What Are the 5 Basic Types of Welding Joints – A Beginner’s Guide
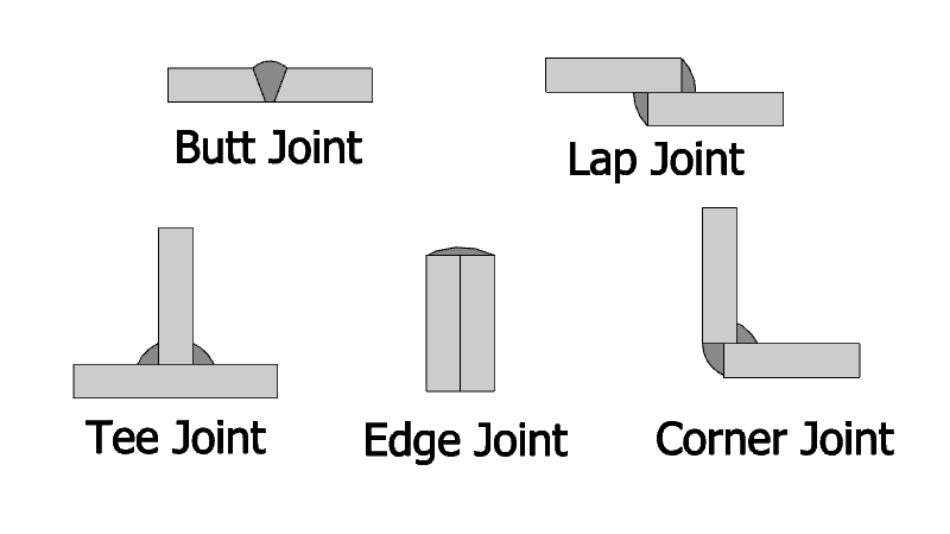
Welding is a fantastic skill to learn. Whether you’re a hobbyist working on DIY home projects or looking for a professional skill that will never go out of fashion, it is a great plan to learn to weld. Once you’ve picked a technique, you need to master the positions and learn how to properly weld a variety of different things.
What are the 5 basic types of welding joints? The five basic weld joints are the butt joint, edge joint, tee joint, lap joint, and corner joint. Each joint has a specific purpose to help you get the most strength for each weld you make.
This article is going to cover the 5 basic types of welding joints. We will talk about the different kinds of weld joints in-depth, so you know what each weld is and how to accomplish it. On top of that, we will detail the situations in that you will use different kinds of weld joints to finish your project, so you’re ready to get the jobs done!
General Advice for All Joints
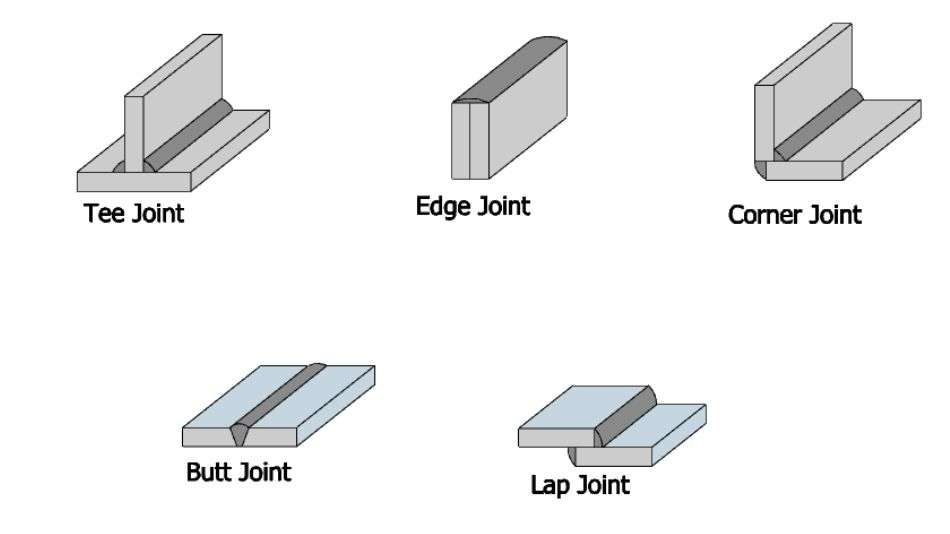
You will need to be sure to cut and grind your parts properly. Using an angle grinder and making cuts will help. A horizontal band saw is the best option. They are versatile and make precise cuts.
