What is a MIG Welder & How Does It Work – A Beginners Guide
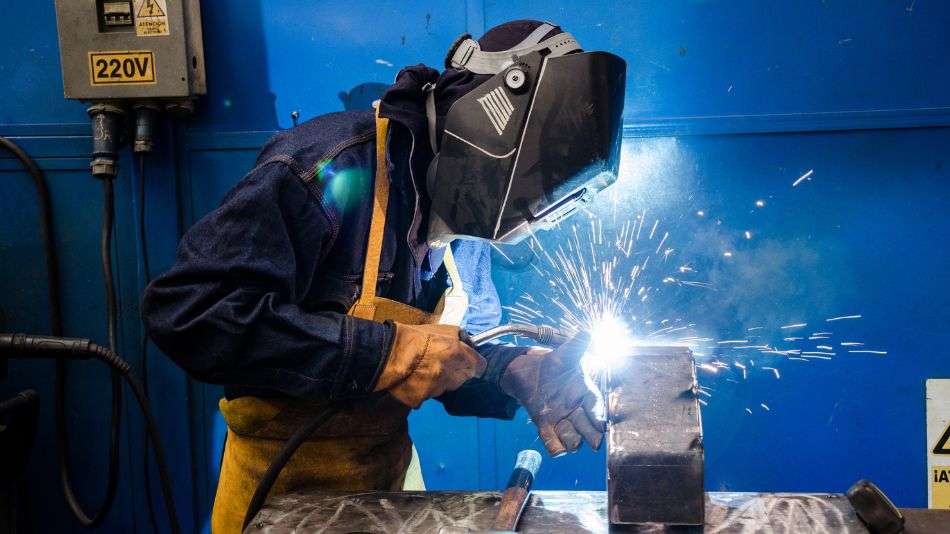
Welcome to welding! If you’re a brand new hobbyist curious about learning to weld, then you have probably heard a lot about MIG welding and have just as many questions as you do answers – maybe even more.
- What is a MIG welder?
- How does a MIG welder work?
This guide will introduce you to MIG welders. We will let you know what MIG welding is, what jobs you can tackle with this method, and how MIG welding works.
We will also answer other common questions. You’ll discover the different methods of welding and how easy MIG welding is for beginners to learn, and you might find out along the way whether MIG welding is the right thing for you to learn!
What is a MIG welder?
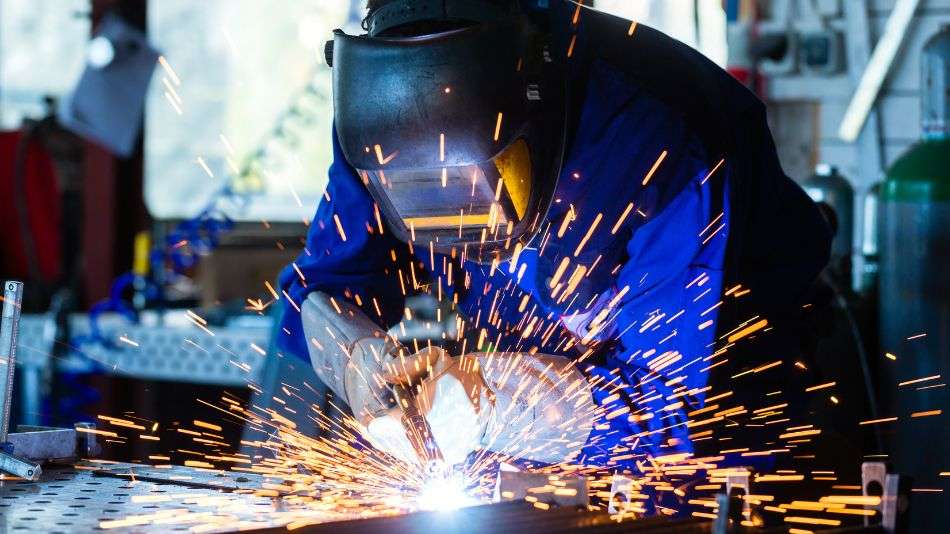
MIG welding stands for metal inert gas welding. It’s a process that uses a spool of wire continuously fed into a MIG welding gun.
This process burns, melts, and fuses two pieces of metal. It is also called GMAW, or gas metal arc welding, on occasion.
A MIG welder is a machine that handles the wire and feeding. The gas shield is what differentiates MIG, TIG, and stick welding. This is created by a flux that releases gas caused by a chemical reaction or a cloud from a tank.
With MIG welders, the tank is usually filled with a mixture of Metal Inter Gas (hence, MIG welding). None of the gases in the mixture will react badly with your weld or add contaminants.
