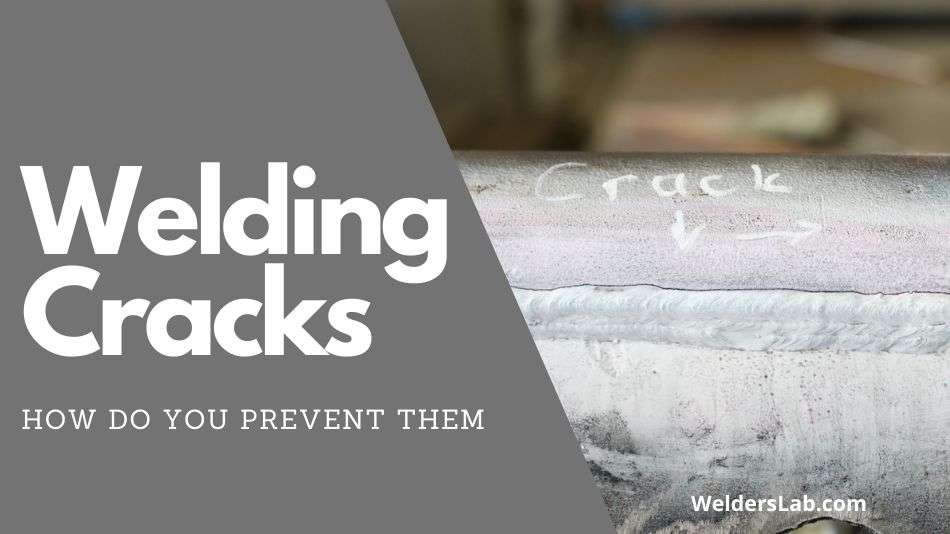
Have you ever taken a moment to really look at your welds? I mean really look at your welds. Do you notice any imperfections in your weld? Porosity, undercut, to little gas, not enough wire speed, low voltage. These things can all lead to cracks in your weld if you’re not careful.
Welding cracks happen for a lot of different reasons from fatigue, heavy load weights, bending and twisting, old age, and hot and cold expansion, and contraction of the weld. To fix a cracked weld you will need to grind out the weld down to the root of the crack and weld a new solid bead in place to strengthen the cracked area.
In this guide, we will talk about how to prevent cracks in welding. We will cover topics like how to fix weld cracks and what causes weld cracks. My goal is that you will understand the concept of weld cracks and also be comfortable with trying to fix and prevent them in your welding.
Keep reading to learn how to prevent cracks in welding and more.
How to Prevent Cracks in Welding: A Complete Guide
Cracks are another welding deficiency that we must learn to handle and prevent, if possible.
We certainly don’t want a cracked weld to be at our own fault but we need to know how to handle the situation if we come across it, and if we’re the cause of it.
What is a Cracked Weld? Identifying What it is and What Causes It
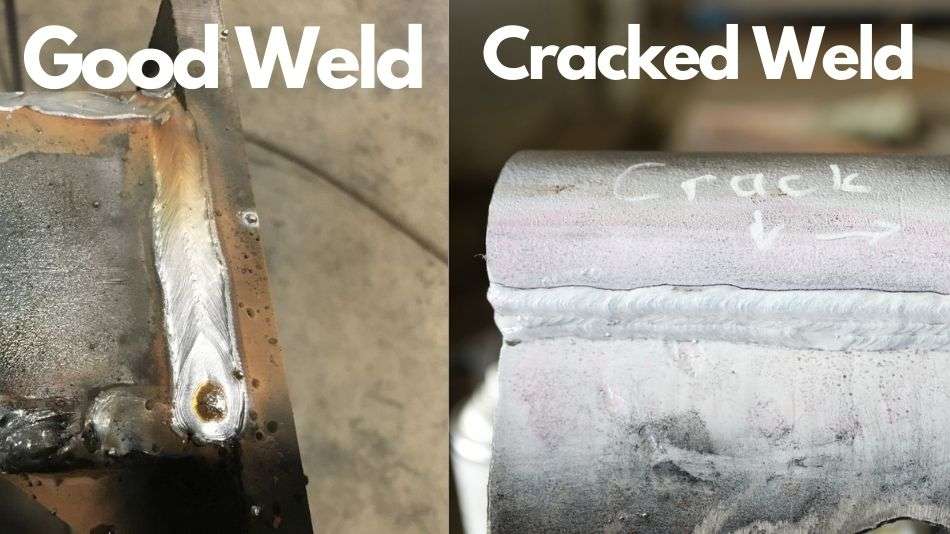
There are several different types of cracks in welding. Here are a few of the most common types.
- Longitudinal crack
- Crater crack
- Underbead crack or Lamellar tear
- Toe crack
- Root crack
- Transverse crack
- Fusion-line crack
The top 3 crack types on this list are the most common welding cracks that you are going to come across or see. The others tend to happen over time. They can be the result of a poor weld but they can also be the result of wear, time, and excess pressure.
