How to Ground Your Welder – A Helpful Guide
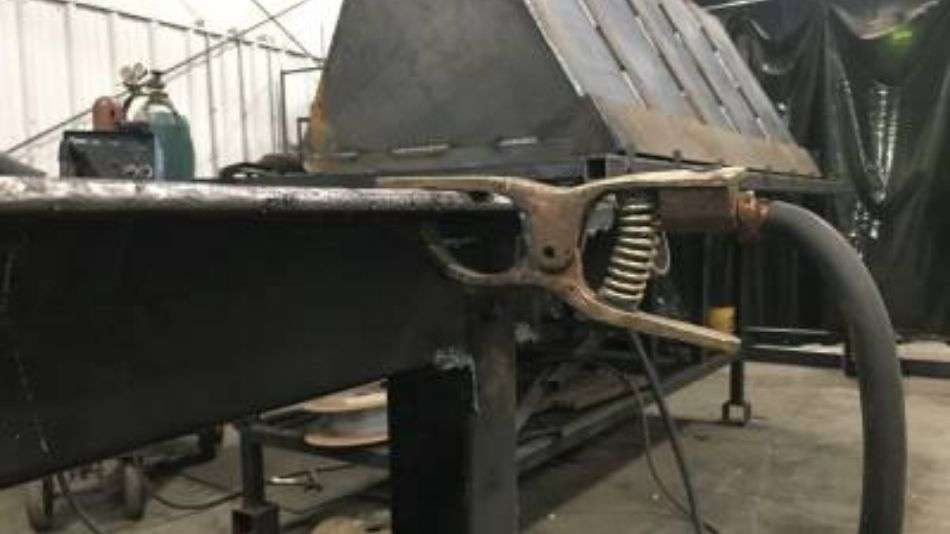
One of the first things I learned as a beginner is that whatever you are welding must be grounded well or your welds, consumables, and everything else will suffer.
So how do you ground your welder? Welders are commonly grounded using a ground clamp typically made of copper or brass. This is done to complete the circuit and allows the welder to create an arc. Without a good ground, it could compromise weld quality, and consumables, or even stop you from welding.
It is vital that you ground your welder before you begin working. If you’re not sure why to ground a welder, keep reading.
This article will teach you all about grounding your welder and answer a lot of questions people frequently ask plus I’ll give you my recommendation for the ground clamp I use. By the end, you will know the best way to ground your welder.
Why do you ground a welder?
Grounding electrical circuits is a pretty common safety practice, and this is the main reason to ground your welder. Maintaining proper grounding within the arc welding setup is vital to safety within the workspace.
Another reason to ground is to improve the quality of your welds. All of your welding currents will pass through the clamp.
This means that if your connection isn’t great, the performance of the welding machine will suffer, which will result in inferior weld quality.
What happens when you have bad ground while welding?
If your clamp is poorly maintained, you will end up with some current either leaking or being too restricted. This results in a decreased output voltage for your welding project. It’s akin to someone changing your settings a bit.
From this point, problems begin to compound. When your clamp has an issue, the broken or problematic area will heat up, which will accelerate the original problem and break down the connection entirely. For this reason, it is extremely important to ground your machine well.
As you can see, it is very important to ground your welder to prevent this from happening. Grounding your welder will keep you safe and improve the quality of your weld.
In fact, welders who purchase their own ground clamps made of superior materials find that they instantly improve the performance of their machines when changing no other settings except the clamp provided versus the upgrade.
Types of Grounding
There are a lot of different types of built-in grounding with welders. Here are a few different ways that the machine works with a grounding clamp to effectively complete your voltage-current circulation and provide for your safety.
Grounding Connectors
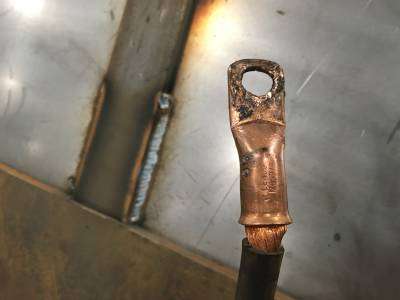
A lot of machines use a setup that involves plugging a flexible cord into an outlet.
A few of them are permanently wired into an electrical supply system with a grounding conductor, but these are rare. Grounding conductors will connect the metal welding machine to the ground.
Tracing the wire back through the power distribution system would allow you to see it connect to the earth through a metal rod in the ground.
When you connect the equipment enclosure to the ground, it makes sure the metal and the ground have the same potential for energy, which prevents you from getting shocked if you touch both points.
Grounding will also limit the voltage on the enclosure, which can help if the insulation on your equipment fails for any reason.
