10 Advantages and Disadvantages of MIG Welding
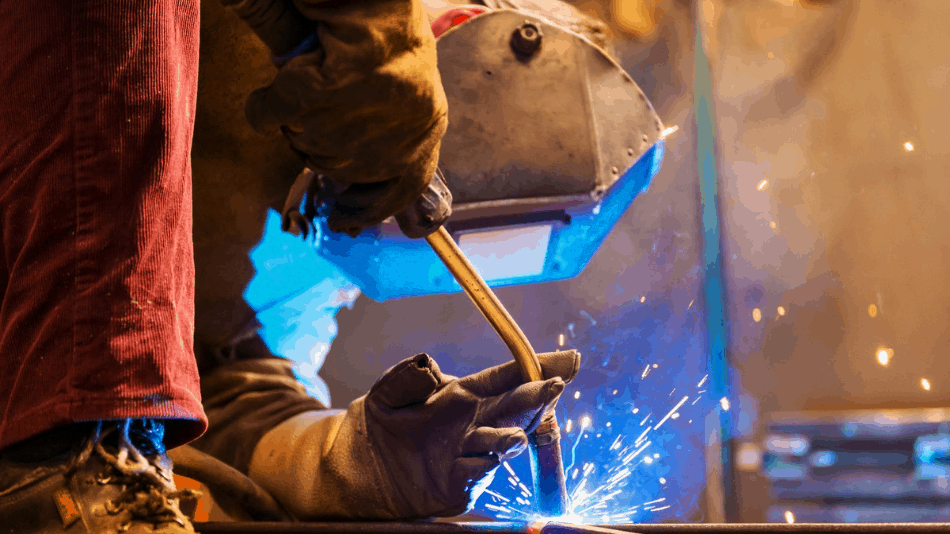
Several years ago when I was first getting started with my welding business I often wondered if MIG welding was the right option for me. After all with other options like Stick and TIG available I felt it was worth my time to see which was right for me and what the advantages and disadvantages are.
What are the advantages and disadvantages of MIG welding? Below are ten advantages and disadvantages I found while using my MIG welder.
- Speed
- Not as portable
- Better looking welds
- Can lose gas while welding
- Can optimize weld settings
- Requires less cleaning
- Easier to control
- Requires changing consumables
- Power Options
- Need a clean welding surface
So if you’re just getting started and looking for your first welding and you’re looking at a MIG welder then you may want to consider all of these advantages and disadvantages before you buy one. In this article, I’m going to go into more detail and talk about each and how it will affect your decision.
#1 Speed: Advantage
The first advantage of MIG welding is the speed at which you can operate your welder.
I’ve been welding with a MIG welder for well over 20 years now and when I go into my shop every more there is something to be said for being able to walk into work and be able to just flip your machine on, open your gas, and start welding.
With a stick welder you can turn it on right away just like a wire welder but the downside comes when you have to constantly be interchanging electrodes which will cost you time.
TIG welding, on the other hand, is slow by nature. It requires you to manage the filler rod, the welding wand, and a foot pedal that controls the temperature of the weld.
Now obviously with a wire welder, you will have to change empty tanks of gas and replace empty spools of wire but in the end, a MIG welder is an option for fabrication shops and production-based businesses because MIG is just faster in the end.
When you look at any major business from car companies to your local fab shop like mine they almost all use MIG welder for the majority of their work because they are way faster than any of the other types of welding.
#2 Portability: Disadvantage
Now there is a big disadvantage to a MIG welder, and the first is that a wire welder is not a very portable machine. There are several reasons for this:
#1 Requires Gas – the first is that a MIG welder will typically require you to use a shielding gas in order to protect the weld.
Related Article: I wrote a whole article on which shielding gas to use for your MIG welder here.
A normal tank of welding gas can weigh over a hundred pounds and can be very awkward to carry. For most MIG welders it will require you to use a cart to carry the machine and the gas.
#2 Requires a Roll of Wire – A MIG welder will also require you to use a roll of wire as well. The wire can be in anything from a 10-pound spool to 60-pound spools and up.
Now there is a way to combine your wire and shielding gas and that is to use a flux-core wire. This is a wire that contains a center core of flux when burned will provide a layer of protection much like a shielding gas.
