When Is It Too Cold to Weld?
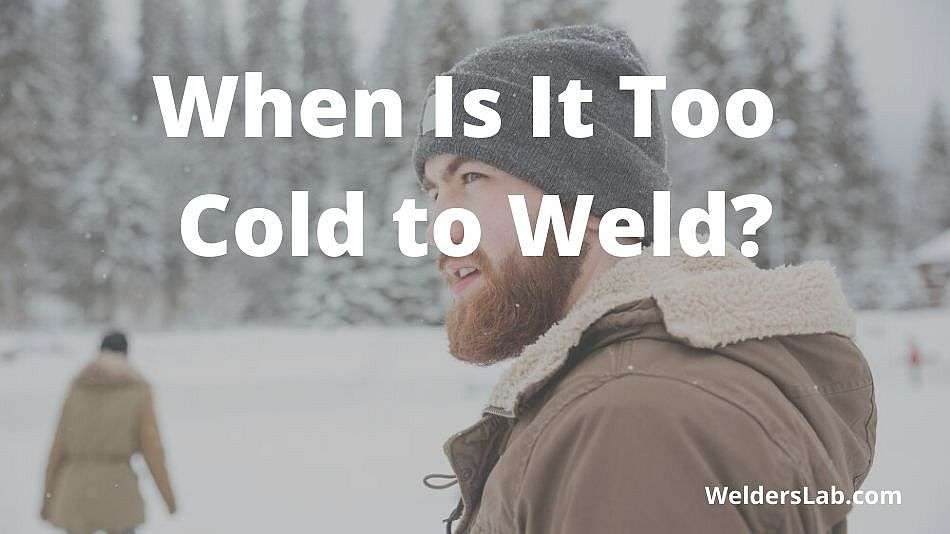
A lot of professional welders have to work every month of the year – even the cold ones. Your clients rely on you to get the job done no matter how cold it is.
But, when is it too cold to weld? Metal below freezing temperatures can cause the weld not to penetrate the base metal. To fix this you can either bring the metal into a warmer place and bring it up to room temperature or by preheating the metal with a rosebud torch to bring the metal to a higher temperature.
For beginners, there is a definitive answer. Welding takes skill, especially for quality jobs. The more patience you have, and the better your technique, the more easily you can handle welding in difficult circumstances.
This means that it is entirely possible that it might be too cold for you to weld specific projects at some point. How do you know what that point is? There are a lot of different things to consider.
Let’s look at some now.
When is it too cold to weld? What is the coldest you can MIG weld?
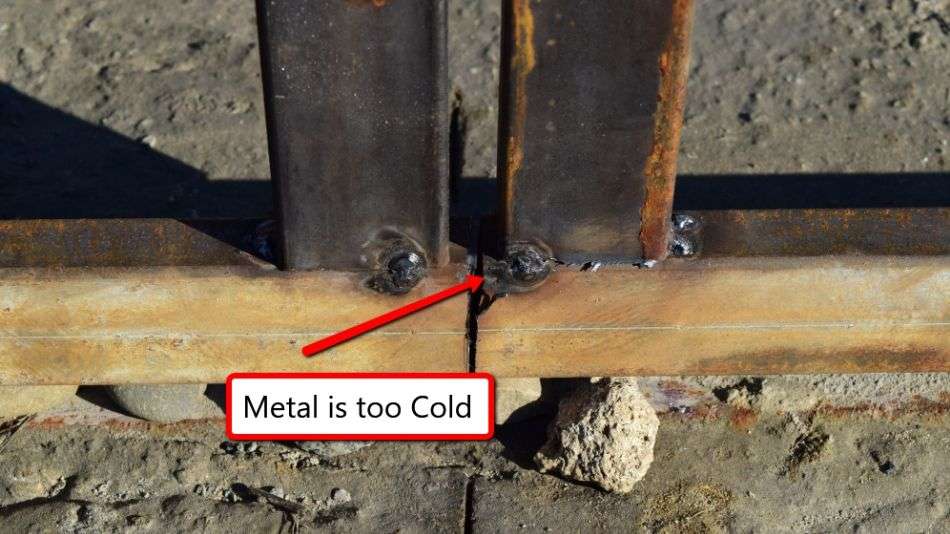
This answer varies based on your welding technique and your work. For example, when you are working on a bridge, there are codes enacted that prevent you from welding if the temperature falls below 0 Degrees Fahrenheit.