Whatever is grounding your machine has the capability for carrying a current that is coordinated directly with the electrical supply system’s overcurrent device.
This allows the grounding coordinator to remain intact even after an electrical fault occurs within the machine.
Double Insulation
Some machines will have a design that offers doubled insulation. These won’t require a grounding conductor connection because the extra insulation is what prevents you from shock.
These can be identified by a box within a box symbol on their rating plate. It may still be a good idea to use a grounding clamp for added safety anyway.
Grounding Pins in Plugs
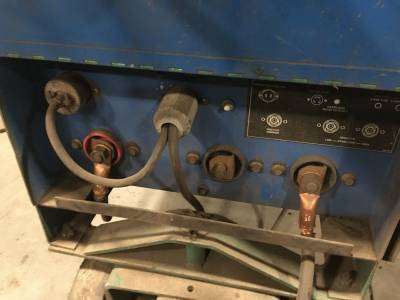
Most smaller machines use a plug on the end of a power cord for operation. In these, the grounding conductor connection happens automatically when the machine gets plugged in.
The grounding pin on your plug will connect to the receptacle. Don’t use an adapter for these because it will undo the grounding and prevent the pin from connecting properly.
You also don’t want to remove the pin from the plug because it is there for a reason. Without the pin, the safety benefits of this grounding conductor are sacrificed.
Test Circuits
If you use a circuit test regularly, you can check for the grounding connector’s continuity.
These check 120-volt circuits and can be purchased for very little money. These will show an indicator light if the grounding circuit is working at that particular outlet.
They can show whether you need an electrician to establish grounding for your circuit.
Workpiece Grounding
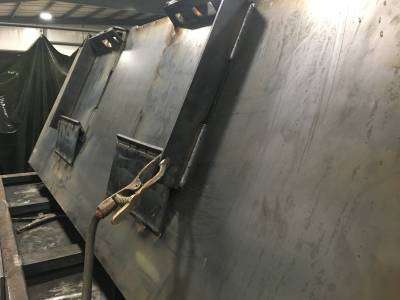
A welding circuit is comprised entirely of conductive material. The current for your projects will flow through this material.
These currents pass through the terminals, cables, connection, gun, torch, electrode container, and the piece you’re working on.
The circuit is isolated from the ground rather than being connected within the machine in the workpiece grounding.
For this type, you connect your piece to a metal table that is grounded. Metal building frames could work, as long as they are separate from the circuit connection your welder forms. This is similar to grounding the machine’s enclosure.
When you ground your piece, it functions at the same potential level as any other grounded object nearby. When insulation fails, the voltage between your piece and the ground won’t be limited.
For this connection, your piece connects to a working cable. It usually uses some type of spring-loaded clamp.
This is occasionally mislabeled as a ground clamp. This won’t bring a ground connection to your workpiece. It simply completes a welding circuit.
High-frequency Grounding
Some machines will start and stabilize currents with high-frequency voltage.
This is used mainly in GTAW machines (gas tungsten arc welding). This voltage will have frequencies that reach the megahertz range despite welding voltages as low as 60 Hz.
These high-frequency signals tend to move away from a welding area. This means they tend to interfere with radio and television reception and can even negatively affect other electronics in the area.
To minimize this issue, you can ground your welding circuit. I use to have this issue in my shop but quickly figured it out that one welder was not grounded out correctly.
Portable Welding and Vehicle-Mounted Generator Grounding
Generators used for remote and mobile welding projects usually supply a range from 120 to 240 volts of auxiliary power.
These generators aren’t connected to an existing power system, so it is often impossible to find a convenient built-in method of earth grounding the machine.
For generators, you should mount your power source to a truck or trailer. Power must be taken from receptacles using a cord and plug. These must have a grounding pin.
The frame of your generator must be bonded or electrically connected to the frame of your truck or trailer.
If you don’t have all of those requirements, you will need to ground your generator as well.
For example, if your generator is connected to a system that supplies power to your house during blackouts, or is somehow otherwise connected to a wiring system on the premises, you will need to ground it.
When the power is hard-wired into your generator and doesn’t require a plug or cord, you also need a ground.
Extension Cord Grounding
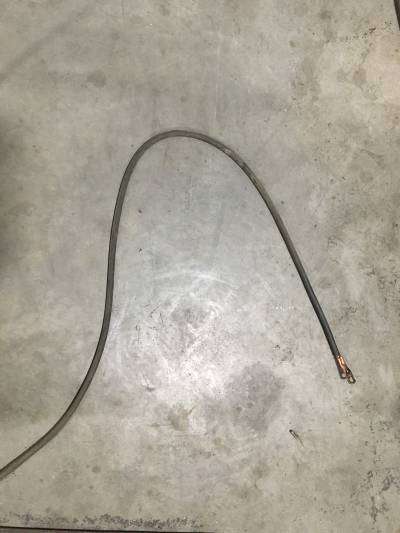
Extension cords need to be regularly rested for their continuity when it comes to grounding.