Next, you will need to clamp your work. This will hold your base metals together so that you can tack them. There are a lot of different clamp sizes, so you can be sure to find one for any of your needs. You want to check your joint properly to make sure that you are keeping your materials where they need to be.
Tacking your weld will be crucial to a strong finished project. This will prevent your material from distorting in the heat. When your heat fluctuates, your material will expand and contract rapidly, causing your beads to shrink and causing your material to shrink toward your weld bead.
Alternating which sides you use when you tack will reduce the likelihood of your metal deforming.
Tee Joint
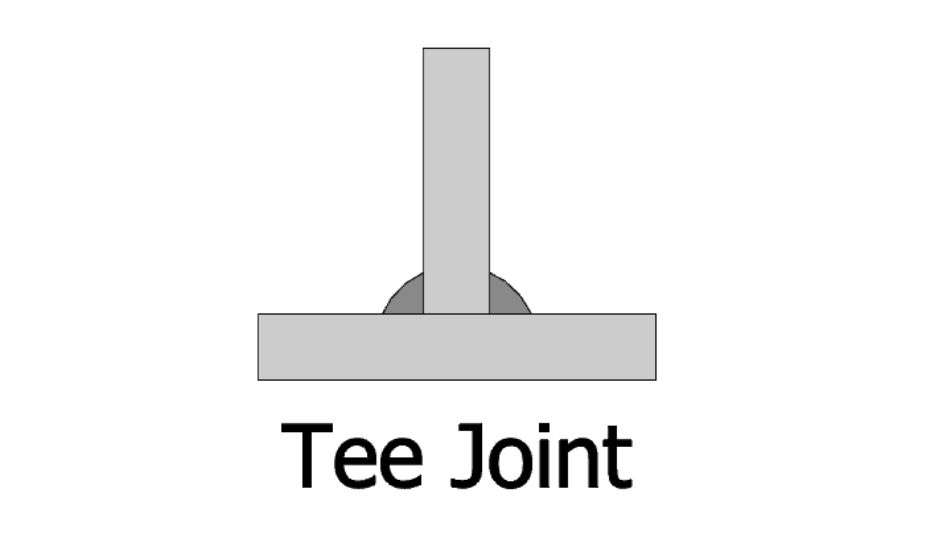
Tee joints are named such because the 2 pieces of metal intersect at a 90-degree angle, which makes the joined edges come together in the shape of a T. These are a type of fillet weld, but they can also be created with piping and tubes that get welded onto base plates. For these welds, it is important to ensure effective penetration.
A tee joint is similar to a lap joint but the two workpieces are not on the same plane. This will require extensive fixturing to perform, especially if your joint can’t stand on its own.
These joints use fillet welding, which is the process of joining pieces together whether at a perpendicular position or angle.
You simply change the position of your torch against the material for this to ensure penetration. In a tee joint, the weld bead won’t penetrate all the way through the base material.
How do you weld a Tee Joint?
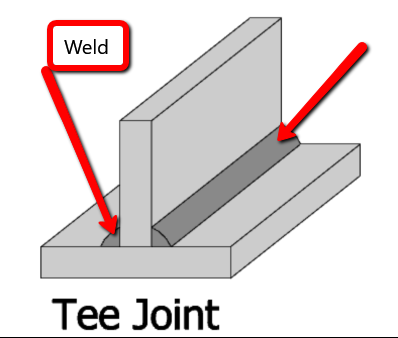
This weld can be created using several different styles. Plug welds, fillet welds, bevel-groove welds, spot welds, flare-bevel-groove welds, J-groove welds, and melt-through welds can all create Tee joints.
This joint is created by fusing together two plats at the right angle to each other. You only need half the angle of preparation that is required for butt joints. There are some different ways to accomplish these joints.
Plain tee joints need very little preparation. They simply require that you clean the end of the vertical plate and the surface of the horizontal one. A single beveled joint can be used on heavy plates as long as you weld from both sides. Single J joints are used for thick plates (over 1 inch) where welding is done from the side.
When you weld tee joints, you need to make sure you fully penetrate the root of the weld. You can do this through the root openings between the ends of the vertical members and horizontal surfaces.