The gas gets pumped through a cable to the lead of your welding gun from the gas tank. It gets released from the same nozzle the welding wire feeds through, creating protection around your arc while you weld.
This wire-feed welder uses metal to create the weld material on a spool inside your welder. The material the wire is made from is determined by the type of metals you’re fusing.
Beginners will usually work with a wire that contains flux inside, which allows them to work without needing a separate gas tank. This will work, but it is less than ideal, and the weld quality will suffer.
The wire gets fed through your nozzle and emerges when you pull the trigger on your spool gun. The wire completes your arc.
Why do we need MIG welders?
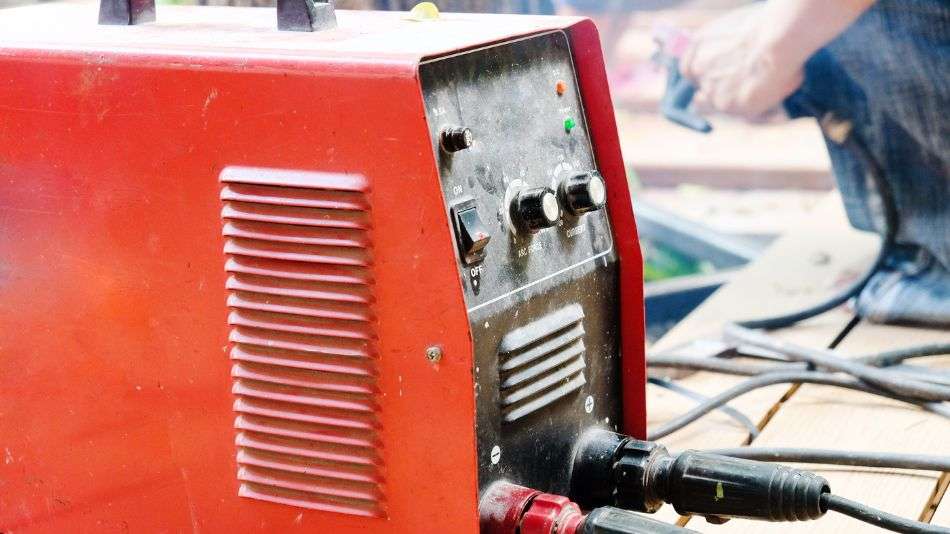
One of the common things that beginners ask is, what do you use a MIG welder for? Here are some of the reasons we need MIG welders.
#1 Heat Settings
MIG welders have several different heat settings, so you can perfectly calibrate the machine to the right power for deep penetration on your weld without burning a hole through your base metal.
#2 Can Handle Multiple Types of Steel
It’s a very diverse process. TIG welding can handle a few more materials but is extremely ineffective on thicker welds, especially when compared to MIG welding.
We need MIG welders because they can handle aluminum, stainless steel, and mild steel on every thickness from 26 gauge sheet metal through to heavy-duty industrial structural plates.
#3 The Wire Feeder
The wire feed also gives it an advantage because it can double as both electrode and filler. This allows thick pieces to fuse without being heated and risking burn-through, disfigurement, and warping.
It uses filler rather than a fusing technique, which also means you can use MIG welding to weld two different types of material together.
#4 It’s the Fastest Way to Weld
MIG is also the fastest type of welding. It’s designed to run continuously over long periods, making it the most efficient and productive form of welding.
Most industrial automated welding uses the MIG welding technique for this reason.
What can you use MIG welders for?
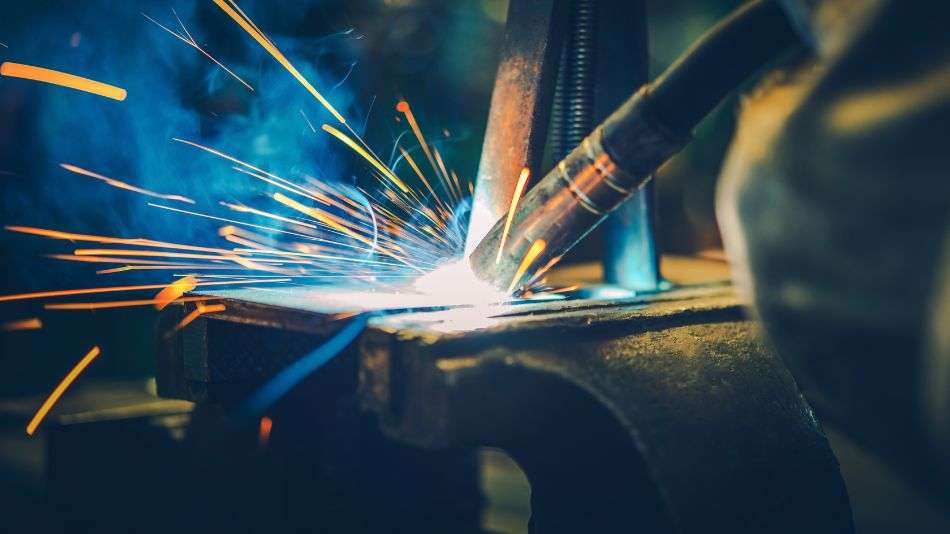
Another common question that people who are new to welding want to know after they answer what is a MIG welder, is: what is MIG welding used for? These are the jobs and projects that MIG welders usually tackle.