They take a lot of damage when laying on the ground. Using the receptacle circuit tester can also help confirm that your connections within the cord, plug, and receptacle is all intact and working properly.
How do you ground your welder?
To ground the welder, you simply need to connect the circuit. You do this by placing a ground clamp on your workpiece. Clean metal works best, and it should be close to your piece.
This should have enough conductivity to complete the circuit while also grounding it to prevent sparks and shocks. It helps safety to have a dampener within your grasp, like wood, in case anything happens and you need to prevent the current from running through your body.
Inside a lot of clamps, the grounding strap will hook onto a lug. There’s a contact plate inside on either side of the clamp. There’s also a contact plate. Once the plate burns through, the camp will no longer conduct electricity. Make sure to maintain them properly and replace them before overheating occurs.
Larger clamps are often entirely made of conductive metal, with giant springs and jaw teeth for added contact. Instead of a stud and nut hook for your cable, these are made with a bolt that has a contact pad in the cylinder for your cable. Tighten and squeeze it shut to the ground, so all your tug happens on the clamp rather than the cable so it won’t pull your ground loose.
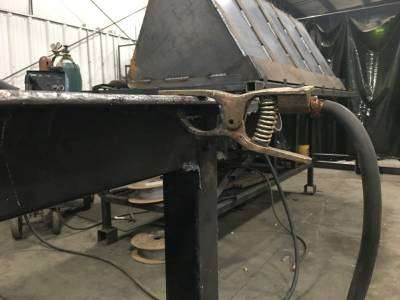
If you’re working from a metal bench, you can just clamp it to the bench or table somewhere clean. You can tuck it out of the way so you don’t trip. The issue is that now your cable has become part of the ground, so if you lean against the cable or work table you may get shocked.
To avoid this issue, hook the clamp to the workpiece whenever you are able to do so. If your piece can’t handle it, then get a giant clamp so you have bare metal to bare metal, then take your ground cable and attach it to this clamp. Then your cable isn’t part of the ground so you can lean on your table.
If your piece is too small for this, then you can clamp it to the bench and ground it to the bench. Just don’t lean against the table. If you do plan to lean against the table, then invest in some welding sleeves.
These will protect you from the heat, from the UV radiation on the weld, and flying sparks, and from the ground if you’re grounded to the table. Pieces of wood and gloves on the table can also insulate you.
Where do you put the ground clamp when welding?
One of the important things to know is where to put your ground clamp when welding. The ground clamp (earth clamp) needs to be attached to the base material you’re welding.
It needs to be close to where you’re doing the welding, too. In fact, you can even clamp it right to the plate you have your workpiece on; just make sure not to clamp it to anything leaning against a wall.
A metal workbench or table would also be a decent place to put your clamp. If your work isn’t touching that metal table, again… just clamp it to your workpiece. The closer you can clamp to the area you’re working the better.
You also need to make sure your eath clamp is on clean metal. If you haven’t prepared the metal it will be a very bad connection. Make sure it’s free of rust and paint. Without this extra protection, you may get shocked and your welding may have poor quality.
You need to use extra care when welding automotive projects. You can’t clamp the ground cable to the heels.
It may destroy the wheel bearings if you do this. Newer cars also tend to have power running at all times, even when they’re sitting idly with no keys or ignition. For added safety, you can unhook the battery before welding or disconnect the alternator.
MIG welding is usually pretty safe, regardless. You just need to make sure that when you disconnect the battery leads, you don’t let them touch the bodywork.
What is the best ground clamp for MIG welders?
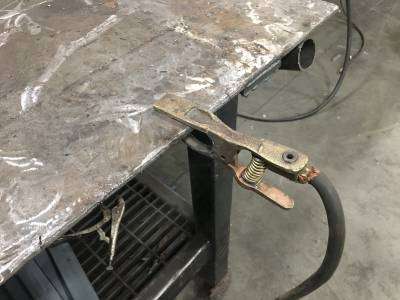
When it comes to MIG welding, I love copper clamps. They’re convenient and safe and the conductivity is pretty high while the corrosion levels are low.
My favorite is the 300 Amp Copper Welding Ground Clamp by Lenco. The clamp is just under 1.5 pounds. It measures 8 inches by 3.75 inches by 1 inch and can handle 300 amps.
