Do You Push or Pull a MIG Welder – Which is Better
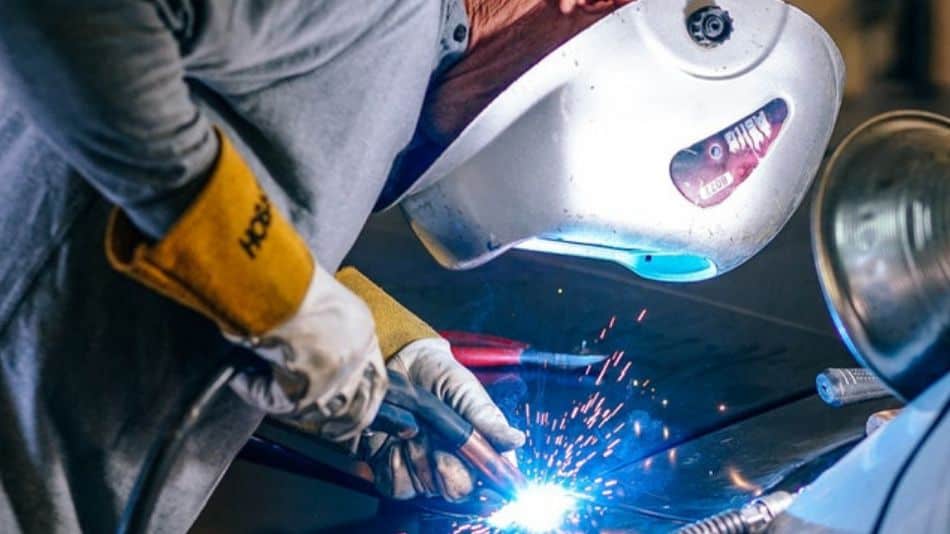
When I was first starting out welding on a MIG welder I often wondered whether it was better to push or pull a weld and in this article I’m going to share my thoughts around this.
Do you push or pull a MIG welder? Pushing a weld with a MIG welder tends to give a slightly stronger weld because it tends to spread out more and fuse with more of the base metal. Pushing a weld also tends to give a more aesthetically pleasing look to the weld. Pulling the weld may give deeper penetration but typically has a more rounded look and doesn’t look as aesthetically pleasing.
I also should mention that just because one way is better than the other you should know that this doesn’t necessarily mean that you can’t do both and in
To Push or To Pull Your Weld
When it comes to welding with a MIG welder one of the oldest debates is whether you should pull your weld or push your weld.
So what does it really mean to push or pull your weld. If you are pushing your weld then this means your weld gun would be behind the weld as you push the puddle along and create the bead.
To pull a weld means that your weld gun would be in front of the weld and you would be dragging the puddle
So here are a few advantages and disadvantages to pushing or pulling your welds.
Pulling Your Weld – Advantages and Disadvantages
- Advantage – Pulling your weld will give you deeper penetration into the base metal.
- Disadvantage – It has a more rounded look and isn’t as smooth of a weld.
- Advantage – It will be a
stonger weld and hold bothpeices of base metal together. - Disadvantage – The weld will not be as
astheticly pleaseing . Basically, it won’t look as nice and may even require grinding if it needs to be smoothed.
Pushing Your Weld – Advantages and Disadvantages
- Advantage – By pushing your weld you’ll create flatter wider and much smoother puddle which will tie into more of the base metal.
- Disadvantage – The weld won’t penetrate as deep into the base metal and not be as strong of a weld.
- Advantage – The weld will be much more aesthetically pleasing to the eye for those who want a smooth flat looking weld.
- Disadvantage – If the weld would happen to be in a high stress situation it may not hold up as well.
One last thing I want to say is that you should not do one over the other. Each type of weld has its place and if done properly both can be used as a tool in your arsenal as a welder.
So don’t think that if everyone tells you that pulling a weld is the only way or pushing is the only way to weld. In fact I have done both types of welds in the same pass.
I’ll explain that more in the article.
When to Push and Pull a Weld
So now that you know the advantages and disadvantages of both push and pulling your weld you might be
To start, not every situation will be the ideal situation for pushing or pulling your weld.
If you’re working in a tight space that doesn’t allow the nozzle of your welding gun to fit in a certain spot you may only have one choice as to whether you should push or pull your weld.
For example, if you have to weld a frame on a motorcycle your weld nozzle may have a hard time fitting in this position and it may cause you to push and pull your welds.
Examples of When to Push a Weld
One good example of pushing a weld would be when you do vertical down weld. This is a weld where you are welding straight down.
You can pull this weld down but often times I’ve done this weld pushing it down to get a smoother flatter look. Does the weld have a lot of penetration?
No, but that weld is more about the look than strength in this case. As you can see in the picture to the right.
Examples of When to Pull Your Weld
An example of a pull weld that I might do is welding an I beam for a bridge together. If I were able to gap the I beam an eighth of an inch apart and pull a weld over the gap it would give a much higher penetration.
In this case since I am welding something that has to be structurally sound you will want a higher penetration to give you the most strength.
Examples of When to Do Both
However their are times when you’ll want to do both a push and a pull in the same weld bead. I do this a lot when I’m welding a piece of half inch rod to a flat.
As I show in the image to the right I usually do this weld starting on one side of the rod doing one pass pushing it and then pulling the weld back across.
The point here is to be creative with the options you have as a welder. If you’re looking for that clean weld then push it but if strength is what you’re looking for then pull your weld.
When Should You NOT Push Your Weld
One thing I do want to add about pushing and pulling your welds is when it comes to using flux core wire instead of a shiellding gas.
With flux core, you’ll use a tubular wire that has flux at the core of it. When that flux burns it creates a shielding gas that also produces slag that will sit on top of your weld.
Related Article: If you want to learn more about how to use a MIG welder without gas read this article.
When it comes to this type of welding you’ll want to pull your welds as much as possible. The reason for this is because if you push the weld you will trap the slag in the weld which could weaken the bead.
It may also produce pin holes and not give a great aesthetic look and feel.
Testing Your Welds
In the
So how do you do this..
Step 1: Tack up a T Joint – This is a weld that would a piece of flat metal sitting horizontally and another sitting in the middle vertically. Basically, it would look like an upside down T.
Step 2: Weld One Side Pushing and the Other Pulling Your Weld. Doing this will give you a side by side comparison of the aesthetics of the welds.
Step 3: Cut the T Joint in Half. Use a hand grinder or a band saw and cut the joint in half. Doing this will show you how deep the weld has penetrated.
Step 4: Heat the End You Cut Off. Doing this will give a more defined look at how deep the weld penetrated. To do this you can use a small hand torch.
Step 5: Review What You’ve Welded. You should see a noticeable difference in which weld was pulled and which was pushed.
If you do this test you should see something that looks a little like the weld below this.
Related Questions
#1 Do you push or pull a stick welder? With stick
#2 Do you push or pull a TIG welder? With a TIG welder, you’ll likely be pushing your weld since you will be heating the metal with a torch gun that will create a puddle and usually add a filler rod as you lay the bead.
#3 Do you push or pull MIG welding aluminum? In this case, you’ll want to weld aluminum by pushing it will give it a more smoother flatter look and maintain the shielding gas in the best position.
When it comes down to it knowing when to push and when to push a weld can be great to know and allow you to get better results.
So what do you prefer, do like to push your welds or do you like to pull them?