How to Set a Welder for Spray Transfer
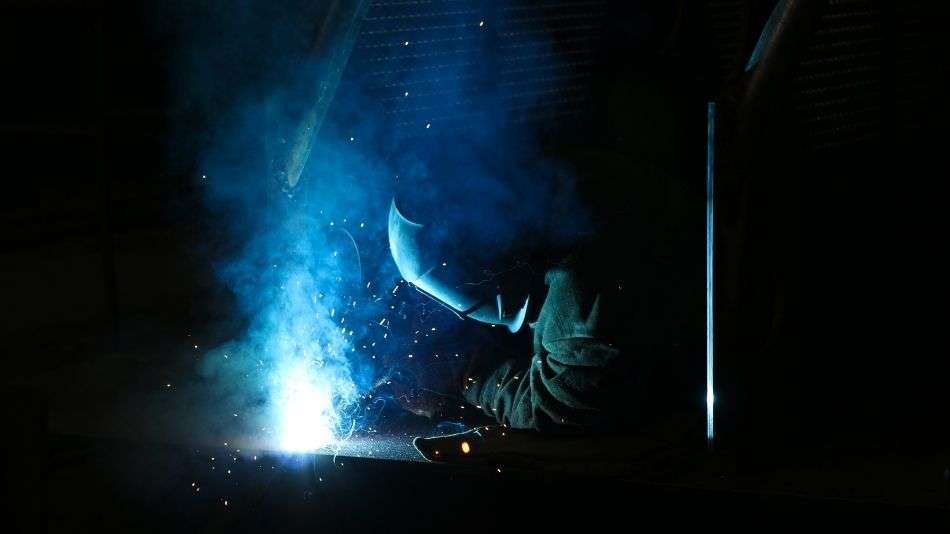
Welding is a form of art that is overlooked by most people. It is still a rare skill set; the average person has little to no experience welding. Academies, community colleges, and technical institutions will all offer skills on how to perform different kinds of welds.
Welding takes a great amount of precision and skill to be successful. There are many different techniques to perform a successful weld. Sometimes, setting a welder for spray transfer is the best solution.
The technique of spray welding consists of spraying a continuous amount of molten drops that are usually much smaller than the arc itself. The arc is continuously on and running during the spray welding process. A voltage higher than 24 volts is used to aide in this process.
Spray welding typically leads to a beautiful weld, and when done properly, makes a very strong pool during the process. Best used on thicker materials such as heavy plates, spray welding can save the common welder quite a bit of time.
The process goes quickly, and it is definitely an asset when on a plant or assembly line. By training employees to use this method, and providing them with the proper equipment, the welding process can become much more efficient. While not overly complicated, there are important things to know about the process.
There are many different reasons a welder would want to use a spray transfer method. Different materials that are being welded constitute the use of this method. Also, there are several important considerations when setting up a welder for this kind of welding activity.
In weighing the pros and cons of a spray arc transfer, there are also many different methods that have to be followed for a good result. Setup, materials, skills, and mathematical equations are all very important parts of the process.
Setting a Welder for Spray Arc Transfer
One of the benefits of setting a welder up for a spray arc is the higher speed of production. Wire speed controls not only amperage but also the penetration of the weld. To find the proper speed, the wire size should be multiplied by the number of inches per amp.
For example, the size of the wire is .023 inches. It should be multiplied by 3.5 inches per amp. If a person is using 1/8 inch wire (or 125 amps), the equation will look similar to this:
3.5 x 125 = 437.5 inches per minute. That is the correct way to set the speed of the wire feed.
For a second example: The size of the wire is .035 inches. It should be multiplied by 1.6 inches per amp. If a person is using 1/8 inch wire (or 125 amps), the equation will look similar to this:
1.6 x 125 = 200 inches per minute. That is the correct way to set the speed of the wire feed.
Much of welding is all about math and the precision of setting the machine. It is important to check and double check that the math is correct, and the settings are perfect before beginning the process. When in doubt, there are many online forums that feed off of the experience of different people in the welding community.