Fixturing this joint is important because of the thermal expansion and contraction of the metal. Once the metal solidifies, it will contract on itself and pull the upright piece downward into a smaller angle with the horizontal piece. It can be prevented by fixing the pieces with a clasp or clamp.
For these welds, magnets like these will do well to hold your material square to each other while you make your tacks. Just remember to check your square between tacks. First, tack the ends, placing one on each side of your tee. Then, finish a tack in the center then tack the opposite sides of the tacks.
This motion will be different. You will use a rounded zigzag for this so that the edge of the base material melts as you run your weld puddle over the joint.
Beads should be run in sections along the joint, and you should alternate from side to side, working your way toward the middle of the joint from the back and front alternations.
The proper weld will form an even triangle shape between the pieces of metal.
What situations would you use this weld in?
You can use this joint to weld plates that are up to 3 mm thick. It is used for things like stands, stiffeners in arc rafts, and other similar things.
Butt Joint
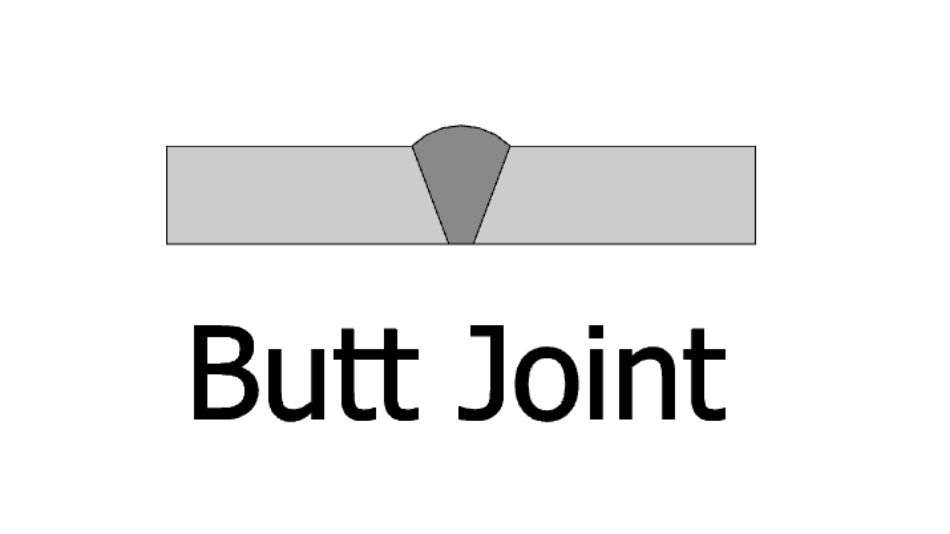
A butt weld is a joint that welds around the circumference. It is the most common type of joint that gets used in pipe welding systems. This is also the most common method of joining pipes to themselves, fittings, flanges, valves, and other types of equipment.
This technique is used in situations where a quality weld is necessary. These welds hold up exceptionally well against X-ray examinations. Plain bevels are the most common type of this technique, followed by compound bevels.
How do you weld a Butt Joint?
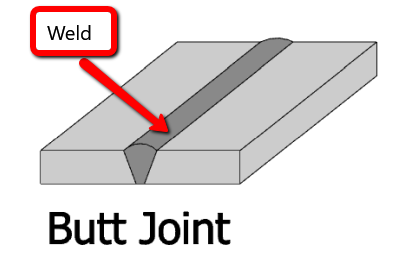
For piping, especially when fitting and flanging needs to be chamfered at 37.5 degrees, it should be flared on a small upright side. This may not be the strongest joint, but it is one of the most useful.
The edge of metal can absorb heat faster than solid surfaces do, so you need to modify your technique when it comes to butt welds. Regardless of the welding method you use, you need to move your electrode quickly around the area of the weld.
This will avoid burning through to your base metal piece. Stick welders can use a stitch welder to move the electrode in and out when pulling the trigger. Other methods will simply need to use caution.
When you properly weld a butt joint, both sides of the metal should have to bead visibly. You can ensure this by clamping the pieces together with a uniform gap in between.
This can hold the sheet metal slightly apart, resulting in better penetration. It will also help prevent the metal from being warped and prevent moving away from the heat.