A cracked weld is one of the most severe welding defects there is, regardless of the type of crack. A crack should never be left uncorrected. It is possible to fix cracks but, ultimately, you should try to prevent the crack from happening so you don’t have to redo it.
Remember that cracks don’t always happen right away. Many cracks show up over time, particularly for structural or load-bearing pieces. Here are some alternative crack causes that we may have no control over.
- Fatigue and tensile loads
- Bending or twisting
- Flexing of metal
- Age
- Heavy loads
- Hot or cold expansion or contraction
Ultimately, a crack is caused when the stresses the material is facing exceed the strength of the metal used in the weld or in the base metal. Sometimes, the weakness is a combination of the weld metal and base metal. Once a crack occurs, it can get worse from there as it becomes a focal point for the stressors.
There are also some welder technique issues that could lead to cracks. Here are those.
- Metal adherence
- Incomplete fusion
- Bead contouring sizes
- Improper weld sizes
- Poor technique
- Incorrect travel speed
- Electrode angling and control
- Improper settings
- Carelessness
How to Prevent Cracks in Welding
If you’re having trouble with a particular weld cracking don’t get frustrated. Working with new techniques or new products can often take practice and it’s very common to find cracks in your welds as you do this.
If you’re testing new base metals or filler materials, don’t be surprised if you find yourself facing cracks.
I’ve said it before but let me say it over and over again, welding requires practice and skill-building. Cracks most likely are going to happen. You will improve your processes and techniques as you build your skills but even an experienced welder may run into cracked weld issues. Don’t sweat it, just keep working and using the tips you learn to prevent it from happening again.
It’s best if you are able to prevent a crack from ever happening, just know that if a crack happens after the fact, you might be able to fix it.
The best things you can do to prevent cracks in your weld are to choose your filler materials wisely. The way that you store and handle your filler materials also make a difference. If you don’t handle your filler materials appropriately, it could compromise their quality when you use them.
Don’t try to spread your materials too thin and don’t try to rush through your processes. Take the time, from start to finish, to do it right and you’re much more likely to be able to prevent cracks in your weld. That means to prepare and clean your area like you’re supposed to.
Check your settings and your materials and be sure you’re using the right things for the job. Don’t over-weld and don’t under-weld. Use a gentle and consistent technique to perfect your weld. Remember, the more you practice at perfecting the weld, the better your weld will become.
How to Fix a Cracked Weld
Despite all of our preparation, training, and planning, we may still find an insufferable crack in our weld or in a completed weld that needs repaired. While it’s much better to try to prevent the weld in the first place, cracks do still happen.
There are certain codes that may not allow you to remove the weld and prepare the piece with a fresh weld. It’s all very subjective. However, in terms of how to fix weld cracks, there are a couple of options. None of them are simple and sometimes you simply can’t fix it with these processes, which is why we recommend prevention first.
You might be able to gouge out the cracked area or the cracked weld, grind and prepare the surface and repair that section of the weld. Most of the time, repair will require grinding down the entire welded area and starting over with a fresh weld.
You are less likely to see cracks if you use the proper equipment. MIG and TIG welders tend to work better where a crack is possible but it doesn’t necessarily mean they are the best option every single time, it totally depends on the job.
Be sure you are using the right supplies, the right filler materials, the proper gas levels, and any other accessories. More importantly, be sure to prepare your surface and take your time to try to do it right. Rushing through the process will not save you time if you have to start over.
FAQ Section
Why Do Stainless Steel Welds Crack?
Stainless steel tends to be established in a corrosive environment. The stress that and the environment that stainless steel is in are the most common reasons that stainless steel cracks.
Another common issue with stainless steel is your filler metal is a different type of metal and therefore may not adhere as solidly as you like. Choose your filler metal wisely.
Why Do Aluminum Welds Crack?
Aluminum welding is more likely to acquire cracks for very similar reasons to stainless steel. You’re using a filler material that is not aluminum and therefore melding two different kinds of metal.
You must choose your filler metal wisely to insure it will adhere properly and you must be sure you use enough filler material as well.
For aluminum, it’s when the item is forced to bear weight or shrinkage occurs that the cracks are most likely to occur. It is very important that you are careful with your procedures to get the best weld. Aluminum is a challenging metal to work with.
Conclusion
Welding cracks are an unfortunate part of the welding life. Seasoned welders and beginning welders alike will most likely face them at some point in your career. When you face a welding crack, it might be because you’re called in to make repairs and you find someone else’s work.
Do your best to be proactive and try to prevent welding cracks from happening on your watch. Unfortunately, a crack is the worst kind of deficiency or blemish and often much more challenging to correct than say porosity or undercut spaces.
Keep practicing, keep working hard to improve your skills. When you’re in the field, stop and take the time to prepare your surfaces as well as slowing down through the process to do the best you can.