For piping and work on pressure vessels, you can’t work if the temperature falls below freezing, which is 32 degrees Fahrenheit.
ASME welding codes are even kinder to welders, preventing anyone from working if temperatures fall below 50 degrees Fahrenheit.
For smaller, personal projects or works of art that won’t need to hold up under stress, these codes are a little more lenient and it comes down to your personal DITY preference. Just remember to take precautions.
Can you weld in cold weather?
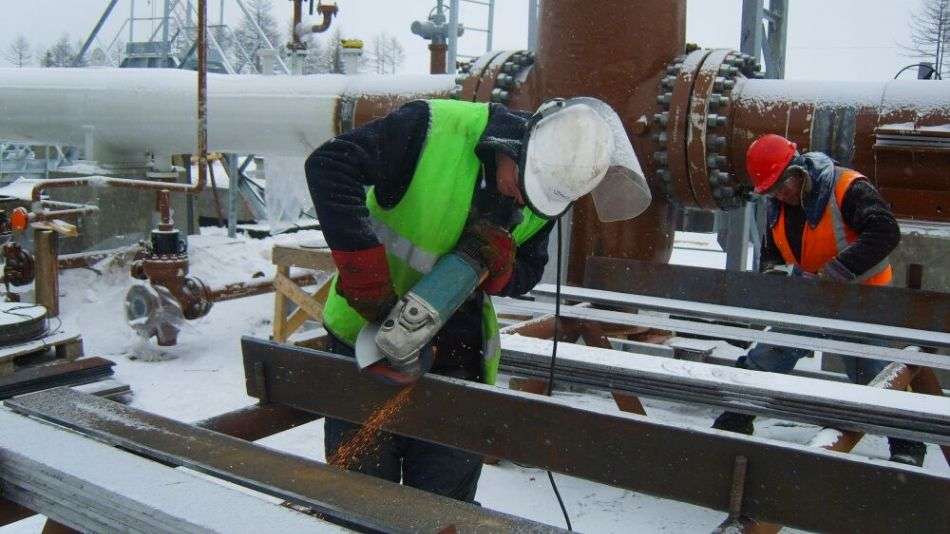
Larger welding projects are rarely held up by cold weather. A lot of very skilled and talented welders are determined to press through cold conditions and ensure quality welds. This means that you can weld in the cold weather. It will just take a lot more skill and perseverance.
A lot of cold weather welding was born out of necessity. There was a job that needed to be handled very quickly, and no one else had the skill or willingness to do it, so welders needed to just go handle it if they wanted to keep their jobs.
The necessity also birthed creativity. A lot of these cold-weather welders came up with ingenious ways to keep their welds protected.
Whether they were out working oil rigs or in shops or fields, they have found several different ways to ameliorate the effects of cold weather welding.
What happens to your weld if it is too cold?
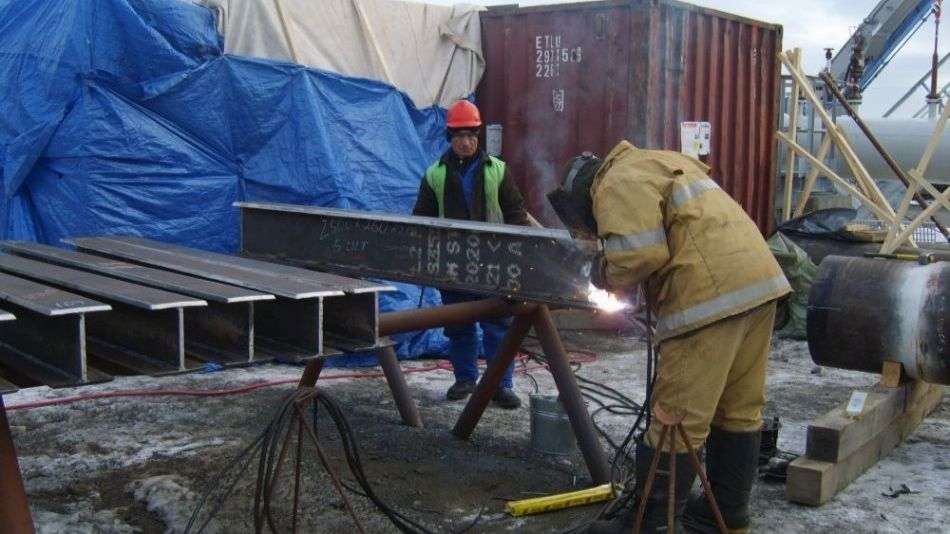
If your weld is too cold, then it won’t achieve proper penetration. This will lead to a failure of the weld, causing cracks, breaking, and the inability to hold up against stress tests.