The first step to welding butt joints is to tack the weld along the entire length of your joints. You want to weld every few inches, When you finish this tacking at a uniform distance, go back over and ill in more welds between the first set you laid down over the joint.
Next, ensure that you have welds about an inch apart along your entire joint. This technique will prevent irreparable distortion, but could still require you to hammer out minimal distortion afterward.
You can use a weave or zig-zag pattern to weld or a circular one. This will help with thinner metals but you end up with a wider bead than you’ll actually need. You need to practice your angles and travel rate before you move on to anything important.
One common mistake is to pile on too much of a bead on the top side of the joint to prevent burn-through.
This is usually because their weld wasn’t hot enough or because their electrode was too far from the base metal to penetrate properly. The bead needs to cover both edges of the work, preventing the original edge from being seen.
Square butt welds are the most common type. This is what happens when 2 flat pieces of metal are up against each other. This is especially effective for TIG welding and thinner metals.
This method won’t work if the metal is thicker than 3/16 of an inch because it won’t get a deep enough penetration and the resulting weld will be weaker.
Bevel (or Double V) joints are another type of butt weld. This is the type to use when your metal is between ¼ and ¾ of an inch thick. Grounding down the edges of these pieces creates a grove for the weld to sit in, which will allow for more surface area for the weld to bond the two panels together.
The third butt joint is a double bevel or a Double V. This is the strongest possible type of butt joint. This joint will be used in areas that require a strong weld.
Usually, for structural repairs, strength isn’t quite as critical but when you weld a butt joint properly it will have a nicer-looking repair with less filler and grinding required. This will also last much longer than shoddy work.
Prepare the bar for welding by grinding off the mill finish. This will protect your steel from rusting while you transport it to your workspace and prevent contamination in your weld.
Bevel your edges before welding. Two bevels on the joining edges create a little valley that the weld pool can form in, which will ensure full penetration in butt welds. When you complete your tack weld, you can position your electrode to stick out of the gun between your bevel valley and the angle grinder.
Don’t let your wire be touching the base material. Only squeeze the trigger for two seconds before completing the tracking loop.
Repeat the tacking, alternating sides so your heat spreads evenly until you have the tacks spread about an inch apart. Run the beads across your joint.
To do this, connect your tack to the outside edges then work back towards the center. Start from the bottom and move upwards, pushing the weld with the tip of your gun. If you’re new, just weld in the most comfortable direction.
When you finish, you’ll have a bump where your filler material went into your weld pool. You can leave it if you want, but you can also grind it flat if you want a nicer-looking weld.
If there are gaps near your weld from grinding, you can tack, where you didn’t manage the right penetration then grind the material back down again.
What situations would you use this weld in?
This welding technique is great for pipes. It’s also good when materials may be thicker than 3/16 of an inch. It is pretty commonly used in automotive repair work.
Lap Joint
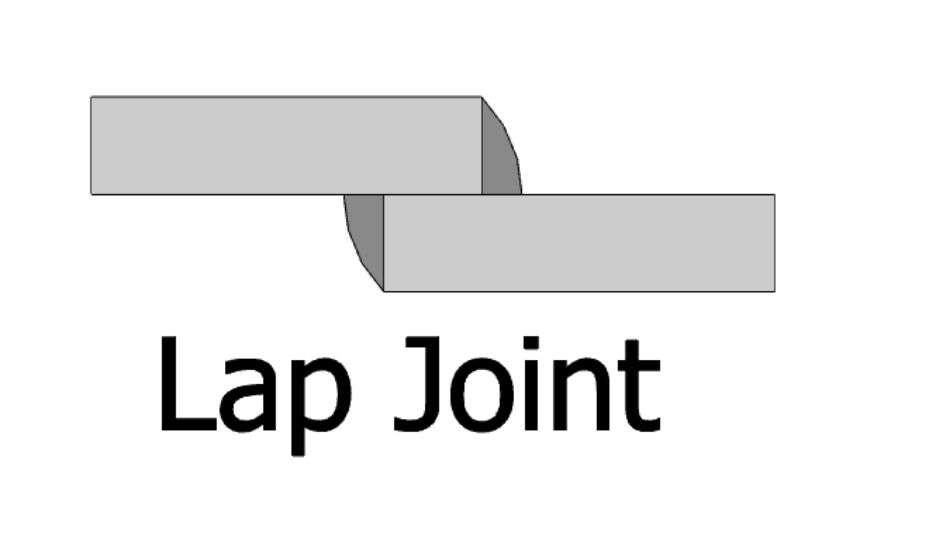
Lap welding joints are used to join metals of different thicknesses together. These are fillet types of weld and can be made to one or both sides of the joint. These joints are so named because one piece of metal overlaps another piece in the weld.