I’ve personally used flux in the past and found it doesn’t work as shielding gas itself but if you are looking for a more portable option this could be the perfect solution.
#3 Can Be Heavy – Finally, the last issue is that I sort of mentioned the first problem is that MIG welders are heavy. Even a lighter welder such as the Hobart 500599 Handler 140 will weigh 65 pounds.
Combine that with the awkwardness of the machine and lugging even just this welder around is a good way to throw your back out of wack.
In the end, certain MIG welders are designed to be portable but they are still limited by their weight and features.
#3 More Aesthetically Pleasing: Advantage
The next advantage of going with a MIG welder is that they will have a cleaner weld. When you look at all the different types of welding out there from stick welding, MIG, and TIG, a MIG will produce a fairly clean weld.
A TIG weld will produce probably the cleanest weld of them all. It will produce very little spatter. This is because a TIG uses more of a spray arc rather than popping while it welds. In fact, a TIG welder will usually hum while it welds which is very quiet.
A Stick weld, on the other hand, will usually have a fairly dirty look to it. This is because of the flux on the welding rod. Also with a stick welder, you will have to remove the slag after you lay down a bead.
With a MIG welder, it can produce spatter as you are welding but you won’t have to chip slag off. In fact, I’ve found that doing a spray arc method when trying to weld hot and penetrate deeply with your welds gives probably the cleanest weld with very little spatter.
Finally, I should mention with a MIG welder that you don’t want to forget to turn shielding gas on as this will make a terrible-looking weld that will not penetrate very well and does not look good at all. This weld can break easily if no gas is used while welding.
In the end, a MIG weld has a great look as long as you have your machine set up properly. More on that later in the article.
#4 Loss of Gas: Disadvantage
The next disadvantage of MIG welding is that it needs a shielding gas to protect the weld. The reason this is a disadvantage is that depending on the situation as it can be pushed away from the weld if you would happen to have too much wind.
For example, if you are working outdoors and you are welding a piece of farm equipment and it would be windy out it would be hard to lay a good bead.
You would see a lot of porosity once the gas is removed looking like a bunch of pinholes in your weld. As a result, the weld won’t penetrate and could break easily.
However, there are a couple of ways to get around this issue.
#1 Cover Your Weld. Your first option is to cover the weld with a welders blanket. This is a special blanket you can use to put around your weld to help block the wind.
It can also be used to cover things so they don’t get burned or cause a fire. I’ve even seen people use it to cover them and the weld to reduce gas loss issues. So it can be used for multiple purposes if needed.
#2 Fluxcore Wire. The second option is to use flux core wire which does not require you to use a shielding gas. However, if there is too much wind even flux-core wire won’t do any good.
In the end, there are viable options for dealing with this issue even if you decide to use a MIG welder.
#5 Weld Settings: Advantage
Another advantage to MIG welders is that they give you various ways to control the setting of your welder to manipulate your welds to do certain things.
For example, if I want to do more of a flatter weld I could turn down my wire speed which would produce more of a spray arc creating a flatter weld. Or maybe I need to weld a thinner piece of metal, with a MIG welder I could turn down the amperage to cut down my heat.
If you would have something like a stick welder you won’t have as much control allowing you to manipulate the welds in certain ways. This is where a MIG welder shines.
So here are two main ways you can control your welder.
#1 Wire Speed. The first way to control your weld is to increase or decrease your wire speed. A faster wire speed will create a taller weld with more spatter and less penetration. A slower wire speed will create a flatter weld with less spatter and deeper penetration.
#2 Amperage (Heat). The other main way to control your welds is to increase and decrease your average. With a lower amperage setting, it will allow you to weld thinner materials and not penetrate as deeply, while a higher amperage setting will penetrate deeper and weld thicker metals.
#6 Cleaning: Disadvantage
The next disadvantage is cleaning. Now I’m not talking about cleaning your welds but rather the welder itself. With MIG welders at some point, the nozzle is going to plug up with a spatter. It’s almost impossible to prevent this.
For most MIG welders if you neglect this you’ll have issues such as the nozzle plugging up, the weld tip filling up with dirt, and even the welding liner seizing up from weld dust.