Running higher voltage is also an important consideration when using the spray arc transfer process. There is a rule to follow here as well. The number of amps directly correlates to the diameter of the wire. There are many charts available to assist with this information.
What is Spray Transfer
Spray transfer is a welding process that requires a considerably high amount of voltage. The arc generally has no popping to it and burns considerally hotter.
To see spray transfer in action, one could picture an arc consistently burning, sparks dropping randomly and rapidly, and fast movement than most other types of welds.
The high amount of voltage must be able to be handled by the model of the welding machine being used. If a machine is overloaded, tragedy can happen. The welding machine should always be grounded and the proper settings dialed in.
Spray transfer is the welding art of spraying a continuous amount of molten droplets onto the surface being welded. Typically, these drops are much smaller in diameter than the wire itself. This leads to a “spray” effect.
Reasons to Use Spray Transfer
Spray transfer has very good rate of distribution, meaning more of a weld is conquered in a smaller period of time making for easier passes. Spray welding has high deposition rates as well. Good fusion and high penetration are also some of the benefits of spray transfer.
In terms of looks, spray welding usually leaves a considerably flat, smooth, and clean design once cooled with minimal spatter. If a person has a large diameter of the wire, this especially constitutes using the spray transfer method. This is due to the fact that the droplets being sprayed will be much smaller.
By having smaller, tighter droplets, not only is the weld generally stronger, but the imprint left behind is usually one that is sought after and professional.
However, to be successful, the welder needs to take the time to learn the technique and properly set the machine. By considering each step of the process, there will still be a splatter effect, but it can usually be kept more minimal.
Being precise enough to use this method takes an ample amount of time. Once the method is mastered, it can be one of the greatest tools in a welder’s skill set.
Some materials require the use of spray transfer to be welded effectively. Materials such as heavy plates and aluminum constitute the use of spray welding.
The thicker the metal, the more the benefit that spray welding has. Oftentimes, in high volume production, spray welding is a must to use time more efficiently.
Reasons Not to Use Spray Arc Transfer
While spray arc transfer can be very useful in welding, there are many reasons not to use the technique.
Smaller materials may not constitute using a spray arc technique. The higher voltage could easily melt the more brittle materials.
Excessive splatter can also occur when using the spray transfer method. This can make weld pools very unpredictable. Also, the end result may not be eye appealing for a solid looking weld.
When welds are not just part of the project, but also exposed to the human eye, it is important to keep clean pools and welds.
This way, when they are covered or painted, the piece will look proper. Spray welding may not always be the best method, as the small droplets are known to scatter about.
The spray transfer method also requires precise detail in setting the machine and using the proper diameter of wiring. If the machine is improperly calibrated, the technique will never work.
There are many guides available showing how to program the welder to get the best result. These formulas have been perfected by many experts in the trade and should always be considered.
Having the correct welder is also a requirement. If a person is only equipped with a small, less professional welder, it may not be able to produce a big enough amount of voltage to constitute spray welding.
Final Thoughts
There are many different training courses available to become a successful welder. Different techniques will be taught and practiced with.
These courses can be found at trade centers or local community colleges.
It is also important to always have the proper safety equipment when welding. A welder’s shield, gloves, and flame retardant clothing are all great assets. Extreme caution must always be used when welding or around one who is welding.
It is important to always consider the machine used for the welding process, especially in spray arc transfer methods.
The machine should be able to be set precisely to form these specific and precise welds. The material should always be able to withstand this type of welding.
YouTube is a great place to consult on different visual welding techniques. From fine tuning the settings on the machine to the actual hands on technique, visuals are a great way to get started. It is important to always follow the proper procedures.
When figuring out whether or not to use a spray welding technique, a person should ask themselves what they are welding, the type of equipment they have, and the timeline they are on.
Spray welding can be a great time saver and a beautiful technique of welding. However, it is not properly suited for every application. While it is strong, it oftentimes can lead to a chaotic weld in terms of looks.