In the cold weather, the base metal ends up becoming a heat sink. The result is that it will suck the heat right out of your weld as soon as you stop applying it.
This is a bad situation because if your weld gets cold too quickly after you apply it, then it will end up cracking.
What can you do to warm up your metal if it’s too cold?
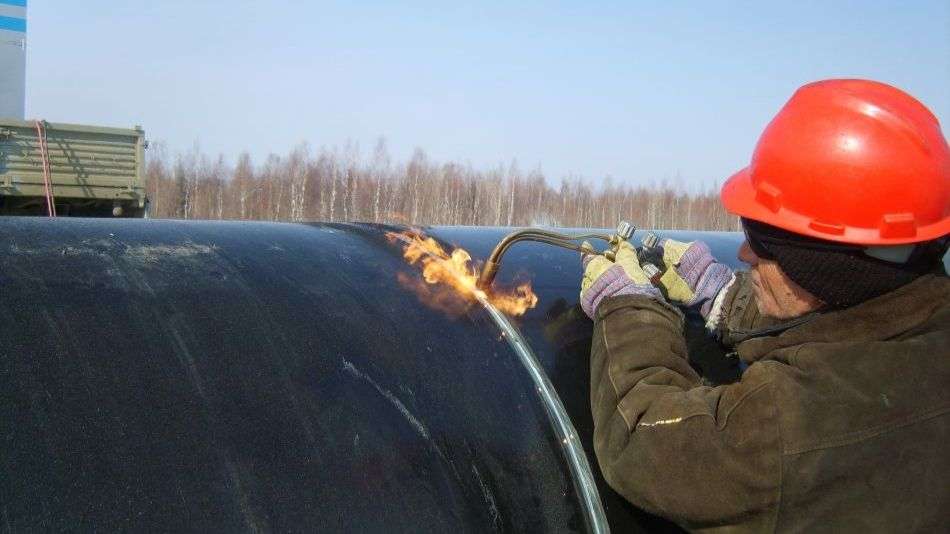
If you’re welding in the cold, then you can preheat your base metal.
It is a vital step to cold weather welding that will ensure proper penetration, so you don’t have to worry about failures due to a lack of penetration.
Your first pass needs to achieve full penetration, especially if the weld will be bearing a lot of stress.
Preheat
To avoid issues with penetration and cracking, you need to make sure that your base metal doesn’t become a heat sink. This means you will need to preheat it so it won’t cool too quickly after you weld.
If you are welding metal that is over 3/8 of an inch thick, you will want to make sure it gets preheated to at least 50 degrees Fahrenheit using a propane or oxy-acetylene torch before beginning.
Bring It Inside
During the welding process, if you notice that your weld is starting to cool too quickly again because it has gotten too cold, you can bring it inside.
This will keep it protected. Once it has warmed, you can return to welding.
Maintenance Tips for Cold Weather Welding
There are a few things you can do to improve the likelihood of success when you are welding in the cold weather.
Let’s take a look at some of the ways that have come about to keep your welds protected.
Gear Up
First, you need to take care of your personal safety. You still need all of your regular safety equipment, like earmuffs and darkening helmets.