MIG welders have a variety of uses. The versatility of this method makes it extremely compatible with a wide variety of uses. This method can handle everything from industrial automation to structural plates to joining different base materials.
MIG welding is very high productivity and quick welding. It’s very easy to use. It can also be used on all types of commercially available metals, including alloys.
MIG welding can be done from every position with the right settings and parameters. It also offers a high-duty cycle and reduces defects during starts and stops.
It offers very deep weld penetration, so smaller welds can have the same equivalent strength as larger ones from other methods.
It minimizes the need to clean up because it doesn’t have any slag on the weld bead and deposits a higher level of metal faster than stick and TGI welding.
It’s great for multiple passes in welding, requires less skill and technique, and has a much lower rate of toxic fumes. This process is ideal for mechanized and automated welding processes.
It produces x-ray quality welds at higher electrode deposit efficiency than other methods.
How does the MIG welding process work?
The MIG welding process uses consumable wire that feeds through a spool to the joint in the metal that you want to be fused.
This uses a MIG welder and gun fueled by an inert gas.
That produces a high arc heat that melts the wire into a bead on your joint, fusing the metals.
Welder
The welder has a wire spool and rollers to push the wire to the gun. If these feed jam, you will want to check this area of the machine.
The large spool of wire should be held in place with a tension nut that is tight enough to prevent your spool from unraveling but not too tight, or the rollers can’t pull the wire.
Gas Tank
There should be a gas tank behind your welder for MIG welders with shielding gas. This will be 100% pure argon o a mixture of argon and carbon dioxide.
Without this gas, your weld will look brown and have splatters. Opening the main valve of the tank will ensure there’s gas.
Your gauge should be between 0 and 2500 PSI inside the tank, with the regulator set between 15 and 25 PSI.
Welding Gun
Most of your focus should be concentrated on the gun while you weld. It involves a trigger that controls your wire feed and electricity flow as you work.
The wire is guided through using a consumable copper tip made specifically for the welder. These tips will vary in size to match the diameter of the wire you’re using.
The outside of the tip is covered with a nozzle that will protect the electrode and help to direct the flow of your gas as it leaves the tip of the gun.
Ground Clamp
The ground clamp serves as your cathode for the welding machine’s circuit. It will complete the circuit that runs between the welder, the gun, and the welding project.
This should be clipped directly to the base metal being welded or onto a metal welding table.
The ground clip needs to make contact with the piece you’re welding to work, so make sure you have cleaned the metal and ground away from any paint or rust that may sit between the clamp and your work.
Safety First
Make sure that you’re observing safety before you begin the welding process.
Use leather shoes or boots, full-length pants, flame-resistant long-sleeve jackets, leather gloves, an auto-darkening welding helmet, and safety glasses. This protects you from metal sparks, spatter, and blindness.
Prepare Your Base Metal
Use a brush to clean your base metal before beginning or striking an arc. Before you begin, you want your piece to be free of mill scale, rust, dirt, oil, or other contaminants.
You should also make sure your work is clamped to clean metal. Any electrical impedance will prevent the wire feed from optimal performance.
For strong welds on thick metal, bevel your joint so your weld can fully penetrate the base metal.
Choose Your Wire
Most projects are welding mild steel. 2 types of metal are commonly used. An AWS classification ER70S-3 will work for all-purpose welds.
If you are welding on dirty or rusty steel that needs a lot of deoxidizers during the process, use ER70S-6 wire instead.
Most welders use a .030 to .045 inch wire diameter for their welds. It’s a pretty good, versatile wire that can handle a variety of different thicknesses across a ton of applications.
For thinner welding base material, use a .023-inch wire instead. This will reduce the amount of heat input and prevent you from accidentally burning through or messing up your weld material.
You can use .035 inch (or .045 inch wire if it’s within your welder’s output range) instead for thicker metals.
Stainless steel and aluminum welds work differently. You will need to perfect your basic MIG technique before being ready to tackle these more difficult weld projects.