A lap joint is used when two or more materials become overlapped on top of one another. The edge of one material is melted and fused with the surface of another material. These joints are very forgiving when it comes to part dimensions. The joint is pretty easy when it comes to creating joints.
A well-done lap joint will have plenty of weld bed penetration. The upper edge will melt back and overlay the project. If it melts too much, you’ll end up with a thin or weak joint. Making the weld takes a lot of practice so you want to experiment first.
How do you weld a Lap Joint?
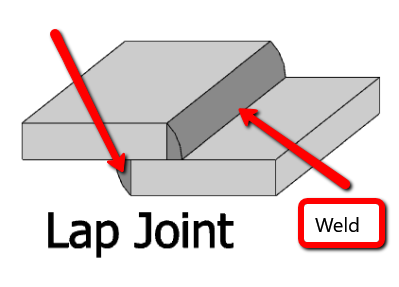
A good rule of thumb to remember for this style of weld is to remember that you should overlap twice the thickness of your base metal.
For example, if you have a quarter of an inch thickness in your plate, you will want a half an inch weld.
Draw a line so you have something to like up, then cut your piece of scrap metal to go underneath your edge. Once it’s flat you can get clamps on tightly.
You clamp the top piece because it gives a little bit of stability, keeping the top piece flat and pushing down onto the bottom piece. This also grounds the table, giving a complete circuit so you can weld.
When you weld flux, it will turn into slag. This covers your molten pool and you just need to chip it off when everything cools to get the weld underneath.
This creates a single fillet weld, which is ok for general welding but not very strong If you need it to bear loads. It would be susceptible to damage if something hit it from the outside.
Flipping it over and welding the other side would create a double fillet weld. This is what you call a lap joint. This is easy, quick, and simple. It offers strength on both sides.
When you weld beads onto your lap joint, you want to use a weaving pattern and zigzag back and forth across your joint. This can prevent it from melting too much along the upper edge.
You want to let the melted metal along one edge solidify partly then add more on top once it’s cooled a bit. Don’t let it cool too much though, or your weld strength will suffer.
Lap joints are like fillet joints in that you angle your torch towards the joint at around 40 degrees from vertical and 20 degrees towards the direction your weld is traveling. Clamp together the sheets for added stability.
For lap joints, you still start by tacking your pieces together, but instead of creating a small shape you put your wire consumable electrode on your top piece, squeeze your gun’s trigger, and drag the gun gently toward the bottom piece of your base material. You will be able to see the edge of the top material start to melt away as you do so.
To complete the joint, run beads along your outer edges and work towards the middle of your joint. Your gun’s angle should be pointing into the corner at a 45-degree angle. Your weld pool should be visible as it grabs the steel on your top sheet
What situations would you use this weld in?
Lap joints are great for patching things up together. They can fix a hole that has worn into a cabinet and get blasts running again.
These joints are also used to make iron racks. When shelves get framed, you weld them to the uprights using these lap joints.
These are also great for attaching thin sheets of metal together. Laser welding uses lap joints quite frequently. These are also used in processes that involve automation.