This clamp will improve MIG welder performance significantly when compared to the factory clamp these welders usually come with, so you will get better welds.
The clamp is set up for larger wire diameters, so you may need to double your ground wire for a strong enough connection, and it is also a crimp style for added strength. If you don’t have a crimper, then you can always use a hose clamp.
This one is an amazing deal given that it is all copper. It’s made in the USA and is heavy-duty, offering better conductivity at a great price. A lot of professional welders trust it, and we can see why. The nice part about the design is that you can easily clamp it directly to your workpiece!
Frequently Asked Questions
A lot of people have some additional questions regarding grounding their welders. If you still have some questions, here are some answers that may help.
Can you get shocked by a welder?
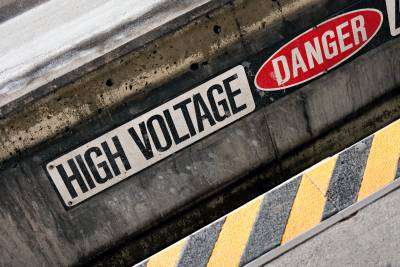
Yes! Welders work with large amounts of electricity. You can drastically reduce the likelihood of getting shocked by properly grounding your welder, but even this doesn’t make it 100% free of risk of shock.
The welding circuit draws energy by voltage. If you end up becoming the path through with the electricity completes its circuit, you will get shocked.
Electricity will always take the path of least resistance when it flows. If you’re dry and on a dry surface, then you’ve got more resistance than the metals you’re using so you’re less likely to get shocked.
Unfortunately, without the ground cable, you may be the only conduit that completes an electrical circuit, in which case you will be shocked.
Side Note: You need to make sure that there is no water near your welding project. Mixing water and electricity is extremely dangerous. Even sweat from your body can increase the likelihood that you get shocked. When you or your clothing is wet or damp it significantly increases the likelihood of a shock.
Another way to help guard against shock is by avoiding the electrode. Don’t touch the electrode because the metal parts of it, along with any exposed wire connectors, will connect the holder to the machine through you. Standing on a metal floor can also increase your likelihood of shock.
You can insulate yourself from this risk with additional safety measures. For example, when you’re wearing long welders gloves, make sure that they are made from an insulating material.
Maintain the insulation across your weld cables, electrode holders, guns, and torches. This will also provide some protection against the insulation. BY maintaining your equipment and extension cords, you can prevent the additional risk of shocks that originate from your electrical system source.
Maintenance and repair are also vital to reducing your risk of shock. Replace any damaged leads at the first sign of cracks or damage. Just remember that you need to turn the machine off and completely unplug it if you perform repairs to any part of the machine itself. This is the only way to ensure that no electricity is present anywhere. Simply turning it off only removes the power to the leads.
If you do end up getting shocked, you should immediately contact emergency medical care. Electrical burns can cause tons of damage that don’t always show up right away.
The good news is that it is extremely rare to receive a fatal injury from welding. As long as you follow safety procedures, you should be fine. Most shocks are also pretty mild, and won’t result in fatality.
Is the ground positive or negative on a welder?
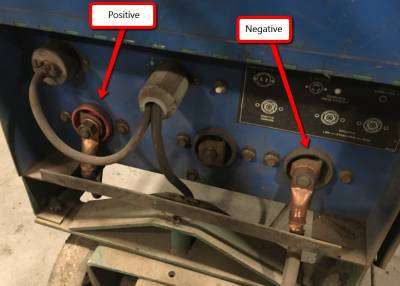
Answer this question requires a look at the terms grounding and work lead. They are often used interchangeably, but this would be a huge mistake to do. They are very different and mistaking them for the same thing can be very dangerous.
The most common sources of power for welding will have a positive stud and a negative stud. You attach your cable leading to the electrode to one of these and then connect a cable leading to a work-lead clamp on the other one.
Determining which polarity is required will answer this question for you. The polarity requirement of the type of welding you perform will run from either the positive or negative stud, and the other one gets grounded.
Side Note: When you’re looking at welding equipment, it is critical to remember that the work lead does not actually ground anything. You must ground your equipment to guard against shock.
This type of grounding and the type we are dealing with in this article has absolutely nothing to do with the positive or negative studs on your welder.
Grounding the machine itself is accomplished through the permanently attached power connection that supplies your machine or by using the separate clamp and wire connecting the case or frame of your machine to the ground.
Sometimes, you will want to use both the plug and the wire connections, but neither of these pertains to the positive and negative machine studs.