You also need to find a way to protect yourself from the other elements – namely, the cold, wind, snow, and whatever other circumstances are leading to such cold weather.
Keep in mind that you need to use the specialized gear. Unlike most cold-weather wardrobes, you can’t just bundle up and go outside.
Welding requires a great deal of dexterity, and the more layers you add for cold protection, the less dexterity you usually see… especially with bulky, padded coats and mittens.
Use thinner materials, like thermal underwear beneath your welding gear to stay warm.
You also need to make sure that the materials of your coats and warm layers are flame resistant.
There’s a reason that welders usually work in thick metals and leathers, and it’s because they know there is always a risk of fire.
This doesn’t change just because the weather gets cold. This means you need to be strategic about protecting yourself.
Protect Your Welder
You need to protect your gear as much as yourself. You will never be able to create a solid, strong, and dependable weld if your welder breaks down in the cold weather. You must take measures to maintain your equipment and protect it from the cold.
When it gets cold outside, you will need to spend a little more time maintaining your welder than you do in the warmer season. This will prevent your welder from breaking down on the job or producing weak welds.
Make sure you check your oil and change it regularly.
The viscosity of oils is critical to it functioning properly and colder weather will make your oil thicker, increasing the viscosity to the point that it won’t flow the way it should. You need to make sure that yours doesn’t encounter this problem, so you may need a lighter weight.
You also want to cover the machine. You can pick up a welding cover pretty affordably, and this will protect your machine against rain and show hitting the critical inner parts. It works to protect it against UV damage in the summer, which can melt hoses and wiring.
You also need to make sure the ant-freeze is working. Check it regularly and change it when you need to.
This is extremely important in the cold weather because it’s what prevents your coolant water from freezing over and destroying your engine. It also protects the metal from corroding in cold weather.
WD-40 will be your friend. A thin layer across everything inside and outside your welder will make things run smoothly. In the winter, the humidity changes in the air and it may cause your welder to rust or corrode if you aren’t maintaining it.
You also need to check your hoses. In the winter, they get more brittle and cracks will start to form.
If you have any hard and brittle hoses that are showing cracks, you will need to replace them. Do not wait until they fail entirely, or you will regret it.
Finally, take care of your fuel. You will need to treat it with some stabilizers during the cold months.
This is especially true if you are not planning to use your welder for a week or more. The stabilizers will prevent the fuel from freezing over or thickening too much while the machine is not in use.
Make Sure Your Rods Are Dry and Warm
In the colder weather, stick welding is the best choice because of how portable it is. It’s also great for thick metals in situations that aren’t ideal. This process is pretty simple, but the weak point of the process is the welding rods.
You must give them special attention when you are welding in the cold. It is critical that the welding rods remain both dry and warm to produce a strong weld. This means you will need to take special care of them.
If your rod gets wet, then the shielding layer is going to fall off or crack as soon as your arc heats up during your weld.
The water vapor will also contaminate your weld as soon as it gets introduced to the arc’s heat. The result is a contaminated weld that has no shielding for the weld puddle, which will lead to even more problems with the weld.
The good news is that there are ways you can keep your rods dry and warm. You can use a rod oven to keep them warm and dry when you need to.
There are tons of affordable portable welding rod ovens available. If they’re not an option for you, then make sure that you purchase dry storage containers.
Frequently Asked Questions
We hope that we have covered most of what you will need to know when it comes to cold weather welding, but here are the answers to a few more questions that are asked when it comes to the topic.
What do you do if your weld cracks in cold weather?
If your weld is cracking, then you are probably not getting proper penetration and your base metal is too cold.
You may want to start over again. In the meantime, you need to take a break and warm up your base metal.
The reason you have cracking is that your weld is cooling too fast after being applied, so you need the base metal to be warm enough not to immediately cool when you remove the welding arc.
How warm does the base metal need to be in order to weld without heating it up?
It is recommended that you have the base metal maintain a minimum of 50 degrees Fahrenheit before welding in the cold.
Conclusion
Are you welding in cold temperatures? If so, what are you going to do to protect your welds? We hope this article has left you with some great ideas.