Determining Your Gas
You need a shielding gas in MIG welding before you can operate the machine properly.
This will shield your weld area from the nitrogen and oxygen in the atmosphere and prevent these elements from contaminating and weakening the quality of your weld.
There are two types of gas popular in MIG welding. One gas type is a mixture of 75% argon and 25% carbon dioxide. This blend is a great all-purpose shielding gas for carbon steel.
It will have virtually no spatter, produce a beautiful bead, and reduce the likelihood that you will burn through your thinner metals or distort your weld.
Using pure carbon dioxide also works well. This gas allows for deeper penetration in your weld, so it may be a good option if you haven’t mastered your technique.
It also increases the spatter and produces a rougher bead quality, so you’ll need to do some cleanup, and your weld won’t be as aesthetically pleasing.
Set Your Voltage and Amperage
Most modern MIG welding machines will let you pick the wire diameter and select the thickness of the metal you’re using to weld.
This will allow the machine to set your voltage and amperage to the correct setting automatically, so you don’t have to worry about your wire feed speed. These machines are very friendly for beginners.
Weld Positions
You must also ensure you’re using the right technique for each welding position you’re working in and select beginner-friendly techniques whenever possible until you master the skill.
The MIG welding position you choose will depend on where the metal you’re welding is located.
Flat Position: Hold your gun at a 90-degree angle to the metal you’re welding.
The goal is to direct your filler metal right into the joint. Just push it straight in. Use a back-and-forth method if you need to fill in larger gaps.
Fillet and T-Joint: The fillet weld is the most common type of weld. These are called T-joints because they form a T. Your gun should be held at a 45-degree angle for these welds.
You must make multiple passes to ensure you have an even weld bead and prevent undercuts.
Horizontal Position: If your workpiece is horizontal in front of you, you must adjust your welding gun anywhere from 0 to 15 degrees at an angle.
This will prevent the filler metal from rolling over the bottom side of your weld joint. If your workpiece is thick or the fit isn’t great, you must weave the beads to fill the joint. This will ensure that the weld ties in properly to the base metal.
Vertical Position: This position is one of the hardest to master with MIG welding. You have to fight against gravity while you weld. Reducing your voltage and amperage by 10 to 15 percent should help.
You will want to weld downwards for thin materials to avoid melt-through of your weld and base. Start at the top of your joint and move downward. Direct your wire away from your weld puddle.
For thicker metals, you will weld upwards instead. Beginning from the bottom of your joint, you should drag your gun upwards using a weaving motion to help control the size and shape of your weld puddle.
Overhead Position: Overhead welding is also extremely difficult because you are now fighting gravity and your welding gun’s speed.
You must lower your voltage and amperage and use a smaller wire diameter to keep your weld puddle small enough to maintain control.
Ensure you drag or push your welding gun quickly enough to prevent the weld metal from falling out of your joint!
Frequently Asked Questions
We want to ensure we have covered all the bases and answered every question you may have regarding MIG welders.
Here are a few questions that are frequently asked regarding MIG welding that were not addressed in our guide.
What types of welding are there?
There are a lot of different welding methods out there. The most popular types of welding are MIG, TIG, stick, and flux core welding. Other techniques include energy beam welding, atomic hydrogen welding, and plasma arc welding.
MIG Welding (GMAW)
MIG welding, or Gas Metal Arc Welding (GMAW), is a welding method that uses a shielding gas to protect your wire electrode.
This will heat both metals so they can be fused. This welding method requires a constant flow of voltage and a direct current (DC) power source.
It is the most popular form of welding used in industrial situations. There are four ways this process transfers metal: globules, short circuits, sprays, and pulsed sprays.
This welding uses an externally supplied shielding gas. It is advantageous thanks to having very little waste. The efficiency of the electrode requires minimal cleanup. It’s also got lower heat input and fewer fumes. The key to successful MIG welding is properly adjusted power settings.
TIG Welding (GTAW)
TIG welding, or Gas Tungsten Arc Gas Welding (GTAW), works best for welding together thicker stainless steel and non-ferrous metals (like aluminum).
This arc welding process uses a consumable tungsten electrode to create the weld.
This process takes a lot more time and attention to detail than other processes and is so much more complex than it requires both hands and plenty of technical skill and ability.
This process is occasionally called Heliarc welding. This process will allow you to melt a couple of pieces of metal together without filler metal. To create a weld bead, you can still add an external filler rod into the molten weld puddle.
This method also uses an external gas supply; the most common type is a mixture of argon and helium.