Your work table should also be grounded. This process happens by connecting a cable to the tale from a driven rod or the building itself. This also does not factor in the positive and negative studs on a welder.
The term ground refers to protecting yourself and your equipment from shock. The term leads, or work leads, is what pertains to positive and negative studs on your welder.
Neither positive nor negative leads are considered proper grounding when it comes to welding safety. This is why the clamp is used.
Brass vs. Copper Ground Clamp
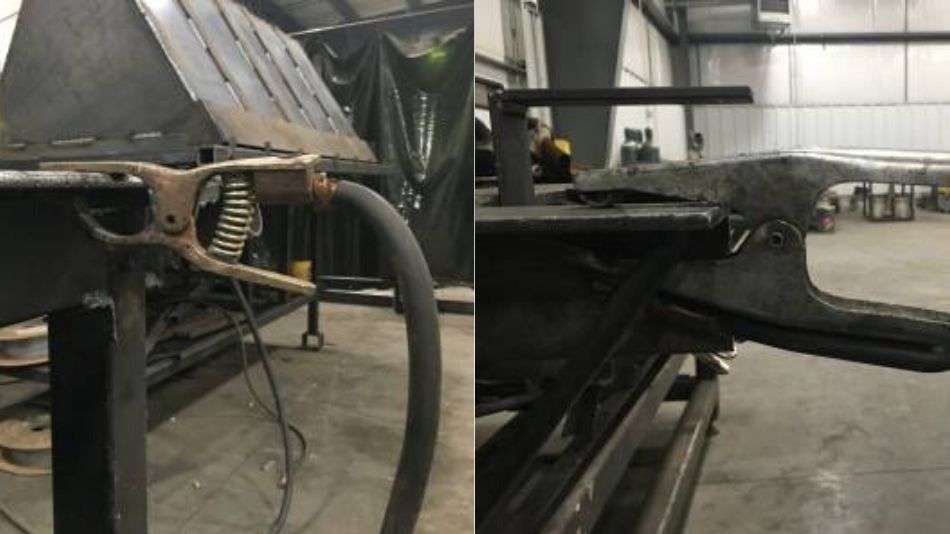
Copper and brass are the 2 best types of grounding clamps. Although zinc used to be common due to its low cost, it is very weak mechanically so clamps cracked regularly. These also have bad resistance to corrosion. Because of these weaknesses, brass, and copper have taken over as popular options. Is one better than the other?
Experienced welders all use either copper or bronze for this because they’re the best metals. When it comes to the two going head to head, tough, copper wins.
If you want to see the copper ground clamp I prefer here is a link to the one I use on Amazon.
Copper is much more conductive than brass (and also more conductive than bronze, the third most common clamp type). Although silver is the best, it is also way more expensive and completely unnecessary when copper does the job well.
Despite this, brass is still used very frequently. Most of the time, copper is hard to find unless it is only used as plating. Most clamps are brass or steel with copper plates.
When it comes to welding, the conductivity difference between copper and brass is insignificant enough that a lot of people like to save money on solid copper by using brass.
Copper is our choice because it’s a good balance. When comparing cost, the resistance to corrosion, and conductivity of copper, brass, bronze, and silver, copper is well balanced. This is why it is gaining popularity and is regularly used in wiring jobs.
Conclusion
As you can see, it is very important to have good solid ground. That’s why I recommend a solid copper ground clamp.
The grounding clamp improves the quality of your welds thanks to increased current flow and performance from your machine. It also keeps you safe and prevents you from being the thing that completes the electric circuit. This prevents you from getting shocked or burned by your welder.
Grounding clamps are very easy to use. You simply clean a piece of metal and clamp it down to complete the circuit. Most of the time, the best safety and quality practices dictate that you clamp your ground clamp directly to your workpiece.
When this is not possible, you can clamp it to a metal table or workbench. Just remember that doing this makes the cable part of the circuit, so you need to avoid leaning on the table or brushing against the cable while you work.
Another important thing to note is that work lead and earth grounding are very different concepts. Both of them are important to the safe operation of your welder, but they serve very different purposes.
Grounding with your work lead will improve your performance and complete your circuit but it will not ground your welder to the earth and mitigate shock risk. True grounding, or earth grounding, connects your welder to the ground so you reduce the likelihood of shocks and lower the potential. It is a critical safety aspect of welding.
Once you master grounding and work leads, you will be able to weld much more safely and may discover that you don’t need to invest in the welding machine upgrade you were considering.
A copper ground clamp may improve your welder’s performance all on its own thanks to the stronger conductivity as compared to factory metals which are usually made from zinc or alloys.