Edge Joint
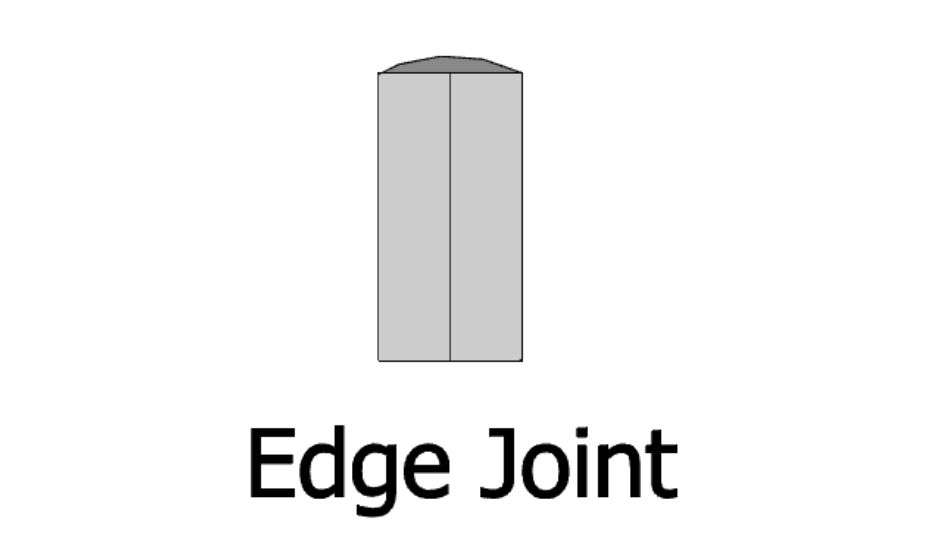
An edge joint will join parallel pieces together. It’s not a strong joint, but it is used mostly for sheet metal. These joints aren’t very strong.
This makes them bad for use with projects that will have to bear a ton of stress or impact. It also makes deeper penetration impossible.
This proves also works on flanging edges. It is used to weld the base edges of 2 different parts.
How do you weld an Edge Joint?
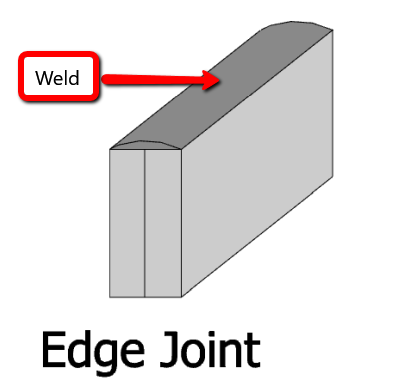
To create this joint, you can use J-grooves, V-grooves, U-grooves, corner flanges, bevel grooves, square grooves, or edge-flange welds.
You need to clamp or tack your weld closed before fusing your joint for this type of weld before you fuse things.
You can maintain the rigidness of your sheet metal by forming a 90-degree bend before the flanges are clamped together to weld. This is what adds rigidity to the structure.
With aluminum alloys, you need to be careful because if you use only the parent alloy along the joint, you won’t get the desired strength. Aluminum requires a fuller metal alloy to make a strong joint.
What situations would you use this weld in?
Because this joint isn’t as strong, it’s mostly used in reinforcement plates. It can be used in flanges of I beams, angle edges, liquid tanks, mufflers, housing, and other areas that don’t need to bear tons of weight.
These welds are also good to build up an edge and replace damaged and worn metal.
Corner Joint
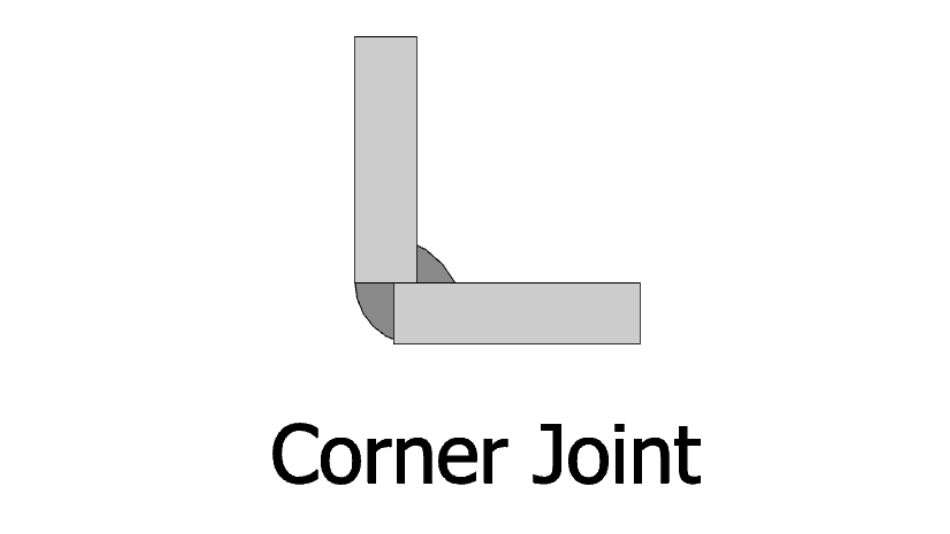
A corner joint only has the corners of your metal plates touching. The angle varies from joint to joint, but it is usually 90 degrees. This leaves a large V space that needs to be filled.