TIG welding is great for precision jobs like piping, aerospace, and motorcycles. It’s also great for metal ornamentation and art because of how much detail you can achieve. It’s a great process for welding thin materials and creating beautiful beads. It is also free of spatter.
Although TIG welding is more expensive and difficult to master than any other method, it is becoming increasingly popular due to its clean welds and the insanely high degree of purity from contaminants.
Stick Welding (SMAW)
Stick welding, or Shielded Metal Arc Welding (SMAW), requires welders to follow a manual process. Their stick uses an electric current to create an arc between the fused metals and the welding stick.
This method is popular for constructing buildings and in industrial fabrication to mix iron with steel.
Stick welding uses an electrode coated in flux with the core wire, which is why the arc is created when the contact tip hits the workpiece.
The molten metal is protected from atmospheric contaminants during the process, so it’s great for pipes, construction, and heavier equipment repair.
This is a pretty affordable form of welding, and it’s also very portable due to a lack of an external gas tank. It’s also far less efficient than other methods, with far more waste.
Operators need a pretty high skill level to use this form of welding. Because of the high price, low efficiency, and required skill, stick welding is becoming relatively obsolete. It is still helpful to know the skill because some weld positions make MIG and TIG welding impossible to use.
Flux Core Welding (FCAW)
Flux Core welding, or Flux Core Arc Welding (FCAW), was developed as an alternative to shielding more convenient welding. This uses a somewhat automatic arc weld for construction.
It’s a very quick method of welding, and thanks to the flux core wire not needing a shielding gas tank, it is also far more portable.
This is the closest technique to the MIG welding process, among other methods. Like MIG welding, it requires an electrode to be fed without interruption, but it uses a tube-shaped wire instead of a solid one.
This wire has the flux that will act in a similar method to shielding gas without needing the tank, making it a great solution for windy and outdoor welding.
This technique is pretty efficient and has lower heat and far less waste. It also reduces the number of fumes.
Unfortunately, it generates a lot of smoke, and equipment costs a lot more money. It can create slag and should be avoided when working with thin materials.
This technique is also easy to learn, though. Many professionals enjoy this welding method because of how cheap it is overall. It’s very limited in use, and the results aren’t beautiful, but it’s easy to do.
Electron Beam Welding (EBW)
Electron Beam Welding (EBW) is done by firing a ray of high-velocity electrons toward the materials you want to weld. This sounds like a sci-fi feature, but it is a great technique.
It can transform the energy electrons give into the sheets required for melting welding materials. This allows them to fuse and melt together. This welding is used in many situations, including automobiles, aircraft engines, transmissions, and bimetal saw blades.
This is a vacuum-based process, so it’s a great way to seal off electrical components. It lets you fuse different materials, like those with different thermal conductivities and melting points.
This is something that other welding methods either can’t perform or can’t produce at high quality without immense difficulty. It’s great for mixing thick and thin material.
Atomic Hydrogen Welding (AHW)
Atomic Hydrogen Welding is still used for welding tungsten, though the popularity of MIG and TIG welding methods has largely replaced it.
Tungsten tends to resist heat, but this technique will allow you to weld the material without damaging it. It involved placing two metal tungsten electrodes in a hydrogen atmosphere.
This breaks up the hydrogen molecules and combines them. It creates a mini-explosion of heat.
Is MIG welding easy?
Yes! MIG welding is the easiest welding process for beginners to master. Most welders recommend that beginners learn MIG welding before other techniques because of its simplicity.
While vertical and overhead positions can be tricky, the rest are quite easy with MIG welding.
It is also extremely versatile. MIG welding can handle nearly every base metal type and nearly any thickness. This process can even handle very thick stainless steel or thin aluminum jobs!
MIG welding is also one of the most forgiving methods for beginners still learning the technique.
You can produce high-quality welds with the MIG welding process because it doesn’t require you to know how to use flux, so you don’t have to worry about slag getting trapped in your weld.
This is also the safest process to use. The gas shield will protect your arc from contamination and almost no spatter gets released in this process.
How do I know if MIG welding is right for me?
MIG welding is a great method for nearly everyone. It’s the easiest of all the welding methods for beginners to master and the most forgiving if you make any mistakes regarding technique.
It can be done from any position, too. If you are new to welding, this is likely the right choice.
If you want to automate your welding process with machinery, then MIG welding is also the best way. It’s the cheapest way to weld, too, so this is a great option for budget and DIY home welders.
Conclusion
Now that you’ve learned what a MIG welder is and how it works, you may be ready to start learning about the MIG welding process.
Whether you want to do repairs around the house or fabrication work, you’ll need a great MIG welder to get going. Check out this buyer guide here to learn more about my favorite welders!