So how can you prevent this?
#1 Clean things regularly. The first thing you want to do is clean your welder often. I like to use welding plyers for this because it works great for cleaning the nozzle and removing the consumables when they get hot.
#2 Use Tip Dip. Second, consider using tip dip once you’ve cleaned your weld nozzle. This will help prevent spatter build-up.
#3 Replace Consumables. Finally, when consumables wear out then replace them with new ones. This would include your weld nozzle, tips, diffusers, and liners.
#7 Great for Production: Advantage
The fourth advantage to a MIG welder is that it can be a whole lot easier to control and operate overall in a production setting. If you’ve ever used a MIG welder you’ll understand when I say that these welders just work.
As I mentioned at the beginning of the article I can set my welder up and I can literally just turn it on and start welding at any point.
Now you can do that to a degree with a stick and TIG welders but MIG just works and you don’t have to do a lot of extra work to keep it going.
So if you are running a small business or hobby shop like me then MIG is the only type of welder you should buy.
#8 Consumables: Disadvantage
In number eight I want to talk about cost when it comes to MIG welding replacing consumables. Consumable as the parts on your welder that get replaced regularly.
MIG welders are designed like this so you can replace smaller parts instead of the whole machine. Typical consumables consist of:
- Welding Tips
- Welding Nozzles
- Weld Liners
These three parts are the most commonly replaced and used. However, the big disadvantage with them is that they can cost a lot over time, especially if you’re running a lot of production.
For example, I recently switch suppliers with welding tips. My original supplier was charging me $1.36 per weld tip. With 8 welders running and each welder going through at least 3 tips per week, you can see the problem.
So I switch to an online retailer and cut the cost down to $.64 per weld tip. Now I can buy two weld tips for everyone that I got from the old supplier.
When it comes down to it you will likely have more cost in consumables with MIG welders but if you shop around for the deals you’ll likely save a bit of money as I have.
#9 Power: Advantage
As I mentioned earlier in this article one of the great assets of a MIG welder is that it gives you a lot of control over your power but what’s also nice about these types of welders is that you can run them with various types of power.
What I’m talking about here is that a MIG welder can run on anything from a 110v outlet in your house, 220v in your garage, to full-on 3 phase power as I have in my shop.
So let’s cover each.
#1 110v Power. With a 110v welder like the Hobart Hander 140, you can run this on literally any outlet in your hose with a 20 amp breaker. You can check out my complete article on welder amperage here. These welders are meant for portability and home hobbyist as they typically have lower duty cycles and limited power.
#2 220v Power. The next step up is a 220v welder. I have a few of these in my shop. They have more power behind them and work great for those doing a lot more work with them. The downside is that they can cost more to run.
#3 Three-Phase Power. This is what most typical weld shops like mine use. Three-phase will supply more power and typically runs less amperage which will cut down the cost of electricity.
#10 Needs to Be Clean: Disadvantage
The final disadvantage to using a MIG welder is that your surface area needs to be clean before you start welding. This is also true with other welders like a TIG welder.
However, a stick welder will weld on almost any kind of surface such as a piece of old rusty farm machinery. A wire welder doesn’t do this so well.
To solve this issue there are a few things you can do to make sure you get a clean weld.
#1 Wipe off the dirt. If you have oil or grease on your metal wipe it off with a rag. You can also use a cleaner or paint thinner to clean off the oil. Just be sure to keep all flammable chemicals away from the area before starting to weld.
#2 Grind. If you have paint, rust, or something similar on the metal then you may need to use a grinder or a brush wheel to remove the paint from the surface.
Is a MIG Welder Right For You?
As I wrap up this article you may be wondering about all the advantages and disadvantages with MIG welders which is right for you so here are a few tips to help you out.
- First, if you are running production for a small business or a hobby business out of your garage then a MIG welder is the answer for you.
- If you’re looking for control over welds to do a variety of things with it then MIG is the way to go.
- If you just want something that works when you need it then MIG is the way to go.
So is MIG welding right for you? Let me know in the comments section below.
I would love to hear your thought and also what advantages and disadvantages do you have with MIG welder that I didn’t mention in this article. Feel free to share them below.