Either side of the joint usually gets welded, but the inside corner is occasionally left without a weld. When this weld is performed correctly, it results in a very smooth and concave finish that is really beautiful.
These joints can be closed, half-opened, or fully open. They form an L. These joints will melt down the overlapping edge so no filler metal gets added. Only a light bead is necessary to make the joint.
How do you do this weld?
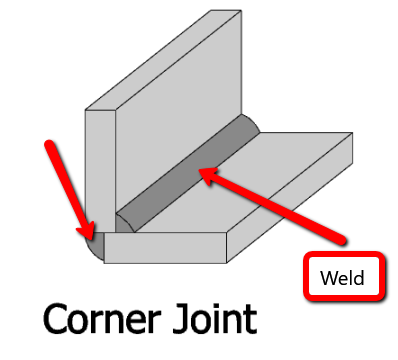
For this joint, you need to brace your corner joints. This will prevent them from pulling out of their proper angles.
You don’t want to use too much heat because that will only increase the likelihood of your joint pulling. Even when you brace this joint, it can still warp with excessive heat.
You will need to find a way to allow the joint to release the stress from the heat.
The strength of your plates will rely entirely on the strength of your corner weld because that’s all that gets welded unless you plan to install permanent braces. This means you will need an impeccable technique.
The good news is that If this joint is flat on a bench it’s pretty easy to weld this type of joint. If you’re using a MIG weld on an outside corner joint, you can do it uphill in only one pass.
Just make sure you set the machine so that it will fully penetrate the root of the joint without piling up too much on the weld.
You don’t want to get undercut or lack fusion in the root of your joint but you also don’t want tons of pileup on a convex weld.
If you’re doing a downhill root or an uphill fill you need to make 2 passes. You need to lower your heat for the uphill pass through the joint.
The 2 pass style of welding will provide a much stronger finish that won’t end up weakening in thermal cycles. Just make sure to polish it and examine it to avoid lamination in the base.
These joints can be difficult because you’re unable to rest your hand on your material to steady your torch. You will need to practice this position and get used to stabilizing your own hand so that you’ll be comfortable when you weld the joint.
What situations would you use this weld in?
These joints are used to join things together in an L. The most common use for this is to construct box frames, tanks, and other similar fabrications.
The closed corner joints are used on lighter sheet metal when higher strength is unnecessary.
Frequently Asked Questions
There are still plenty of questions that get asked when it comes to welding joints. Here are a few answers to some of the more common questions that get asked.
Which welding joint is the strongest?
Each welding joint serves a different purpose, but a couple of them are specifically stronger than others.
The thing that makes this difficult is that your skill will have a lot to do with how strong each type of weld is. A corner or tee joint with a groove will provide the strongest weld, especially when using an arc welder.
The key to making strong welds is reinforcement and penetration. If you make sure to tack properly so you don’t distort your base metal, and you ensure the right angle for deep weld penetration, then your joints should be strong.
What is the easiest welding joint to learn?
The joint difficulty depends on your position and technique. In general, Tee joints and butt joints are the most common and simple types of joints to learn.
Lap joints are also pretty easy to weld, as long as you remember to clamp the base material.
What is the weakest part of a weld joint?
The weakest part of a weld joint will be inside, where there is no material or filler included in the joint. With lap joints, you can mitigate the weakness by flipping the joint and welding both sides.
To prevent weakness, ensure that you are penetrating the joint properly and using good technique.
Conclusion
Which of these weld joints have you tried to use? As you can see, there are a variety of different purposes and joint types. Each joint type also uses different positions and techniques for the strongest possible weld.
To make sure that you are welding your joint properly, you need to study your technique.
Prepare your meal ahead of time and ensure that you’ve got the right technique and heat settings to make nice beads and tacks without melting through your base metal.
Know which joints are strongest and weakest, and how to use each one in different situations.
Now that you’ve finished our guide, you should be a bit more familiar with each of the types of welding joints and capable of using the different kinds of weld joints to finish and repair your own welding projects.